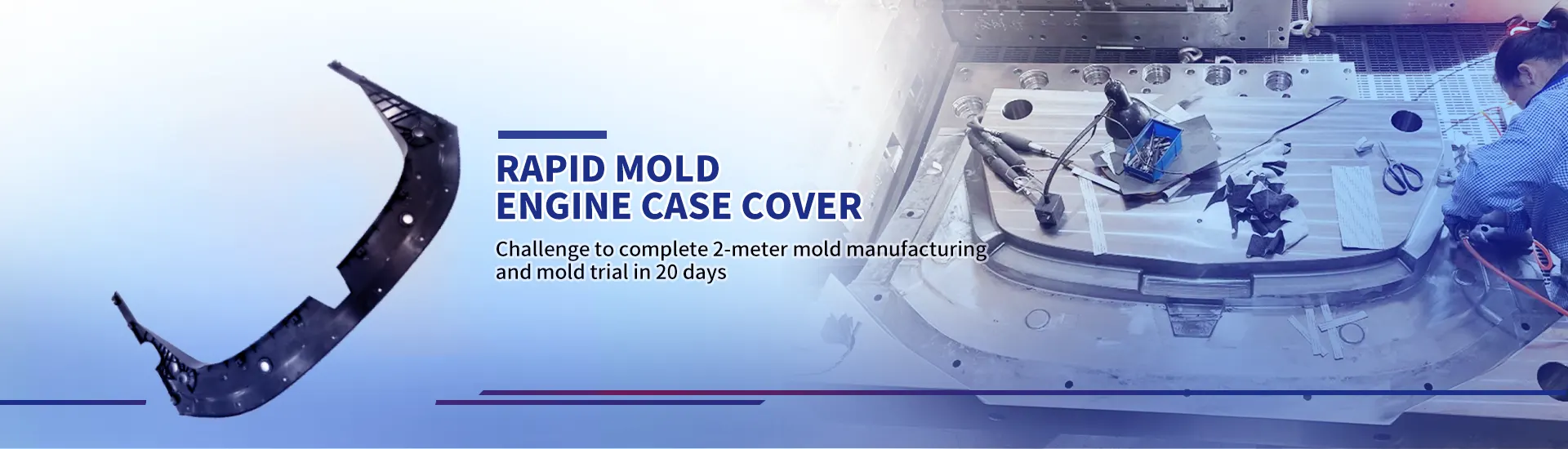
Rapid Mold – Engine Case Cover
Challenge to complete 2-meter mold manufacturing and mold trial in 20 days
Created by: Felix
Position: Project Director
Project Information:
This is the latest auto part of our old customer MOPAR, the engine case cover, 100 pieces, with a delivery time of 20 days. The customer needs to provide two quotations for the prototype and the mold for evaluation. We understand that the customer’s demand for 100 pieces of this product is mainly for testing, to provide data support for subsequent mold manufacturing and mass production.

Project evaluation:
We evaluated the prototype manufacturing of the parts and believed that the difference between the prototype material and the actual injection molding may lead to large errors in the test results of multiple tests. We suggested that instead of choosing the prototype process that would result in errors, it would be better to directly choose the rapid mold. After communication, the customer agreed with our plan. Therefore, we followed the rapid mold plan. Although the mold was manufactured in a rapid manner, the product quality was completely in accordance with the formal mold, and the delivery time remained unchanged and was completed in 20 days.
Specific requirements:
1):The product cannot have any defects such as lack of glue, shrinkage, beryllium front, etc.
2):There must be no joint lines, scratches,and other issues on the surface.
3):Strictly control the mold manufacturing cycle, the time is 20 days, and the sample quantity is 100 pieces.
Product information:
Part Name:Cover Plate
Project Name:M1036
Part Number:68586208AA
Part Size:1612.5X852.38X180.05mm
Mold Size:1800.0X980.0X920.0mm
Part Weight:1696g
Mold Weight:13T
Cavity/Core Material:P20(1.2311)
Cavity Number:1X1
Gate Type:9 Drops Hot Nozzles,Valve gate
Design Cycle:3 days
Manufacture Cycle:20 days
Molding Cycle:100 S
Production Machine:2800T(HAI TIAN)
Manufacture Date:Dec 2023
Rapid mold features:
There are differences between rapid molds and ordinary molds in design, manufacturing and use, which are mainly reflected in design time, manufacturing cycle and cost, mold life, precision, quality and durability.
Design time: By simplifying the mold design, the design cycle of the rapid mold is generally controlled within 3 working days.
Life and durability: Rapid molds are suitable for small-batch production, and their lifespan is normall low.
Material selection: Rapid molds are usually produced in small batches or meet verification requirements, and most materials used are soft materials.
Processing accuracy: Due to the design time and manufacturing cycle, the accuracy of the rapid mold is lower than that of the formal mold.
The actual production materials is supportive for the subsequent manufacturing and production of formal molds, such as whether the injection molding material needs to be changed, whether the mold structure can be realized, etc.
Technical difficulties:
High product requirements, large mold size, short manufacturing cycle, many edge insertion positions, 10 deep undercuts, and the screw temperature needs to be set according to customer requirements. These are all challenges for this set of molds. In order to ensure that the mold manufacturing and trial molds are completed within the delivery period, we optimize the entire design and manufacturing process.
Surface requirements: weld line issues
No joint lines on the surface of the product allowed, which is verified through mold flow analysis and control the glue injection sequence to avoid water lines on the surface of the product.
Mold flow analysis
Increasing the glue inlet to avoid pressure loss in the flow channel as could as possible. The 9-point needle valve is used for glue injection in sequence, and the glue injection method is banana-type. The glue inlet is duckbill-shaped. The glue inlet size is first processed according to 3X1 and then adjusted. The injection molding equipment is Haitian 2800T machine. The maximum glue injection pressure is 80Mpa. Adjust the glue inlet position and move the joint line to the hole to avoid it appearing on the front of the product. The core hole is made into an insert to avoid deformation affecting assembly.
To achieve the fast delivery of molds and reassure customers, we optimize the mold structure based on the product structure and equipment advantages. Not only the delivery time is ensured but also the mold and product quality also meet the requirements. We will mainly optimize the mold structure from the following aspects.
1.Design
The size of the product is roughtly 1700mm, and the mold size is 2 meters. Large mold steel is required, and the ordering cycle is generally about 5 days, which does not meet our goals. In addition, the size of the steel is difficult to process and transport. Thus, optimize the design and processing is necessary.
Improvement plan: After discussion, also considered about the progress of our CNC equipment processing, we divided the rear mold core into 5 parts, and the size of all mold cores was controlled within the range of conventional CNC processing. At the same time, 5 matching CNC machines were reserved for full cooperation to shorten the CNC and EDM processing cycle. In terms of detail design, non-critical positions adopt air avoidance design to reduce the workload of mold matching. In terms of processing, we adopted a fully customized mold base solution. After the optimized design, the full processing time of the mold base was reduced from 15 days to 12 days.
2.Structure
The product has 10 large-angle undercuts. If use traditional inclined ejector, extra workload will be added to the rear mold core and mold base, especially for such large mold cores. The maximum size of the mold core after processing is 700 long, which is difficult to position in the mold. The weight exceeds 800KG. The inclined ejector hole will lead to errors in the wire cutting position due to weight reasons during wire cutting, which will also lead to extra work when matching the mold.
Improvement plan: as the number of products is only 100, after the meeting, we decided to use the manual insert form, cancel the inclined ejector structure, and decide to use an ejector at the bottom of the manual insert. The advantage of this is that it is convenient for processing, as the ejector is at the bottom of the manual insert and the ejector does not directly contact the glue position. Therefore, the accuracy of the ejector hole will be lower than that of the inclined ejector hole. Therefore, the ejector hole on the mold core can be directly processed by a drilling machine, and the ejector hole on the mold base is also the same. Compared with wire cutting, the time cost is low and the processing progress can be better guaranteed.
3.Processing
All positions that can be processed are processed by CNC, reducing EDM processes, saving processing time, and reducing mold saving time. The first processing is on the back of the steel material, with a step height of 20mm. The steel material is positioned and divided into the four sides of the bottom step. The pinholes, screw holes, etc. are drilled and processed. Then, the B plate of the mold is tested to determine whether the 5 pieces of rear mold steel materials can be assembled as a whole to ensure accuracy; the front of the mold core is turned over and processed. 5 CNCs are processed simultaneously to ensure progress and control the CNC and EDM time of the mold core within 10 days.
Select the appropriate EDM process according to the depth of the bone position. For areas with dense bone positions and bone depth exceeding 10mm, stone grinding copper is used to save EDM processing time. There are many steps on the top surface of manual inserts and the top surface of glue-in inserts. In order to avoid steps on the top surface of the inserts, the top surface of the inserts is processed after the mold is matched to reduce processing errors.
Mold assembly:
Although the rear mold core is designed with multiple mold cores, the weight after processing is about 170KG. Hence, we must be careful in assemblying, otherwise the edge of the mold core will be broken. We adjusted the assembly order of the mold cores, first installing the middle and two side mold cores (1, 3, and 5 mold cores), and then arranging the two corner mold cores (2 and 4 mold cores) to a fixed position by pushing them horizontally.
The 9 needle valve nozzles is segmented design, which effectively improves the processing time and ensures the installation accuracy. Due to thermal expansion and contraction, the thermal expansion coefficient of the hot nozzle will affect the position and size of the hot nozzle. The segmented design can ensure that the data changes caused by thermal expansion are reduced; when installing the hot nozzle, first install the second section of the hot nozzle in place, and then fix the two sections of the hot nozzle with the middle bridge.