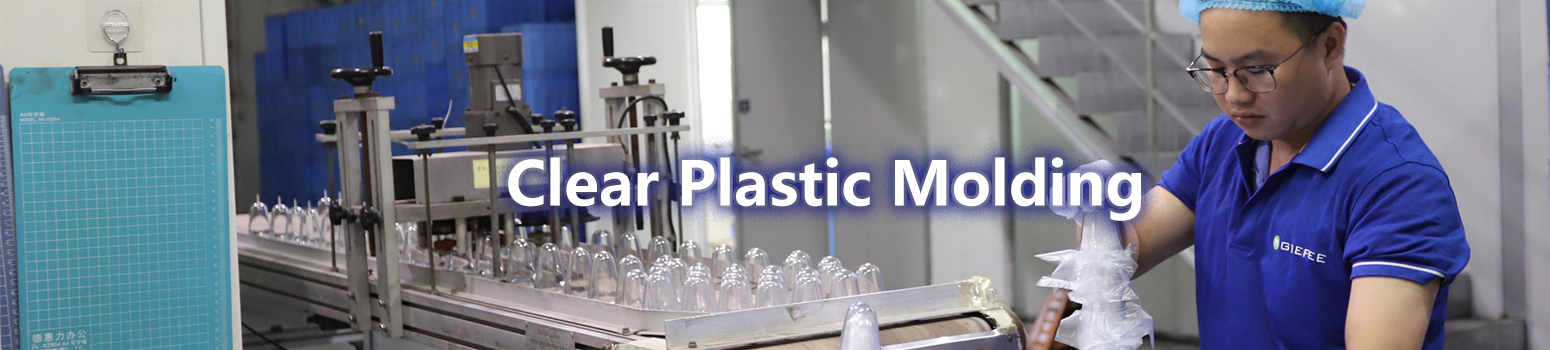
Molding Clear Plastic at GREFEE
Clear injection molding products are beautiful and novel, and are widely used in daily life, such as automotive lighting, Medical container,lens, packing boxes….etc. Injecting transparent parts are much harder to make than ordinary ones in injection molding process.
GREFEE provides high-quality and most economical customized transparent plastic services. The production of transparent injection molds is as important as the injection of transparent plastic parts. High-quality injection molds are the basis for making high-quality transparent injection molded parts!
Use the right injection molding material for your Clear Plastic Molding.
GREFEE provides a series of transparent plastics, such as PC, PMMA, PVC, PS, GPPS…etc. for your injection molded parts. Material is quietly likely to damage the function and performance of the end product. For example, the automatic lighting matches with PC/PMMA according to the standard due to their high performances in finishing and light transmittance.
If you change the material to transparent PP, the performance will be completely different. Before processing, fully consider the material and transparent plastic injection molding technology. Transparent mold manufacturing technology is very important! You can get the certified transparent plastic you most look forward to at GREFEE, and immediately contact our engineering team at info@grefeemold.com. to choose the right injection molding material for your project and evaluate your project free of charge.
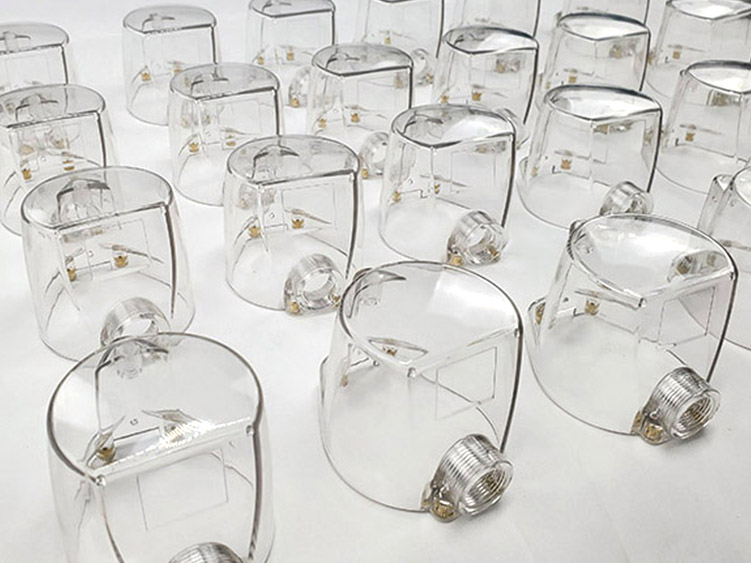
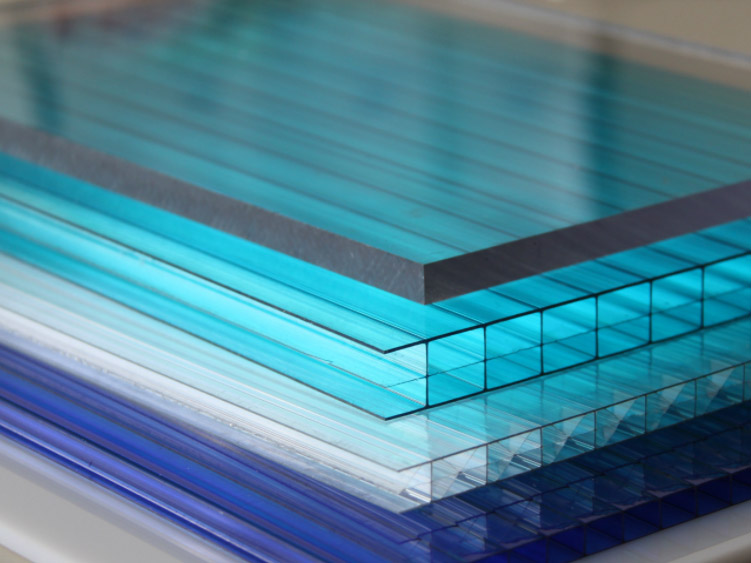
PC material property:
High transparency(close to PMMA), amorphous, fine heat resistance, low molding shrinkage(0.5-0.7%), high dimensional stability, high precision, most high impacting strength, micro-creep, firm and tough, low fatigue resistance, low wear-resisting, sensitive to gaps, weak stress cracking
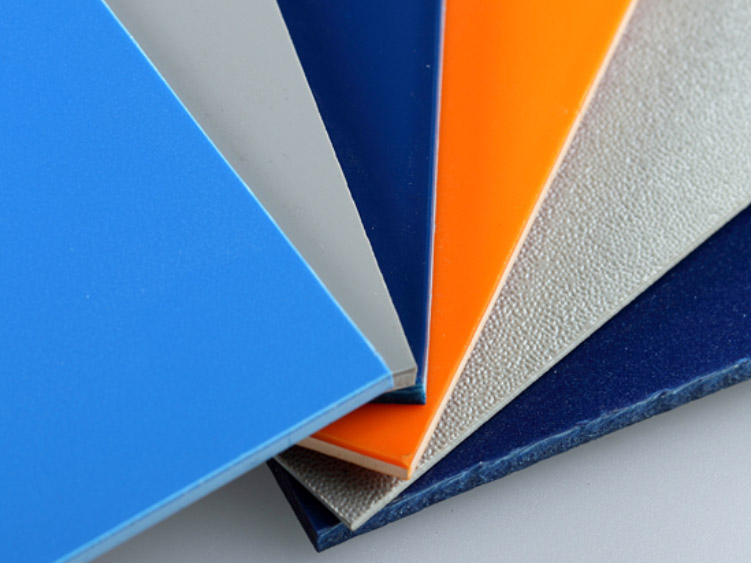
PMMA material property:
Most excellent transparency(only GPPS can compare), fine light-transmitting, high mechanical strength at room temperature, low surface hardness, easy to scratch need high-quality packing.

PVC material property:
Generally hard PVC contains plasticizer under 15%, while soft PVC contains plasticizer above 15%. Toys making usually adopts soft PVC with hardness 35-90°, amorphous plastic, transparent, tinting-easy, material hardness and mechanical property are determined by the content of plasticizer(usually 55-90°).
GPPS material property:
High transparency, fine gloss, tinting-easy, amorphous plastic; dimensional stability(shrinkage around 0.4%), inferior wear-resisting, therefore parts need high quality packing to avoid scratch; sensitive to internal force, crisp, no ductility, low impact strength, easy to crack and get sharps and edges.
Mould materials for clear plastic molding are: NAK80,1.2344ESR,S136,S-STAR
Use the right steel for clear plastic part mould building.
NAK80, P20HH, 1.2344ESR, S136, S136H, and S-STAR are the most common steels used by GREFEE for cavities and cores. For small batches of transparent plastic molded parts, such as transparent plastic molded parts, transparent plastic molded covers, we usually recommend customers to use NAK 80, S-STAR, P20HH or S136H as mold inserts, even without heat treatment, they have 300,000+ mold life. For large For volume requirements, the advantages of heat-treated S136, 1.2344ESR surpass NAK 80, S-STAR, P20HH or S136H, and are more durable.
NAK80 is hardened steel, high solidity, excellent dimensional stability, excellent discharge processablility and etching, mirror polish can meet #8000; suits for medium-volume injection molding production for simple structure and high performance and precision products, such as car fascia board, copying machine, printer, and products made from plastic with corrosive or cannot add fire-retardant, such as POM, PVC..etc.
S-STAR(DAIDO): High purity, tiny and even construction, excellent mirror polish and corrosion property, fine dimensional stability of heat treatment, hardness can meet HRC50-52 by appropriate heat treatment technology, polish, corrosion resistance and wear resistance can be improved. Suits for low/medium volume high mirror injection molding production of PC, PMMA…etc, and for injecting corrosive plastics like PVC, PA, POM…or plastics with fire retardants, and also for mechanical components used in food industry requiring corrosion resistant.
S136(ASSAB):High purity, tiny and even construction, excellent mirror polish and corrosion property, fine dimensional stability of heat treatment, hardness can meet HRC50-52 by appropriate heat treatment technology, polish, corrosion resistance and wear resistance can be improved. Suit for long-term high mirror injection molding production of PC, PMMA…etc, and for injecting corrosive plastics like PVC, PA, POM…or plastics with fire retardant, and also for mechanical components used in food industry required corrosion resistant.
1.2344ESR(Groditz)
Steel has high purity, uniform structure, excellent toughness and tempering resistance, good thermal fatigue resistance and hardenability, and excellent mirror polishing and machinability. It has good high toughness and High plasticity, high wear resistance at high and low temperature and overall hardening performance are relatively excellent, with excellent toughness and plasticity in all directions.
P20HH(FINKL)
P20HH steel has good polishing performance, and the surface roughness value of the mould made is low. The molds made of this steel are generally quenched and tempered first, with a hardness of 28-35HRC (ie pre-hardening), and can be used directly after cold working into the mold, which not only ensures the use performance of the mold, but also avoids heat treatment. Deformation of the mold.
Mould gate design of clear parts, can design hot nozzle needle valve gate for directly gating, also sub gate, side-feeding fan gate.
Hot sprue valve gate: good liquidity, large-degree of position freedom, small gate, suits for thick clear products or large size products without appropriate area for gating. The only weakness is left gating trace. Car taillight products usually choose hot sprue valve gate.
Sub gate: sub gate can designed on mould ribs in cavity and core, side wall, and ejector; can choose gate point flexibly, pouring gate separates from part automatically, left slight gate marks. Weakness: it’s easy to pull material powder out on gate point and rush it out cause pits on surface; drying marks left easily in gate point area, need wiping it out by h
Side-feeding fan gate: molten plastic flow through gate, are assigned lateral evenly, decrease stress; decrease the possibility of air entering cavity, avoid causing streaks and bubbles. Weakness: pouring gate cannot separate from part automatically, left sprue marks on part’s edges, need tools to process pouring gate flat. Clear PC and PMMA usually adopt Side-feeding fan gate, which can proportion injection and pressure holding, and also good for pressure holding and feeding, in this way, it’s better for improving air lines, flow marks…etc, runner must be S-shaped and cold runner well, shouldn’t have sharp corners, which can lower the material flow speed, reduce jetting, and S-shaped runner can also tone down plastics. In designing the position of fan gate, the most appropriate idea is trying to design the gate point not obvious as much as possible based on assemble drawing.
Demoulding draft requirements on clear parts:for demoulding draft on clear parts side face, it should be larger than that of ordinary parts, because clear parts are more easier to scratch, and also need consider wall thickness and material, generally bigger shrinkage, larger demoulding draft. PC is high viscosity, greater holding force, higher rate of scratching, suggest demoulding draft at 1.5-2 °. PMMA and GPPS are high viscosity and brittle tendency, suggest demoulding draft no less than 2°.
Mould ejector for clear parts, scrap ejector, slide, ejector bar, blade ejector,Scrap ejector suits for products not allow down ejecting, only can let scrap ejector assists ejecting, no any ejecting marks on product surface, and scrap ejecting position need tools to cut flat.Slide, ejector bar: can be used for products don’t need very high appearance, this kind of ejecting position cannot be seen easily after assemble, but there may be parting line marks between push plate and direct ejector.
Blade ejector: when product has many ribs, large holding force and surface needs no marks, the only method is blade ejector. Blade ejector can be designed at the bottom of ribs, which makes product ejected evenly stressed. Blade ejector hole need processing with mid-cutting or fast-cutting, otherwise, mould is easy to have burrs. Blade ejector hole should be smooth, if not, it’s easy to break and burn.
thickness requirements on clear parts, too thick thickness is easy to cause shrinkage marks, bubbles and swash marks, need increase injection pressure and cooling time in injection molding, so thicker product, longer lead time. Generally the best product thickness is designed 1.5-3mm, and the proportion of length and width should not be too intervallic, otherwise, pressure would weaken with injection distance, need add injection pressure, which will cause different pressure in cavities, then cause internal stress, therefore cause product transformation. Product transformation issue can only be controlled and improved by increasing injection pressure, pressure holding time and cooling. If injection molding parameters cannot be improved, it can only improved by adjusting water running, according to product deformation feature, adopting a separate runner, and improving transformation by stagger water running temperature between cavity and core.
Plastics | Minimum wall thickness | Small-sized part wall thickness | Medium-sized part wall thickness | Large-sized part wall thickness |
PC | 0.95mm | 1.8mm | 2.3mm | 3.0-4.5mm |
PMMA | 0.8mm | 1.5mm | 2.2mm | 4.0-6.5mm |
GPPS | 0.75mm | 1.25mm | 1.6mm | 3.2-5.4mm |
PVC | 1.15mm | 1mm | 1.8mm | 3.2-5.8mm |
Polish requirements on clear parts: generally, clear injection molding finishing use oil strip, wool wheel, grinding paper….etc, which can make material surface plastic deformation, so as to remove bulges on part surface and get smooth surface, usually polish by hand. Product surface need high performance can adopt high precision grind polishing, like automotive lighting. High precision grind polishing adopt tailor-made grinders, in polishing liquid with grinding material, rotate at high speed on processed surface. Polish surface can meet roughness Ra0.008 μm. Common international polish standards are SPI A1,A2,A3. Polish process should be completed in two places, that’s to say, rough polish place should separate from fine polish place, and need pay attention to clean up the surface grind left in the former process.
Usually after rough polish by oil strip and 1200# grind paper, parts need shift to dust-free plant for polishing, make sure no dust in air stick to mould surface. Polish requires precision above 1 μm(include 1 μm) can be done in clean polishing room. If need much more precision polish, it requires absolute clean space, as dust, smog, dandruff, and saliva foam could damage high precision polished surface. Still need pay attention to avoid undercuts or round corners on parting face in polishing process, need make tags in parting area or make polishing jigs to avoid polishing cross boundary and problem that round corners on parting face.
After polish, need to pay attention to dust protection. When stop polishing, should remove all abraser and lubricant carefully, assure clean surface, and then paint transparent anti-rust oil on part surface.
NO. | Grades | Ra(um) | RZ(um) |
1 | SPI A1 | 0.025~0.03 | 0.1 |
2 | SPI A2 | 0.03~0.045 | 0.16 |
3 | SPI A3 | 0.06~0.07 | 0.25 |
Summary of experience
- High rotate speed of polishing machine needed
- Use polishing wheel with small diameter and most soft, such as pure silk polishing wheel.
- Use polishing paste with most finest grind, such as some good brands green polishing paste( vulgo: green oil)
- Use polishing paste with most finest grind, such as some good brands green polishing paste( vulgo: green oil)
Injection molding requirements on clear parts: as clear parts require high light transmittance, must need plastic surface are high quality, cannot have any streaks, porosity, whitening, blurring, pits, dark spots, discolor, poor gloss…etc, therefore in the whole injection molding process, should pay much attention to product design and put forward special strict requirements on raw materials, machines, and moulds. Secondly, because clear plastics usually are high melting point and poor liquidity, to assure high quality on product surface, usually need slightly adjust technological parameters on higher temperature, injection pressure and speed, which makes mould be full of plastic material, but without deformation or break by internal stress. There should be no impurities in raw material preparing and drying, and in the process of injection molding, adding material must use dry hopper, also pay attention to the air which should be filtrated and dehumidified in drying process, to make sure not to pollute material. Cleaned by injection molding screw detergent before and after production, assure no impurities, and also can cleaned by PE, PS materials.
Processing property of PC: high viscosity, high melting point, poor liquidity, injection temperature needs 270~320℃, adjustable range of material temperature is relatively small, is worse than PMMA. Injection pressure has less impact on liquidity, but because its high viscosity, larger injection pressure needed. To avoid causing internal stress, pressure holding time need as short as possible. Low shrinkage, stable dimension, but large internal stress, easy to break, it’s better to improve liquidity by raising the temperature instead of pressure, and decrease breaking by raising mould stability, improving mould structure and finish. When injection speed is low, crinkles are easily formed around pouring gate. To achieve high stability mould, runner and pouring gate need small resistance.
Processing property of PMMA: high viscosity, weak liquidity, must need high temperature and injection pressure, impact of injection temperature is larger than injection pressure. Raise injection pressure, which is good for improving product shrinkage. Wide injection temperature range, melting point is around 160℃, and decomposition temperature is higher than 270℃,therefore has wide material temperature range and good processing property. Improving liquidity by injection temperature. Poor shock and abrasive resistance, easy to scratch, fragile. Can raise mould temperature and improve cooling process to overcome these defects.
Inspection requirements on clear part: check all product features whether correct or not, inspect dimensions according to tolerances required in product drawing, and inspect at least 3 trials of products. Check parts to see whether have deformation, joint lines on surface, gas marks, black pots, greasy dirt, wave marks, are stock, bubbles, scratch, stuck, mismatch, cave, cut marks…etc.
Try GREFEE now,for free
We keep your uploaded files confidential and secure.
Inspect items | Level A standards | Level B standards | Level C standards | Notes |
transparency | can’t tell by eye | allow slight deviation around upper and lower limit | allow deviation in a relatively large range | make boundary samples(limit samples) for reference |
greasy dirt | no greasy dirt or sundries on surface | 0.5mm² Slight dirt but acreage <0.5mm² | acreage < 1mm² and not affect function | make boundary samples(limit samples) for reference |
Shrinkage marks | NO | slight shrinkage with small acreage | not affect part assemble and function | make boundary samples(limit samples) for reference |
gas marks | NO | not obvious with small acreage | not obvious with small acreage | make boundary samples(limit samples) for reference |
Gate point | +/-0.1mm | +/-0.3mm | +/-0.5mm | |
transformation | <0.1mm | <0.2mm | <0.5mm | make boundary samples(limit samples) for reference |
flash | Cutting marks ≤0.3mm, height<0.05mm, no flash | Cutting marks ≤0.3mm, height<0.1mm,no flash | Cutting marks ≤0.5mm, height<0.03mm | make boundary samples(limit samples) for reference |
Short shot | NO | not affect assemble, allow slight material | not affect assemble and function | make boundary samples(limit samples) for reference |
tolerance | within +/-0.05mm | within +/-0.2mm | within +/-0.5mm |
Packing requirements on clear parts
- Before packing, must inspect parts and ensure them meeting quality inspection requirements.
- Before packing, blow off material chips, trimmings, and broken filaments on parts, keep parts clean, stick protection film.
- After packing, must avoid scratch between parts. For some parts require structure, must avoid extrusion or breakage.
- In packing box, parts must be placed placidly and reliability, placing position can be vertical, horizontal, crossing or back-to-back, which depends on specific products. Must assure products not tipping inverted.
- After packing, product cannot beyond box’s surface, and surface’s box cannot be raised after packed. Must ensure boxes are stressed instead of inside products when boxes pile up.
- Same type products should packed in same specification boxes, and keep consistency of each box, quantities of boxes also should be the same between day and night shift.
- For every batch, only one mantissa box can be allow after packed, that’s to say, packing quantity of each batch can allow only one remnant box.
- Material identification card must be noted clearly, including date, shift, name, part name, specifications and models, quantity, serial numbers of boxes. Contents must be consistent with the actual situation. Same packing boxes only allow one material identification card, not allow 2 or more. Identification card must stick to the upper middle area of packing box uniformly, not allow reverse. Packed boxed must be placed in designated area with identification card face outward.
Common defects and improve solutions on clear parts
Streak: in the process of filling and condensation, internal stress affect all directions, vertical stress makes resin fluidity and illiquidity orientation, which cause different refractive index and flashy marks, after it extends, parts may have cracks.
Solution: clear up grease pits, fully dry, decrease and control resin temperature, increase injection pressure, adjust counter-pressure, low down screw speed, design appropriate gate sizeand position, increase exhausting size and position appropriately, check nozzles, runners, gate location to see if they’re blocked.
Bubbles: it main because the air in resin cannot be vented. In the process of mould cooling, vacuum bubbles formed because short shot or too fast cooling.
Solution: fully dry raw material, decrease resin temperature, increase injection pressure, speed and time, increase the wall thickness of gate point, adjust the mould temperature appropriate, increase cooling time, strengthen venting system, check nozzles, runners, gate location to see if they’re blocked.
Poor glossy on surface: it main because large roughness of the mould, besides, cooling too early making resin cannot copy the situation of mould surface, which all make product surface sags and crests and poor gloss.
Solution: increase resin temperature, increase injection speed and time, design appropriate gating system, increase mould temperature and cooling time.
Whitening: it main because dusts in air fall into raw material or raw material contains too much water.
Solution: clean up impurities and dirt, decrease and control resin temperature, increase injection pressure, decrease production lead time, adjust counter-pressure, increase mould temperature.
Joint lines: joint lines are formed from two or more gate points. When two strands of resin joint, thickness became larger in holes, nested areas, and joint areas.
Solution: modify product thickness, move the positions of joint lines, add spew wells, move joint lines to un-conspicuous positions by control flow speed by needle valve sequence or change gate locations, adjust product partial feature to eliminate joint lines, increase resin temperature, mould temperature, injection speed and pressure.
GREFEE Mold has powerful technical team, import injection molding machines and advanced processing machines. We’re experienced in producing clear parts, and are able to provide the most suitable product analysis report for customer, including parting line locations, gate points, ejector positions, thickness analysis, demolding draft analysis, deformation range analysis, finish requirements, and steel selecting. We’ll offer you best solutions, and help your projects set sail and come into market successfully!