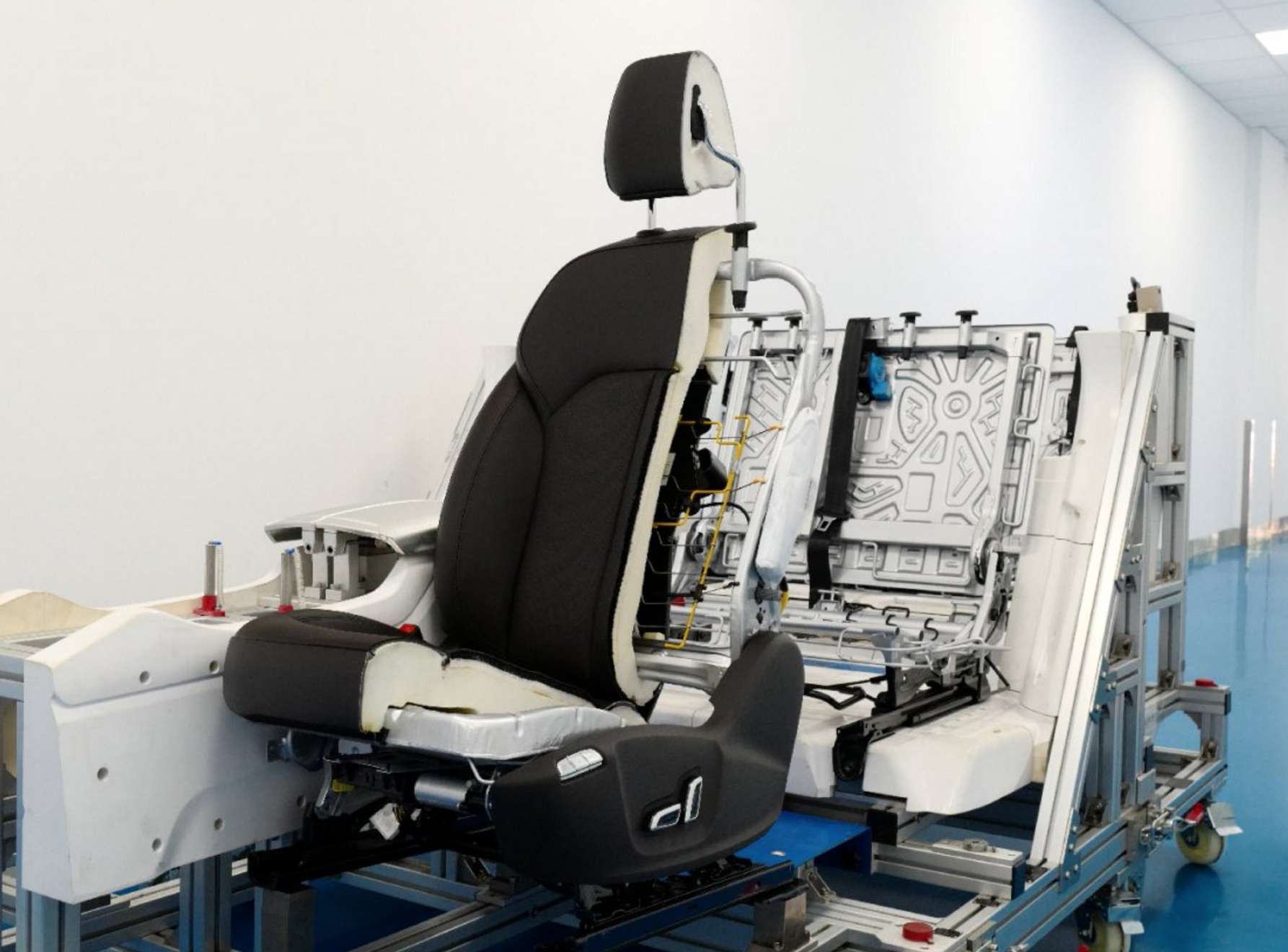
Aston Martin cars are lightweight
Aston Martin car cushion introduction
Writer: Arvan; Role: technology manager
Today, it is about car cushion production that customized by GREFEE for Aston Martin in their process of lightweighting. As an essential part of the automotive, the car seats lightweighting has become the focus of many car companies, especially in the field of automobile racing, for it is an important factor to win in the competition.
Applied processes:foam molds, bending process
Materials used: EPP, low carbon stee
Post processing applied: electronic music, welding
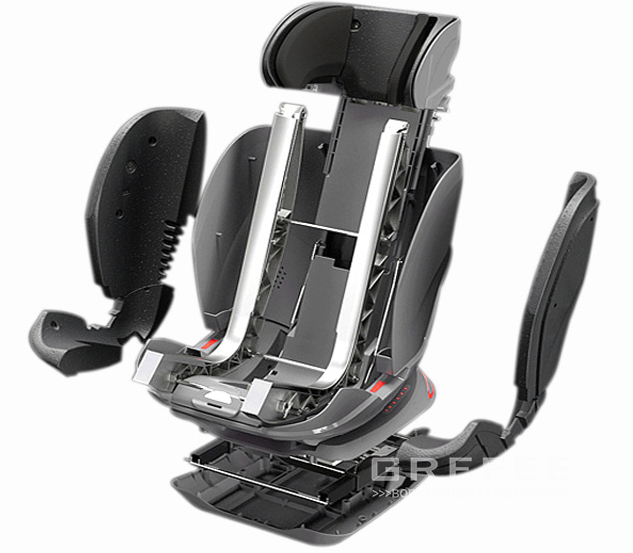
EPP material performance:
EPP, as a high-performance high crystalline polymer and gas composite material, has become the fastest growing environmentally friendly new compression buffering and insulation material due to its unique and superior performance. Products made of EPP is acknowledged with its excellent seismic and energy absorption performance, high recovery rate after deformation, good heat resistance, chemical resistance, oil resistance, and thermal insulation. In addition, the lightweight characteristic is also another advantage. EPP can be recycled and reused, and can naturally degrade without causing white pollution. Due to these excellent performance, the application of EPP has become increasingly widespread.
Application of EPP material:
Packaging fields: Packaging boxes for electronic communication equipment, LCD displays, plasma TVs, precision electronic components, and precision instruments and meters.
Automobile field: Car bumpers, car linings, safety car seats, toolboxes, trunk, armrests, floor mats, helmets, etc.
Foaming molding process: There are many types of foamed materials with diverse properties. The functions are differentiated based on their composition, density, and softness. However, as there are a large number of bubbles in foaming materials, they all have some common characteristics: 1. good impact resistance. 2. Good thermal insulation; 3. Lightweight.
The forming principle of EPP foam mold: The foam mold forming process is mainly divided into 5 steps: firstly is to preheat the mold before closing it; Step two, fill the material into the interior of the mold; Step three, inject steam into the mold and heat it to around 140 degrees Celsius; Step four, cool the mold to around 70 degrees Celsius; Step five, manually retrieve the product.
Technical difficulties of foam molds:
1.Parting line type: Due to the large size of the product, there is a possibility of errors in mold processing. To reduce errors, we did the rubber reduction treatment around the product, which is reducing the rubber by 1.5mm on the front mold side, creating a small difference between the front and rear molds. The sealing surface of the mold has changed from a sharp point to a flat sealing surface. However, this small modification could cause the parting line position to have a problem of burrs. Our rubber reduction has avoided this happening, so the products are very smooth and flat on the side without any misalignment or burrs.
2.Cooling: one key factor for size reassurance is the cooling of foaming mold. The efficiency of cooling is directly related to the thickness of products. If we cannot make uniform cooling, the inside of car seats may have dents and other problems. We have conducted an detail analysis regarding to product thickness in the early stage of production. As the product thickness of car seats is thick in the middle and thin at the edges, we have adjusted the mold cooling system according to the characteristics of the product. In addition, we have changed the order of opening the cooling water and adopted a cooling method from the middle to the edges to ensure that the thick rubber position in the middle of the product is cooled in the first time.
3.ventilation: several large areas of collision structures exit in the middle of the seat, which poses a significant challenge to the flow of airflow inside the mold. Thus, the ventilation of the mold is critical. If the gas is not discharged from the mold in a timely manner, problems like dents and internal defects will occur. We analyzed the characteristics of the product and adjusted the density of the air holes at the location where the mold has trapped air. For this set of seat molds, we designed about 1100 air holes to ensure smooth ventilation of the mold.
Although the overall strength of EPP seats is close to that of steel frame seats, there is still a possibility of severe deformation at the edges of the seats under compression. In order to increase the strength and strengthen the integrity of the seats, 13 5mm brackets were added around the interior of the seats. The bracket material is made of low-carbon steel with better toughness and ductility, and the bracket is subjected to electrophoretic treatment on the surface after welding to prevent rusting.
production difficulties:
1.bracket accuracy: As the core of the seat, bracket accuracy is the key. The bracket better integrated the edges of product and seats. We have conducted an assessment and made a specific fixture based on the mold size to compete welding and testing to ensure each part is qualified before entering into the next stage. After that, the bracket will be welded on top of the fixture. Electrophoresis treatment will be carried out after welding. Finally, the fixture will be used for the final verification to bracket, which not only makes sure the accuracy of bracket, but also can testify if the installment of bracket on mold can be completed efficiently.
2.Encapsulation molding, the metal brackets are wrapped inside the seats. However, the product size is relatively large, and the brackets are welded from multiple small brackets. Applying steam inside the mold during the production process will have an impact on the position of the brackets, which may push them out of the seat. Therefore, due to various factors, the fixation of the brackets has become a key focus. We tested the fixation of the brackets on site by opening molds and applying pressure. When the brackets are fixed in more than 10 positions, a relatively stable state is created. A modifications we made to the corresponding positions of the seats with a different fixing method. Firstly, we kept 2 fixing clips in each of the four directions of the brackets, and at the front-end position of the seat formed by splicing multiple small brackets. Fixed slots with fixed clips, so the stability is ensured by using embedded blocks in the suspended positions of the brackets that are crossed on both sides.
fabrication of bracket:
The bracket has been processed with fully automatic linear bending machine. Compared to human processing, the machine efficiency is higher, and the shape, angle as well as size are more accurate and stable. We made texting fixtures for bracket before production. After we have completed a product, an testing will be done and put the qualified product on the fixtures to make sure the shapes and angle of products, which improves our testing and production efficiency.
The qualified bending parts will be welded on the welding fixtures and there may be errors in the size of the bracket post welding, and thus an adjustment is required to make sure the electrophoresis will be carried out if there is no issue with the size.
inspection:
GREFEE always conduct the products inspection according to the QMs. We have inspectors on site for each procedure for each semi-finished product. Every QC staff ensure the flow of personnel in the upper and lower processes of the product. The image below is the 3D inspection report of the bracket and it can be seen that the key sizes of product are all within the accepted range before entering into the next stage.
After the car seats has been produced, we will confirm the surface and structure of car seats on site and then carry out the maximum size inspection to the products. An 3D examination will be done to the final product after the first two procedures. Through the below reports, it can be seen that the surface of car seats is smooth without defects, and all the size of critical areas meet the standards. Also, the function working properly and the bracket inside has no deviation.
packaging:
Grefee adheres to the principle of being responsible for our products and customers, and we strive for excellence in product packaging. We have used internal PE bags, 10T thick foam partitions, and 7-layer kraft paper packaging to ensure the safety and reliability of our products during transportation
About GREFEE:
GREFEE is a supplier with automotive parts production qualifications with more than a large engineer team over 300 people and a more than 100 people QC team, which has been certified by the ISO9001 and IATFI6949. All of our projects are designed and produced according to the APQP process. Grefee’s goal is to become a leading global automotive parts supplier. We collaborate with automotive companies from over 30 countries worldwide, such as Bosch, BYD, Volkswagen, General Motors, Aston Martin, Ferrari,etc.
why choose GREFEE?
Their working efficiency in the early stage of work impressed me. When I first approached them for an inquiry, they replied to us on the same day with detailed information. We compared the quotes of other suppliers and found that the price GREFEE asked was more reasonable. When I looked at the documents they sent to us, I found that they also provided detailed modification suggestions. The suggestions from their manufacturing engineers are professional, which saved us a lot of time in manufacturing and also enable us to better help our end customers.
Different from other suppliers that usually only quote according to my product requirements, Grefee also provided their ideas and quotes as per the quantity and requirements of the products. Their efficient quality management team basically provided various testing reports for inspection on the second day. Overall, you can trust them with their efficiency, professionalism, lower price, and quality. This is also the main reason why we have cooperated with Grefee multiple times on different projects.