Mold design Tips – Two-Stage Ejecting Structure
Posted on : March 24, 2022 By GREFEE
Generally, when taking the product out from the mold, no matter it applies a single or multi-parts ejecting structure, the ejection should be finished once. However, due to the specific shaped products or requirements of volume production, a two-stage ejecting structure makes it possible to carry out ejection two times, which is very continent in cases in which the molded item can not be taken out old with only one ejection operation. This mechanism is called the two-stage ejection structure.
In order to safely eject the modeled article out, the two-stage ejection structure is a good choice for some products which has a long eject stroke, as it can reduce the ejecting force to avoid defects.
The two-stage ejection structure can be simply classified into three types:
1. Two-stage ejection mechanism of single ejector plate combined.
2. Two-stage ejection mechanism of double ejector plates combined.
3. Two-stage ejection structure of gas/hydraulic.
1. Two-stage ejection structure with single ejector plate.
The single ejector plate combination mechanism refers to the combination of one top ejector pin plate and bottom ejector pin plate. Due to the limits of the mechanism, so the ejecting machine can only perform ejecting once. It must process with the help of other mold structure designs (eg. spring) to carry out the next ejecting.
Classifications of two-stage ejection structure with single ejector pin plate.
1. Cavity and core plate ejecting mode
2. Cavity and core plate pulling mode
3. Ejector pin plate combined structure
4. Floating mold insert.
Below are some design sheets of different designs.
Cavity & Core plate Two-Stage Ejecting
The first stage of ejecting operates when the cavity plate opens, the mold plate (local mold insert) will be ejected out for a short stroke by spring.
The second stage of ejecting works by the movement of the ejector pin plate to eject the molded article out by the ejector pin.
The two-stage ejection is the easiest choice for mold designing, which is operated with spring. The upside of it is only a few extra processed parts, while the downside of it is the shortcomings of spring (elasticity fatigue). To maintain the effectiveness of the mold structure, we need to observe the function ability of the spring and check the first stage of ejecting stoke.
Below are some transforms in the cavity & core plate two-stage ejection mode
Turns “spring pushing die plate” into pushing the “ejecting inserts”.
Shown in the pic above. The mechanism is to push the whole die plate by spring. In application, it can switch to pushing the ejecting inserts according to the appearance and sizes of products. The pic below shows how it works. By reducing the weight that the spring overcomes each pushing to increase the service life of spring.
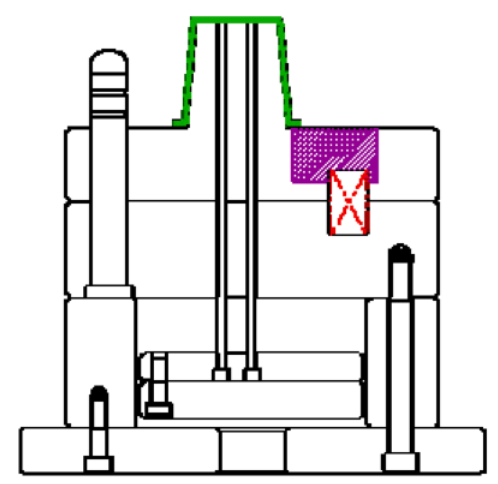
2. If the first ejection stroke is not quite long, Youli glue is also a feasible solution.
Youli glue is an artificial rubber foam material. Its compressing ratio is only about 1/3; unlike the coil spring, the compressing ratio can be like 1/2. It shares some similarities with gas springs in terms of hardness. It will be more solid when pressing harder. While it will be more solid in a short stroke. Its fatigue intensity is worse than coil spring. however, it can work for a long period of time as long as with appropriate lubrication.
The downside of Youli glue is its sensitivity to temperature. It will become hard when the temperature is low, and soft in high temperatures. The user should be cautious of the service life and checks regularly to replace problematic materials.
Two-Stage Ejection in Cavity&Core Pulling Mode
Although It can perform the ejection of stripper plate after the mold opening by spring; however, for a big die base, the force of spring is not enough, so we need other mechanisms to deal with it.
This mechanism is called Tension Links, see pic below:

Simply assemble, the procedures are shown as below:
In most cases, to avoid accidents happening, we will add some extra mechanisms to make sure the original mechanism working smoothly and safely.
The device which assists chain links to work is called the chain.
The cooperation mechanism between chain and chain link is demonstrated in pics below
▲Mold opening
Mold closing ►
Once the stripper has been ejected, perform a second ejection with the ejector structure.
Ejector Plate -Two-Stage Ejection
The two-stage ejection can also be finished by changing the ejector pin.
For the type of ejector pin with two sections, it only increases its strength to avoid distortion in ejecting. We can just add more structures on the ejector plate, which is the simplest method.
The example here is to cut the sub-running gate by this mechanism.
When ejecting, the ejector on the left side will start first till the bottom fixing plate eject and reach the ejector pin which locates down to the right side ejector pin and circled by the red line, then the ejector pin on the right side will start.
At the stage of ejecting sub gates, such a two-stage ejection mechanism can help with preventing damages when pulling the products out from the gate. It works well for the side gate, too.
This eject method is not only used at the time of ejecting around the gates. As the start point of its second ejecting stroke just needs to change the bar length of the ejector pin end. Besides, the mold manufacturing cost is low and this ejecting mechanism suits the ejection of deep box-like stuff.
Summary:
Two-stage ejection is often used at the time of ejecting the molded article out of the mold or the article is difficult to eject in once. Sometimes, the design of the demolding corner is not qualified will cause warping if only carry out once ejecting, which affects the quality of components. It is better not to use double ejecting which not only increases the lead time but also increases the cost. If the pressure is too high, it will cause problems which I mentioned before, while if the pressure is too low, it cannot eject the components out, in this situation, we can try double ejection or can prolong the ejecting stroke.
The two-stage ejection should be forced demolding, which is mainly used at the time when the undercut not working or the inclined top and slider are separated. The two-stage ejecting not only can be used in demolding but also for deeper products or to avoid gate pulling damages.
MORE BOLG
Categories
Try GREFEE now,for free
We keep your uploaded files confidential and secure.