Common Issues in the Hard Anodizing

Posted on : July 28, 2022 By GREFEE
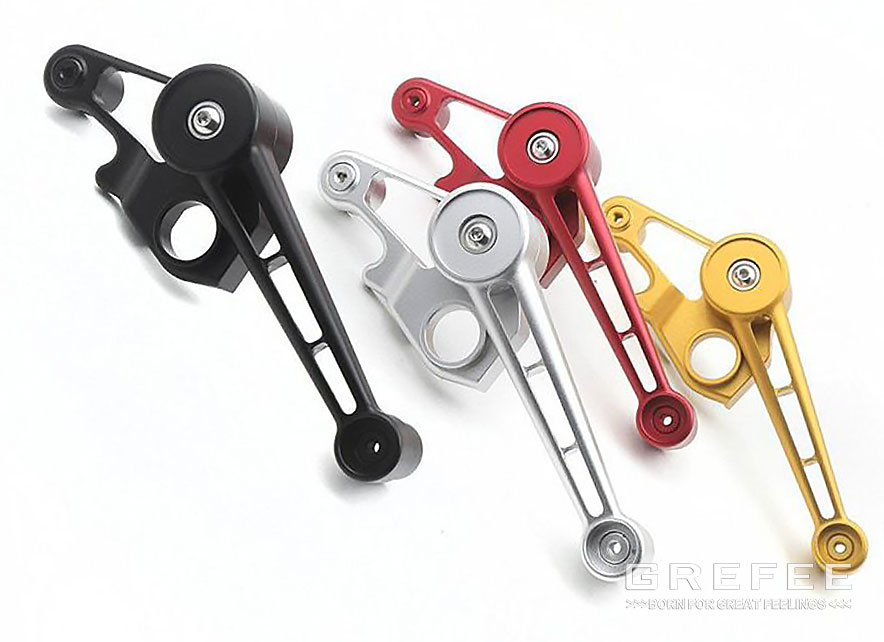
Common Issues in the Hard Anodizing
Hard anodizing is a kind of hard anodized with higher requirements for the wear resistance of the oxide film of the workpiece, which is categorized into: (1) sulfuric acid hard anodizing method; (2) oxalic acid hard anodizing (3) mixed acid hard anodizing. Without specified, it often refers to sulfuric acid hard anodizing.
hard anodizing principles
1. Cathodic reaction:4H+ +4e=2H2↑
2. Anode reaction: 4OH -- 4e=2h2o+o2 ↑
3. Aluminum oxidation: the oxygen precipitated from the anode is in an atomic state, which is more active than the molecular state of oxygen and easier to react with aluminum: 2al+3o → Al2O3
4. Dynamic equilibrium of oxidation in anodic film dissolution: since the oxide file is increasing as the time goes on, the electric current increase will thicken the oxide film. At the same time, due to the duality in chemical performance of Al2O3, it is alkaline oxide in acid solution and acidic oxide in alkaline solution.
Only when the oxide film dissolve in the acid solution can its build speed is higher than its dissolving speed, and it will be thicker. When the dissolving speed equals to the build speed, the film thickness will no longer increase. When the oxidation rate is higher than its dissolving rate, a powdery oxide film is formed on the surface of aluminum and aluminum alloy parts.
Common base materials for hard anodizing:
When producing the hard anodizing, some special measurements are required. For instance: for 2xxx aluminum alloy hard anodizing, to avoid it burning in the hard anodizing process, 385g/l sulfuric acid and 15g/l oxalic acid can be adopted as electrolyzer solution, and the current density should also be higher than 2.5a/dm.
Film thickness of hard anodizing:
The regular film thickness of the hard anodized process is usually within 25μm-150μm. The film thickness of most hard anodizing is 50μm-80μm.
Film thickness of the hard anodizing less than 25um is generally adopted into components, like tooth key and spiral. The thickness of wear resistant or insulated anodize film is around 50um. 125μm thick hard anodizing film is required only in special situations, like high temperature, moisture, high pressure, etc. there is extremely high requirements in products used in sea, medical devices, or environment like high temperature plasma radiation. From the products test to the mass production, which is rigorous.
Besides, one thing that the hard anodizing companies need to know is that the actual film thickness increase is 50μm when producing 100μm thick hard anodizing due to it two way production property.
Moreover, the hard anodizing suppliers cannot neglect that the thicker the hard anodizing film, the higher the outer layer micro hardness (oxide film is more brittle), the higher the film surface roughness.
Function of hard anodizing:
1. High wear resistance: surface hardness up to 500HV.
2. Ideal thermal insulation layer: melting point is 2050 degrees, poor thermal conductivity.
3. Good insulation performance: high resistance coefficient which can breakdown voltage up to 2000V.
4. Strong adhesion: 50% of the oxide film penetrates into the aluminum alloy and 50% adheres to the surface of the aluminum alloy.
5. Superior corrosion resistance: great corrosion resistance in industrial atmosphere and marine climate.
Hard anodized color:
The color of the hard coat anodized surface is generally original color or black. The original color actually include grey – dark grey – brown – taupe – tan, which varies according to its base materials. On top of that, the color is getting darker as the increase of the film thickness.
Difference between hard anodizing and common anodizing?
1.Temperature difference: temperature for common anodizing is 18-22 degrees. With additives, it can be 30 degrees. Too high temperature will cause powder or cracking. Hard anodizing is usually below 5 degrees, which means the lower the temperature, the higher the hardness.
2. Concentration difference: the concentration for ordinary anodizing is about 20% and 15% or lower for the hard anodizing.
3. Electric current/voltage difference: the common oxidation current density is 1-1.5A/dm2, whereas the ordinary oxide voltage for hard anodizing is less than or equal to 18v, sometimes as high as 120v.
4. Film thickness: the film thickness for ordinary oxide film is thin. The figure for hard anodizing is higher than 15μm. Too low thickness cannot meet the requirements of hardness ≥300HV.
5. Surface status: ordinary oxide surface is smooth, whereas the hard anodizing surface is rough (microscopic, related to the surface roughness of the substrate).
6. Different porosity: common oxidation has high porosity; However, the porosity of hard anodizing is low.
7. Ordinary oxidation is transparent film and hard anodizing is an opaque film due to its thick film.
8. Different application sites: common oxidation is mainly used for decoration. Hard anodizing is generally used in wear-resistant and electric resistant situations.
How to control hard anodizing time?
1.Long hard anodizing time will lead to losses and rough layers. Too short will lead to think and smooth film. It can be seen from the above that too short or too long are all bad for quality. Strictly control the time is key, which includes two parts under below.pre anodizing time (take Formula 1 in Table 8-3 as an example). When the workpiece enters the hard anodizing tank, a current of 0.5a/dm2 should be applied immediately, and increases current density from 0.5a/dm2 to 2.5a/dm2 for 5 to 8 times within the next 25min, which should not be too short, otherwise it is easy to lead to short circuit of the workpiece in the later film-forming stage and cause ablation, and long time is meaningless.
2.Anodized film forming time. After 25min pretreatment, the film growth officially begins when the current density has been constant at 2.5 ~ 3a/dm2. Too long or too short forming stage is unfavorable to the quality (the appropriate time is specified in different process specifications).
Reasons for hard anodic oxidation dyeing failure
1.After hard anodizing, timely dyeing is suggested rather than place the workpiece in the water tank long. If is workplace is placed for too long, the workpiece can be placed in the anodic oxidation tank or nitric acid neutralization tank for appropriate activation treatment before dyeing. This improves the effect outcome.
2. Too low oxidatoin temeprature will lead to dense films, so the temperature can be increased appropriately.
3. Inappropriate dyeing material.
4. Poor electric conductivity. Poor contact between the anode copper rod or cathode lead plate indicates poor batch conductivity. Cleaning the anode copper rod and cathode lead plate to ensure good contact.
5. The dye has been decomposed or moulded, and the dye needs to be replaced at this time.
6. Too high pH value of the dye solution. Adjust the pH value to the standard value with glacial acetic acid.
7. Insufficient thickness of anodic oxide film. Check whether the anodic oxidation process is standardized and make sure the temperature, voltage, conductivity and other factors are stable. If there is any abnormality, adjust the specification accordingly. If there is no abnormality, appropriately extend the oxidation time to ensure that the film thickness meets the standard.
Hard anodizing process flow:
Aluminum workpiece → upper hanger → degreasing / chemical oil discharge → cold water cleaning → alkali corrosion → water washing → light discharge / electrolytic polishing → water washing → hard anodizing → hot water washing → deionized water washing → (dyeing or electrolytic coloring → water washing → deionized water washing) → sealing → cold water cleaning → lower hanger → water blowing → drying → quality inspection → oiling → packaging → delivery;
Note 1: hard anodizing takes more than 3 hours overall. The main reason is that the concentration and temperature of electrolyte are much lower than that of ordinary anodizing (the temperature of ordinary anodizing solution is about 20 degrees, whereas hard anodizing is only about 5degrees), leading to slow production of oxide film. What’s more, the thicker the oxide film, the longer the time required;
Note 2: what is different from ordinary anodizing service is that the hard anodizing service has the last process, oiling, which smoothes the surface of the film and makes it delicate, but the sensation of it is oil free in its natural color;
Note 3: the common problem in the blackest hard anodizing is that there will be water stains, for there is water residue in some through holes and blind holes of the workpiece during water blowing. Moreover, since it is not fully dried (too rush and not fully cleaned up). Thus, in the blackest anodizing, ensure to fully dry the part. It is better to dry with oven again to remove the water fully since the residual water stains cannot be erased after a period of time can the workpiece be only reworked. The rework affects the tolerance dimension of the workpiece.
MORE BOLG
Insert mold in injection mold service
What are advantages and disadvantages of Zinc alloy and Aluminum alloy?
Inspection standards for injection molded partappearance
How to judge the quality of your plastic products?
Inspection standards for CNC machining
To ensure that your products are 100% qualified
Categories
Try GREFEE now,for free
We keep your uploaded files confidential and secure.