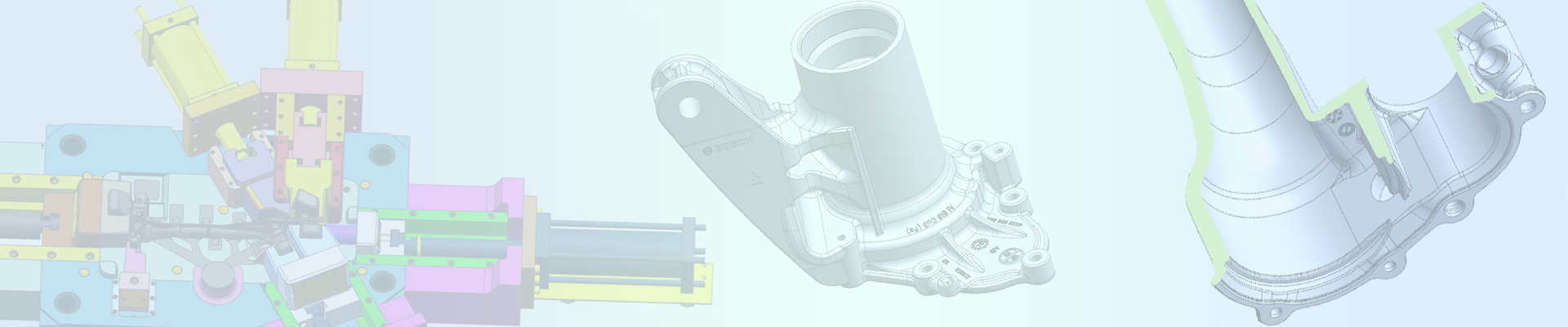
Bosch Automotive Steering Products byDie Casting Process
You can check our case or to start your project.
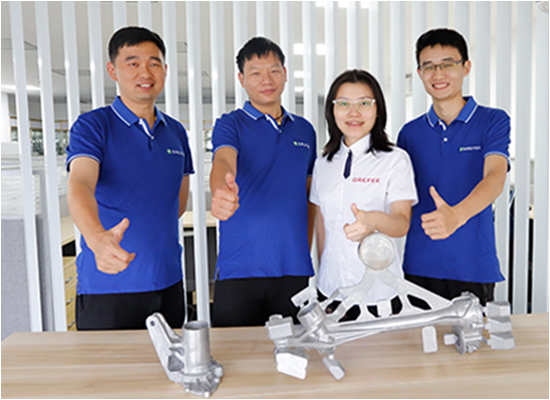
Bosch is one of the most famous industrial enterprises in Germany. It devotes to auto- intelligence traffic technology, industrial technology, combustion goods, and technology related to energy infrastructure.
Based in Stuttgart, a city in the Northern part of Germany, Bosch is a company that has over 230 thousand employees in more than 50 different countries. Its’ innovative and sophisticated product and system solutions make it well-known globally.
GREFEE has been the supplier of Bosch’s multi-color injection molds for electronic tools since 2015 and was highly regarded by the headquarters of Bosch, so GREFEE has successfully become member of the Bosch supply chain. In 2016, Bosch officially contracted GREFEE for die casting services, initially with a test run of a single part to eventually mass producing die casting projects with complex and high requirements.
Now we are going to present the main die casting part of the automotive steering system that GREFEE produced for Bosch in 2021. This article will allow you to better understand how steering products are manufactured and the proficiency of GREFEE in the die casting area.
Characteristics of Project
1.Products have complex parting surfaces, so the strength of the mold needs to be high enough. Besides, it has slides with more than 10 angles, and the core pulling distance is long on both sides.
2.The appearance of products needs to be bright and compact. No blowholes, shrinkage is allowed on the machining surface. No defects such as cold claps, cracks, or shrinkages on the outer surface of products are allowed.
3. The wall thickness is thick and uneven, so the shrinkage of the product and interior air holes inside the product need to be paid much attention.
4. It has rigorous demands on dimension accuracy, so a well-designed clapper is needed in CNC machining to reduce the dimensional errors due to multiple clamping.
So GREFEE usually chooses 5-axis CNC machining. It needs to be performed rigorously following a standardized QC guide for the process of die casting, CNC machining, and post-treatment.
Product name:GEARBOX COVER
Parts Size: | 196X156X168(mm) | Business Type: | Die casting +CNC machining |
Material: | A380(Aluminum alloy) | MOQ: | 10 |
Process: | Aluminum die casting | Place of Origin: | Guangdong,China |
Post Finish: | Sand blasting | Shipping Method: | By Express |
Color: | Nature | File Format: | STP;IGS |
Tolerance: | +/-0.05mm | Brand: | Bosch |
Order QTY: | 8350PCS | Customer: | Germany |
Lead-Time: | 16 Calendar Days |
Product name:Housing
Parts Size: | 572X215X180(mm) | Business Type: | Die casting +CNC machining |
Material: | A380(Aluminum alloy) | MOQ: | 10 |
Process: | Aluminum die casting | Place of Origin: | Guangdong,China |
Post Finish: | Sand blasting | Shipping Method: | By Express |
Color: | Nature | File Format: | STP;IGS |
Tolerance: | +/-0.05mm | Brand: | Bosch |
Order QTY: | 8350PCS | Customer: | Germany |
Lead-Time: | 28 Calendar Days |
Knowledge about Automotive Steering Technique
As a part of the automotive chassis system, the steering system determines the active safety of vehicles. The automotive steering system has two types, mechanical steering system (MS) and power steering system (PS). The latter relies on the power to control the steering system and then switches from a hydraulic power system to an electric hydraulic power steering system (EHPS) and Electronic power steering system.
So far, the most advanced and cutting edged steering technology is steer-by-wire. It is manipulated by a computer on the vehicle that can simulate the feedback from roads or cut off the feedback from roads completely. For the driving mode steering vehicle, it is a helpful technology, improving the driving experience. More importantly, it is also critical for future automatic driving.
At Bosch technology day in October 2021, Bosch showed the steering system equipped with a steer-by-wire steering system. It was a great honor that this product was the work of GREFEE. GREFEE can provide the most advanced steering products for Bosch, and GREFEE feels honored that we can win the trust of Bosch.
Due to uneven wall thickness, complex structures and lots of slides, the quality of the design of parting lines and runners are the key to guaranteeing quality of final products.
Parting Line Surface Design
It is best to pass through the largest section of castings when choosing the parting surface and leave the casting behind the core. The parts which require a high dimension accuracy should be put in one mold cavity. For the sake de-molding and runner distribution, the parting surface of the HOUSING die casing should be the one that passes through the steering axis and is parallel with the moving direction of the slide.
Injection Material Solution
The design of the runner should make the molten metal flow direction follow the cavity venting direction to keep the cavity venting system functioning properly. The overflow tank shall be set according to the needs.
The design of the runner should take the overall product length into account. To assist filling and product feeding, 5 runners are needed for the main product. Besides, as the requirement for oblique holes is high, another single internal sprue should be set for filling and feeding.
The area of runner and calculation of width: Select low filling speed and time to calculate and ultimately select in-gate area which is about 500mm2, and the width of in-gate which is 2.5 mm. It needs to be set up by scientific calculation methods combined with years of practical experience.
It also needs to design the overflow and venting on each far end of the final product. It mainly uses the centralized vent and single vent to facilitate the gas inside the mold cavity and cold material when filling as well as to ensure the quality ( specific design of runner, venting, and cinder ladle should be analyzed according to mold flows).
Mold flow analysis
The runner of die casting products, the cinder sale, and the venting are the three essentials as well as biggest sticking points in the design of die casting molds, so it is necessary to carry out accurate mold flow analysis of parts. Usually, we have to do many adjustments and simulations to find the most rational parameters. Ultimately, the amount of time needed for material to reach different positions of the cavity can be minimized and gas bubbles can be eliminated.
Cooling System Design
This product has a thick wall thickness. The heat concentrates, especially the forming position of the slide wraps the aluminum liquid, so the cooling system is critical in this process.
Cooling methods: designs cooling runners in each core pulling, product cavity is evenly distributed with point cold water holes, set wire cooling water channels in runner position, the spreaders and sprue bush use cooling water channel.
During solidification, the left and right parts are complicated, so the process is slow. The top area of the mold should be cooled carefully.
3D Displays of Mold
core
cavity
The Mold
Dos and Don’ts for Mold process
1.long casting part, multiple holes needs core pulling and forced directly. Mold shape 2836X1909X811 (mm).1250T die casting machine, the core pulling positions of oil cylinder are crossed, stacked. So the long core pulling oil cylinder should be put top and bottom to avoid the interference with die casting machines.
2. Use the core pulling system to achieve the positioning and core pulling action of slide core pulling after the mold clamping. The first thing is to consider the core pulling force and decide the modes of the core pulling system. Due to the long slide stroke, it needs to make sure the slide moves smoothly and some slides have the requirements on movement orders, so it overall uses the oil cylinder core pulling structure to ensure it can process properly on the lathes.
Besides, the core pulling structure is wrapped with aluminum liquid. The holding force should be designed largely due to reasons like hot spot, thick wall thickness and large holding force。 After trial production and have decided the process, the die casting parts can be produced successfully.
3.If it is mass production, then it needs to use imported ASSAB Global 8418 material to make the mold core, fitting for the vacuum heating treatment to ensure the mold life and the stability of production. If the processing is large, the mold fit would be complex. It is important to organize a detailed production scheme in advance.
Key Process Control
The production cycle of each die cast is 74s. The injection amount is 10.23 kg, the filling amount is 6.52kg, component weight is 2.93kg. During production, the operator must follow the practice guidelines strictly.
Operation Procedures:
(1)Strictly following the handover records. The equipment must be checked and registered before startup.
(2)The operator directs die casting process, following the machine process strictly. Important factors: spray painting material, molten metal liquid temp, die casting mold temp, ejector rod oil brushed, parting surface cleaning , and cake thickness control.
(3) Prepares the checklist as production requirements and checked one by one to make sure the preparation is done properly, such as coating material, bolts, cooling water, mist blower, soup feeder etc.
(4) Pre-heat the cold mold with natural gas blowtorch to make sure equal temp. After pre-heating, it needs to apply parting agent on the mold surface and gradually increase the die casting machine working pressure.
(5) After the mold temp is increased to the standard value, increase the pressure for normal production.
(6) After producing 5-10 molds, introduce the cooling water completely.
(7) For local strains and deep cavity positions, we apply manual painting and dry the parting surface and cavity. For strained cavity part, we brush a little parting agent evenly.
(8) It has to observe the pressure gauge of the charging cylinder, pressure booster and nitrogen accumulator. Once abnormal values are found, (pressure drop, no pressure, or insufficient pressure etc), we stop for maintenance immediately and re-start the production after it is normal.
Causes and Prevention of Defects
In production, the professionals must quickly figure out the causes and preventions of defects on the casting.
(1) Roughness: roughness refers to the rough and ragged casting surface, which are surface defects. Such defects result from the damages to casting surface when repairing the mold, or when the coating is too thick, which can start peeling after a certain time after production has kicked off. How to avoid roughness: stop the machine immediately and fix the mold. Practice the spray painting technique rigorously.
(2) Mold repair marks: mold repair marks refer to the attached repairing mark by the operators when the mold sticks to the metal block, which affects the surface of the casting. The reason why is that the operators scratch the non-tensile surface when repairing the mold. Due to corrosion mucus around the gate, the operator scratches the mold during processing. How to avoid it: sandblasting the mold and repairing the mold with sandpaper and grinding tools.
(3) Painting peeling: painting peeling results from the blanking during spray painting. When the mold is eroded, the repairing area easily generates a painting backlog. Too often repairing the mold will lead to mold oxidization and paint peeling. How to avoid it: clean the painting area and add supplementary spray painting.
(4) Damages: damages refers to casting damage due to mechanical impact. Impaired phenomenon: it is because of the ineffective protectiveness of the product in the process of shipment or machining. How to avoid it: a certain distance between products and avoid damages is needed due to the percussion between products. When stacking products, a rubber pad needs to be used to isolate each layer of the product.
The machining design and trial production have guaranteed the steering products being manufactured productively. We control the manufacturing process rigorously and have successfully turned the ADC380 steering gear housing production into a reality. So far, the monthly orders are about 8500 qualified pieces.
GREFEE has almost 20 years of experience in the automotive die casting industry, especially in automotive steering, gearbox, shock absorber, oil pump housing, automobile battery housing…
Bosch has harsh requirements for its suppliers but GREFEE never shies away from the challenges presented. We are proficient in difficult and complex project and are looking forward to tackle yours! Contact Us