Analysis of cracking phenomenon of plastic screw bar and preventive measures
Posted on : Dec 20 , 2022 By GREFEE
Cracking phenomenon of plastic screw column is a common plastic structure failure phenomenon. It is tricky to fix it as once the cracking occurred, it is hard to make up. What is the most tricky issue is the cracking is not to detected as easy as other defects of plastic parts as soon as the injection molding is completed. In many cases, cracking has not occurred yet (or already cracked but just micro, which is difficult to visualize). When the cracking occurs, the parts have already transferred to the production line or are already assembled and ready to deliver. Thus, this kind of cracking normally is hard to noticed and the consequences can be devastating.
Screw bars is a fastening structure of plastic products. The cracking of screw bars will lead to lower or invalid fastening function, which presented as products cannot pass the dropping test, or the internal functional parts fall off can caused damages, etc. This is not same as general appearance issues (eg. shrinkage, flashes, scratches, etc). Appearance problems normally do not affect the functions of products. However, the cracking of screw bars will affect the functions of products ultimately.
Cracking usually occur into brittle materials, stress sensitive materials or materials prone to internal stress, commonly include PS、ABS、PC、PC/ABS alloy, especially PC. It is like the NBA basketball player Durant . Durant is a great basketball player with excellent basketball skills, but he is too sensitive to the opinions from public (stress sensitivity, organic solvent sensitivity), easily be hunted mentally that could explain some inappropriate responses time to time on social media (stress release, cracking). This makes him lovely but also hateful as it does not have the own system and outstandingly capable, which can be seamlessly compatible with most teams, like Thunder, Warriors, Nets, so you will find that PC can be blended with a variety of materials to form alloys: PC+ABS, PC+PS, PC+PBT, PC+PET, etc.
PC plastic screw bar cracking include two cases:
1. The light hole screw bar cracked after self tapping screws were applied.
The essential cause for cracking is the unbalanced distribution of internal stress (mainly are cracking resistance and internal stress. This unbalanced distribution include unbalance in size and direction (stress concentration). When the cracking resistance and internal stress are balanced, cracking will not occur. While when the cracking resistance is lower than the internal stress, it will cause cracking.
Cracking resistance mainly depends on how long the molecular chain is and the number of entanglements between chains, the force between molecular chains, etc.
Internal stress mainly refers to the stress produced due to the orientation of large molecular, cooling shrinkage and other factors during the plastic melting process, which mainly include orientation internal stress and shrinkage internal stress.
Orientation internal stress
Orientation mechanism: Polymer under external force, of which the molecular chain is arranged orderly along the force field direction.
Orienting requires external force to achieve, and orientation is a natural process. Thus, the orientation state is a non-equilibrium state. Once the external force is removed, the chain or large molecular chain will spontaneous reorientation and return to the original state. Just like a stretched spring. When the force applied onto the spring has been removed, the spring will return to the original state. Therefore, if you want to obtain the orientational material, the temperature must be under the glass transition temperature after the orientation and frozen the chain or large molecular chain. Of course, the frozen status belongs to the thermodynamic nonequilibrium. Only with relative stability, the temperature and time will impact the stability of the orientational structure.
Orientation characteristics: anisotropy
Before orientation, the large molecular and chain segment is are arranged randomly, and thus it presents isotropy.
After orientation, the force between atoms mainly relies on chemical bond. while for the direction vertically, the force mainly relies on the VDW, so it presents anisotropy, which is demonstrated on the significant difference of mechanical, optical and thermal properties of materials before and after the orientation. For instance, the tensile strength and impact strength can be improved in the orientation direction, but the tensile strength and impact strength decrease in the vertical direction, so the molecular orientation is directional.
Downsides and upsides of orientation: the directivity of the orientation has upsides and downsides in different molding processes or products.
The molecular orientation is easy to control when the plastic process is in the high elastic status, and easy to lose control when it is in viscous flow state. Squeezing formation is processed when the plastic in the high elastic status. The stretching ratio, traction and speed are all controllable. The strength o风stretching direction of products has been improved greatly, like the plastic wire, film, tube, sheet, plate and other products. The injection molding is processed under the viscous flow state. The orientation of molecular is disordered, force is inequality in size, and the freezing speed varies, too. These issues cause different internal stress inequality in size, and are more likely leading to warpage and cracking. Thus, freezing molecular orientation should not be involved into the injection molding processing.
Orientation internal stress: the high pressure and high shearling force results in serve change into the molecule chain of plastic molecular. The molecular is frozen before it returning into disorder and relaxation state, which could explain the residual internal stress.
Molecular formula of PC
It is quite obvious in some large molecular chains with polymers containing the benzene ring, like PC, PPO, PPS, etc. The molecular chain of this type of polymers is high and the viscosity of melt is high, but the polymer molecular chain activity is poor. Thus, poor recovery of occurred reversible high elastic deformation, which is disorientation difficulty. Normal plastic materials will spontaneously complete the disorientation after injection molding, and the orientation stress is low. However, it is difficult to achieve disorientation after the formation. At this stage, the orientation stress will exist. When the cracking resistant force and the internal stress are balanced, the products will not crack. Also, this balance will be broke when the cracking resistant force decreased or the combined force of internal stress+ external stress is larger than the cracking resistant force with the changing of environmental factors (temperature &external force) and cracking will occur, which is one of the reasons for the cracking of the final PC products being placed after a period of time.
This can explain why the PC material smooth hole screw bar cracks after tapping screws.
Based on above, the main reasons for cracking are the cracking resistant force and internal stress are broke. Since the internal stress cannot increase automatically after formation, we can assume that the cracking resistant force decreased or external force is involved (extrusion stress of tapping screw), this cracking phenomenon is called environmental stress cracking.
The environmental stress cracking occurs when there is special medium used in plastic products (corrosive medium, solvent and certain gas). These special mediums and stress will cause crack or even fractures. We can conclude that two important conditions for the environmental stress cracking are special mediums and stress.
The special mediums that caused the environmental stress cracking of plastic products include organic solvents, water, some surfactants, ozone, etc. The mediums will not lead to the chemical reaction directly or the degradation of molecular. As a matter of fact, the mediums penetrate into the molecular chains and damage the internal molecular force of polymer chain, which further accelerating the molecular fracture and finally reduce the anti cracking ability. Thus, not only we should do to avoid applying the organic solvents such as antirust oil and thread tightening agent on the screws, but also to prevent the products from contacting other mediums that may cause cracking.
There are two types of stress causing the environmental stress cracking, which are mechanical stress and internal stress. The former one refers to the products are always under the mechanical force, like the extrusion stress of screw on screw hole. Thus, to reduce the mechanical stress, the matching structure at the screw hole shall be reasonably designed.
Key parts:
1. The inner diameter of screw bar should be larger than the normal size if it is hard plastic.
2. If the outer diameter of screw bars cannot become larger, straight or cross reinforcement is required.
3. The depth of the inner holes of screw bars should be deeper than that of the screws for enough space to contain the plastic chips.
4. The orientation structure of screws. To prevent the screws from being hit obliquely, the limit structure must be made on the pillar, and the top of the inner hole of the screw column shall be guided by an angle.
5. The torque of the screwdriver should be matched according to the size of the screw during the assembly process to prevent the cracking from happening due to large torque.
6. Select appropriate self-tapping screws can reduce the concentration of stress.
Shrinkage internal stress
Shrinkage internal stress, is also called the thermal stress, which is a type of internal stress produced caused by the uneven contraction of plastic products due to the cooling formation during the melting processing.
1.Due to the plastic structure problem, even if there is a cooling system, it is difficult to achieve the same cooling rate for all parts of the product, so it is difficult to avoid the internal stress of cooling shrinkage. Especially for thick wall plastic products, after opening the front mold, the outer layer of the plastic products will first be cooled, solidified and shrunk, and its inner layer wrapped in the rear mold core may still be hot melt, so that the core layer will limit the shrinkage of the surface layer, causing the core layer to be in a state of compressive stress, The surface layer is in a state of tensile stress. When the product is ejected, it will extrude and deform inwards.
2. If it is also the structure at the same side of the rear mold, such as screw column. Due to the small difference on cooling rates inside and outside of the screw bars, extrusion deformation will not occur at inner holes after the formation.
3. If inserted the un-preheated copper bolts and metal inserts into the molds for injection molding, the cooling rates of inner holes in screw bars and external walls are different. After the injection molding, the inner holes of screw bars will contract and tightly hold the bolts. Due to a big difference of the thermal inflation between the plastic and copper bolts and other metal inserts, the contraction rates inside the plastic parts can be seen as zero compared to the contraction of plastic. Now, the copper bolts will affect the overall contraction of screw bars and the contract stress produced due to this will be huge. A high level of the contraction stress is around the copper bolts. If this kind of contraction stress is larger than the cracking resistant force of plastic, then it will cause micro cracks on the plastic surface. These micro cracks do not risk normal plastic products. However, for PC plastic products that are sensitive to the loopholes, this will grow into fractures gradually.
This is why no cracks found from the molds at the time when the copper bolts are inserted into molds, but after a period of time (of course, the above is just one of the multiple reasons. There are still other reasons)
To address this, we can start from reducing the contraction stress or increasing the cracking resistance force.
1. Before inserting, preheat the copper bolts, making the cooling rates of both internal and external walls of screw bolts equal to reduce the contraction stress.
2. Carrying out surface degreasing treatment for the copper bolts that can prevent the stress cracking of products due to the grease.
3. There should not be too many copper bolts in one product, or the plastic is likely to degrade during the stay inside the barrel, which reduces the cracking resistant force.
4. It’d be better to select bolts, of which patterns or shapes of copper bolts with sleek features to reduce the concentration of stress.
5. Enlarging the outer diameter of screw bars appropriately. If cannot achieve, considering to improve the strength of screw bars with straight or crossed reinforcement to reduce the concentration. If these methods cannot solve the issue, the following embedding schemes, such as hot pressing or ultrasonic can be considered: the type and embedding method of metal thread inserts in plastic parts.
To reduce the subsequent cracking of the screw column, the following aspects can be considered
1. Selection of plastic raw materials
a) Resins with large molecular weight and narrow molecular weight distribution
The larger the molecular weight of polymer is, the greater the force between macromolecular chains and the degree of entanglement are, and the stronger the resistance to stress cracking of its products is. The wider the molecular weight distribution of polymer is, the larger the low molecular weight component is, which is easy to form micro tearing first, causing stress concentration and cracking of products.
b) Reduce the additive content of nozzle material or recycled material
For water absorbing resin and resin mixed with amount of recycled materials, even a small residual stress will cause the embrittlement as the water absorbing resin will decompose and embrittle after heating. While, resin with higher recycled material content has more impurities, higher volatile matter content, lower material strength, and is prone to stress cracking
c) Blending modification
Resin that is prone to the stress cracking blended with appropriate resins can reduce the level of internal stress. For example, blending the proper amount of ABS, PBT, PET, and others with PC can effectively help to improve the stress cracking resistance of PC.
d) Enhanced modification
The internal stress of the product can be reduced by using the reinforced fiber for reinforcement modification as the fiber entangles many macromolecular chains, which furthre improving the stress cracking ability. For instance, the stress cracking resistance of 30% GFPC is 6 times higher than that of pure PC. However, what should be paid attention to is that the filler should not be too much, otherwise the resin material is likely to be brittle.
e) Other additives
Adding appropriate antioxidants to plastics can alleviate or prevent the oxidative degradation of resin materials during processing or use, and improve their mechanical properties and aging resistance.
2. Reduce the orientation internal stress of products
The molecular orientation increases with the increase of molecular chain length. It changes as the change of pressure, freezing temperature and time. The selective molding process can be adjusted and controlled to reduce the molecular orientation of injection molded products.
a) Increasing the temperature of melt and mold to reduce the orientation effect.
b) Lower the injection pressure, holding pressure and time to reduce the molecular orientation.
c) Gates reduced in size can reduce the molecular orientation of the product .
d) The product wall is thin and the mold temperature is extremely low, so the product is cooled before orientation, and the orientation effect is reduced.
e) Under the action of high shear force, the melt temperature increases, the viscosity decreases, the mold cavity is rapidly filled and cooled, resulting in orientation force reduced.
3. Reduce the shrinkage internal stress of products
The optimization is mainly considered from the mold cooling water path to reduce the internal stress caused by uneven cooling. Preheating the embedded metal inserts as necessary.
4. Structure design of products
What need to be careful with in terms of the structure design of screw bars have already been mentioned, so we will move on to next.
5. Reduce or avoid products contacting with media causing environmental stress cracking
After the formation of products, we should prevent the products from contacting with some organic solvents, gas and other substances that could cause environmental stress cracking during packaging, transportation, assembly, usage processes.
6. Carry out annealing treatment for products
The thermal treatment for plastic products is to place the molded products under a certain temperature for a period of time to eliminate the internal stress.
Generally, soaking the products into the hot oil, hot water or hot wind. According to the variety of plastics, adjusting the annealing temperature for a period of time, the annealing is done. The annealing temperature is normally 10-20℃ lower than the thermal deformation temperature or approximately the glass melting temperature. If the annealing temperature is too high, the products are likely to deform. If the temperature is too low, the annealing effect cannot be achieved.
What should be aware of is that the products after annealing should be cooled naturally rather than rapidly. In addition, the annealing heat treatment had better be processed immediately after formation. This effect is the best.
Here has another question. How to know whether the screw bars will crack or not?
Stress cracking inspection is required at the early stage, like PC material. Under the room temperature, soaking the PC products for driving screws or embedding copper nuts into the glacial acetic acid or carbon tetrachloride solution to estimate the stress level according to the time required for the screw bars cracking. The longer the time is, the lower the stress is. If the product cracked in 5-15s, it indicates the stress is huge. If there is no cracking occur after being soaked for 1-2 mins, it indicates the internal stress is low.
Finally, if the screw column cracks, some products can be remedied by gluing. See Fig below:
MORE BOLG
Insert mold in injection mold service
What are advantages and disadvantages of Zinc alloy and Aluminum alloy?
Inspection standards for injection molded partappearance
How to judge the quality of your plastic products?
Inspection standards for CNC machining
To ensure that your products are 100% qualified
Categories
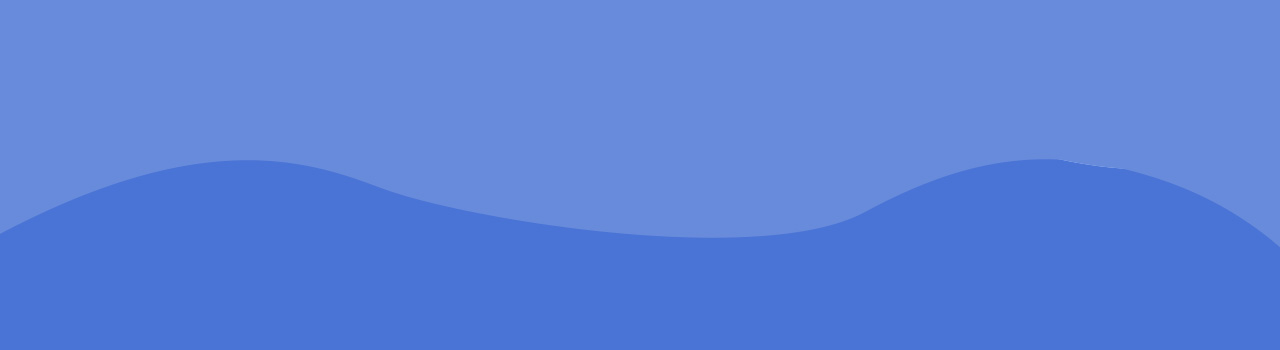
Try GREFEE now,for free
We keep your uploaded files confidential and secure.