Acceptance check of die casting mold

Posted on : Oct 27 , 2022 By GREFEE
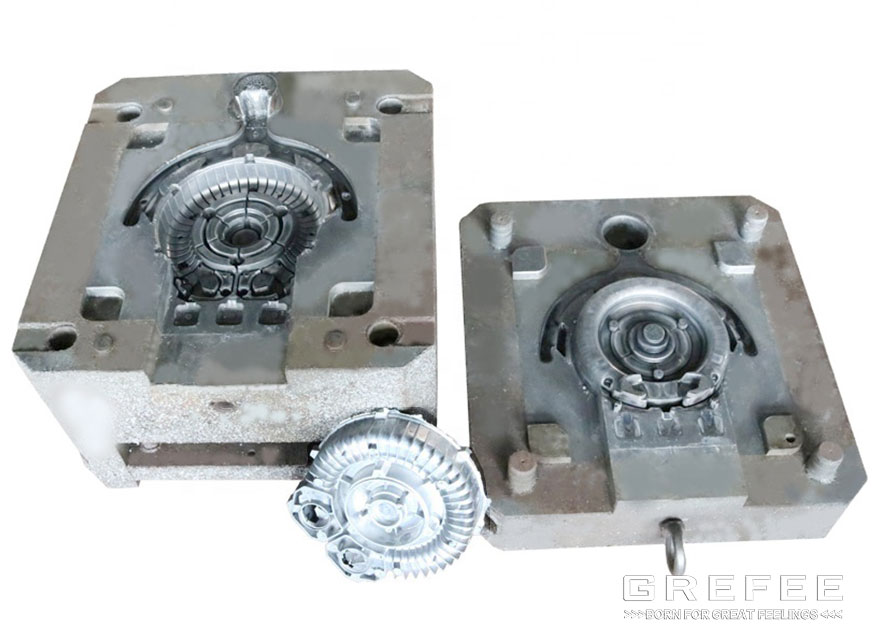
The die casting mold manufacturers around the word have gradually move their business in customs aluminum die casting mold to China. Ensuring the products meet the quality requirements is the key. The following introduces the acceptance check of die casting mold.
Accept and check of mold
1. Safety check of mold
Safety production is the base of for an enterprise. Safety is one of the important characteristics of mold because poor safety will bring potential risks to the subsequent production, or even cause personnel causalities.
(1). Acceptance check of the lifting holes
The lifting holes of mold must meet the policies of the technical agreement signed by both parties to make sure the balance of the lifting of molds (The lifting balance includes two aspects: the overall lifting of the mold and the split lifting of the movable and fixed mold). This requires full consideration when making the location of the lifting hole.
For mold parts weighs over 15kg, the lifting holes are necessary. The position of the lifting holes should provide continence for the maintenance of molds.
The accuracy ache of mold lifting holes is more importance than the quantities and positions, and it must be checked. These lifting holes should meet the requirements of H7, and the depth should not less than that of the thread of lifting ring of the same specification. The reason why the accuracy of lifting holes is important because it is often found that the thread bottom hole of the lifting hole is too large during the acceptance of the mold, and the thread matching with the lifting ring is not good, which may even lead to thread slippage during the mold lifting process, and cause accidents, like personal injury and mold equipment damage.
(2). Acceptance check of mold slide spring
Each slide requires the limit spring assembly to make sure the position of slide is reliable after mold opening and prevent the slide from moving itself and collapse with the guide pins. During mold clamping, the spring is compressed due to the action of slide. If there is error during the assembly progress, the length of spring after being compressed completely outweighs the remaining effective length of internal screw of spring. Another thing happens is that the screw will slide off from both ends, so that the spring will collide and cause personal injury.
(3). Waterproof acceptance of travel switch under mold
During the production, due to the effect of mold release agent, the stroke switch of core pulling oil cylinder under the mold must be waterproofed to prevent the switch from being affected by the water mist of release agent, for it results in the abnormal core pulling movement, which further leads to the collide between molds.
(4). First reset hole thread accuracy inspection
The first reset hole thread should ensure the accuracy of threads because the thread accuracy errors will cause the first reset bar cannot work normally, which will make the ejector plate cannot be reset properly. Part of the ejector rod interferes with the slide and cause mold damages when clamping the mold.
2 .Acceptance check of each part of mold and external connection size
The connection size of mold and external areas has four parts:
(1). Interface dimension of sprue sleeve
(2). Oil cylinder connection size of the core pulling oil cylinder
(3). If the mold is reset first, reset the rod hole size
(4). Connection size of the water cooling pipes
Only until the size of this part is qualified, it will make sure the molds fit for the die casting machines of the company. In another word, only qualified molds can be tested on the die casting machines of the company. What is worth of noticing, some designs of die cast molds require to be used on different types of die casting machines, while there may be a slight difference between the connection size. In terms of this, a ring is needed on the mold gate sleeve. The size of ring should also be tested.
3 .Appearance acceptance of signboards and molds
Things should be specified on the signboards of molds include: Part drawing number, mold name, delivery date, supplier name, mold weight, mold outline dimension and other mold related parameters are convenient for mold management in the future.
Things should notice on appearance acceptance: The transition part of the runner shall be smoothly connected, the splicing part shall be smooth and flat, and the surface roughness Ra of the runner and the mold core shall be ≤ 0.8 μ m。Knife marks left by machining and discharge marks left by electrical machining are not allowed. The contact area between the ejector plate limit block on the mold foot and the ejector plate shall not be too small, such as The contact area between the limit block and the ejection plate of the mold is too small. During the use of the mold, the ejection limit is unreliable, and the traces of the ejector rod on the die casting parts are different in depth, resulting in the unqualified batch of products.
Generally, after the appearance check of molds, a “die casting mold test list” is required to test the working status of molds, which is the most direct and reliable test methods. Main content of the mold testing list:
(1). The movement of the movable part of the mold during the mold test shall be flexible, stable, accurate and reliable, and whether there is skew and stagnation.
(2). The cooling circuits and hydraulic circuit should be smooth, without leaking
(3). Good venting condition. If there is any flashing of liquid metal.
(4). If the mold required fixed parts are stable installed
(5). The sliding block shall move steadily, the sliding block and wedge block shall be compressed after mold closing, the contact area shall not be less than three quarters, and the limit position after mold opening shall be accurate and reliable;
(6). No abnormal sound of ejector bar of mold. The ejection and reset are normal.
(7). There is no abnormality in punch following and product ejection.
(8). The mold opening shall be free of cracks, deformation, product parts falling off the fixed mold and other phenomena.
(9). Test results in early stage for parts after mold pre-heating
Quality inspection of parts
The inspection of parts should be carried out before the mold opening according to the technical requirements on the contract. The major things need to be checked are plane blank drawing of product parts, product sample, three-dimensional drawing, special requirements agreed in advance, etc. The mold preheating parts should be excluded in the product parts used for inspection. Parts produced under the stale die casting conditions can be used for testing. Major testing requirements include:
1. Appearance of parts
Designing and manufacturing good quality die casting molds, the number of the mold preheating parts will be largely reduced, and the appearance of the parts is very beautiful. Defects on the die casting parts are simple principles to test the properties of mold forming properties. According to the related technical standards, the appearance of the general parts should be:
No cracks, bubbles, strains, loose, cold shut, flow lines, deformation, shrinkage, under casting and other defects. The above defects can be adjusted by processing. Some defects that cannot be eliminated requires to adjust the technique and carry out mold modification. Otherwise, the mold should be classified as unqualified, especially for the parts that are produced under abnormal conditions. Although the parts are qualified, the molds are not qualified necessarily. What should be paid attention to is that during the mold acceptance, deranging working conditions will harm the equipments and molds, sometimes even have safety accidents.
2 .First testing of full-scale inspection of products
Make a full-scale inspection on the die castings produced by the new mold for the first time can effectively avoid the hidden perils in the size of die casting produced products, especially for the size of the fitting part with other parts. For instance, two pieces of die casting parts required to be assembled. Single inspection should be within the qualified tolerance. If one of them close to the small tolerance, and the other part is close to the maximum tolerance, which easily leads to the problem that it cannot be assembled.
3. Performance testing of die casting parts
As the application ranges of die casting parts increases, the requirements for all properties of die casting parts increase, too. Common tests include destructive test, air tightness test and air hole (shrinkage hole) inspection after machining, etc. This is very important for different alloy custom die casting mold, like custom aluminum die casting mold or custom zinc die casting mold, etc. It is necessary to carry out the tests for the newly made parts. When the die casting parts cannot satisfy the requirements of these needs, then we need to analyze them to find out the reasons to solve them. Sometimes, even some little changes of gates of mold will change the filling status of the mold, and the mold filling status will impact the structures, density, venting, and other problems, which will affect the quality of die casting parts.
Check of the stability of mold and
1 .Acceptance check of the mold stability
Due to the poor working conditions of the molds, there is a higher requirement for the stability of mold. The defects of the design and manufacturing of mold cannot be detected through a constant production. Thus, a quality stability test will be required for a die casting mold. The production volume usually is: aluminum, magnesium alloys 1500 cav, zinc alloy 3000 cav.
Once the quality stability issues has been solved, the die casting mold is considered as qualified. Common issues of stability are:
(1). Small core of mold cracks
(2). The slide is soaked and stuck
(3). Running water on parting surface
(4). Ejection deformation caused by insufficient die strength
(5). The die-casting parts are cracked and damaged during mold opening
(6). The die casting part falls off during mold opening
(7). Local mold sticking (mostly at the gate scouring part
(8). Unstable dimension of mold parts, the form and position tolerance exceeds the standard
2.Acceptance check of mold accessories
Once the quality of die casting parts meet the requirements, starting the detailed acceptance of the mold accessories attached to the mold factory and the cores installed on the mold according to the mold accessories drawings to ensure that the drawings are consistent with the original copy, which is very important for the future mold maintenance and production. For copying molds, the mold factory is required to design and make molds according to the original mold accessories in the first place, and try to standardize the extra parts to allow the original mold accessories be continually used. In this way, the inventory and waste of mold parts can be reduced significantly. For serial product parts, the manufacturers need to design and manufacture according to standard spare parts when making molds. Standardizing the mold accessories reduces the maintenance cost.
MORE BOLG
Insert mold in injection mold service
What are advantages and disadvantages of Zinc alloy and Aluminum alloy?
Inspection standards for injection molded partappearance
How to judge the quality of your plastic products?
Inspection standards for CNC machining
To ensure that your products are 100% qualified
Categories
Try GREFEE now,for free
We keep your uploaded files confidential and secure.