Dark spots of products

Posted on :Nov 9 , 2022 By GREFEE
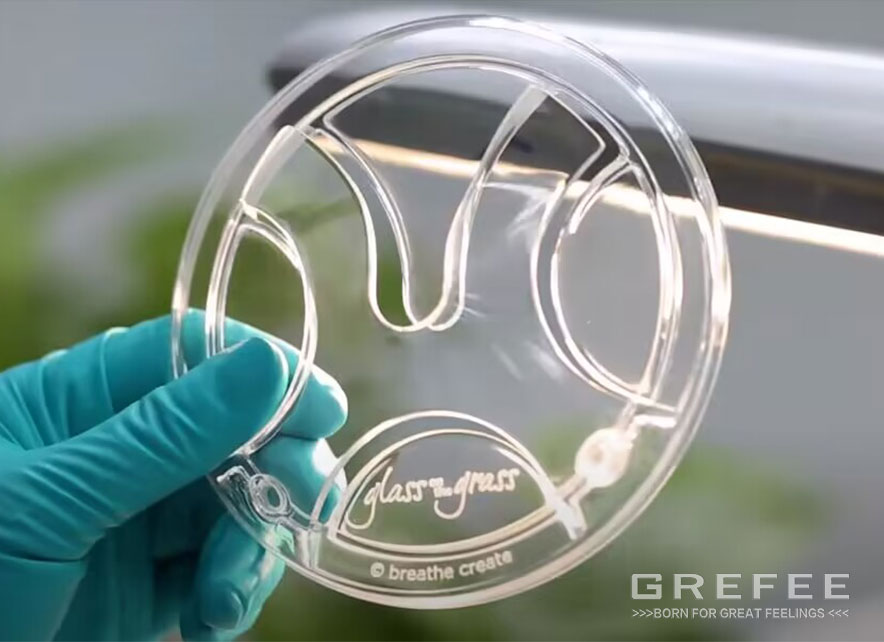
Surface defects of injection molding products include dark spots, gloss differences or fogging areas, and surface wrinkles or so-called orange peel. The defects are usually detected around the gate or far away from the behind of the sharp corner of gates. The cause for the defects can be found easily from two aspects, mold and molding.
Dark spots of products
Dark spots are usually detected around the gates, like the a faint halo of the sun. When producing products with high viscosity and low flowability, especially obvious in PC, PMMA, ABS. When the cooled surface layer resin is carried away by the resin flowing in the center, such visible defects can be on the surface.
People often misunderstood that the defects are often occur during the mold filling and holding pressure stages. As a matter of fact, dark spots usually appear around the gates. It is often started at the initial stage of the injection cycle. Based on experiment, surface slip often results from injection speed. More accurately, it is the flow velocity at the front of melt flow.
Even when the melt enters into the molds, the injection speed is constant. while, the flow speed may change, too. When entering into the gates of mold, the flow speed of melts is high. However, the melts flow starts slowing down in the mold filling stage. This change in the flow velocity at the front of the melt flow will cause surface defects of the product.
Reducing injection speed is one of the ways to address this. To lower down the speed of the front of the gates, we can separate the injection into several stages, and gradually increasing the injection speed. The reason of doing so is to obtain a constant flow speed during the whole molding filling stage.
The low temperature of melts is another cause for dark spots. Increasing the temperature of barrel, the back pressure of screw bar can reduce the possibilities of this. In addition, low temperature of mold can also produce the surface defects, the increase of mold temperature can overcome the surface defects.
The design defects of mold can produce dark spots around gates. The sharp corner at gate can be voided through changing the diameter. Be careful with the position and diameter of gates when designing to see whether it is suitable for the designing of gate.
Dark spots will not only occur at the gate position, while it will also appear after the generation of sharp corners, for example, the surface of sharp corners of products is generally quite smooth, but it becomes dark and rough later on, which is caused by the the cooling surface layer is replaced by internal fluid and slides due to high flow speed and injection speed.
Multiple-stage injection can be applied to increase the injection speed. The optical method is to increase the speed of melts after flowing through the margin of sharp corners.
In the area far away from gates, sharp change in angle of products will also cause this defect, and thus when designing an article, use smoother fillet transitions in those areas.
Improve gloss difference
For injection products, on the surface of products with textures, the difference in gloss is the most obvious. Even though the surface of mold is even, the irregular surface gloss cannot be found on the products. That is to say, some parts of mold surface effects are not paid much attention.
As the distance of the melt from the gate gradually increases, the injection pressure is gradually decreasing. If the gate distal end cannot be filled out, the pressure of this area is the lowest, which makes the texture of mold surface cannot be correctly duplicated on the surface of products. Therefore, the area where the cavity pressure is the largest (half of the fluid path from the gate) is the area where the gloss difference is the least.
To alter this situation, we can increase the temperature of melts and molds or pressure, and raise the time for holding pressure in the meantime to reduce the possibilities of gloss difference.
A good design of products can reduce the possibility of surface gloss. For instance, the server change of wall thickness can cause the irregular flow of melts, which cause the textures on the mold surface cannot be duplicated on the surface of products. Hence, even wall-thickness can eliminate the possibilities of this. Thick wall-thickness or too large ribs will increase the possibility of the gloss difference. In addition, insufficient venting could be another reason.
Cause of peeling
Peeling or surface wrinkling generally occurs in the end of the flow when using material with high viscosity to produce thick wall products. During the injection process, if the flow speed is low, the surface of products will quickly be solidified. With the increase of flow resistance, the from flow will become uneven, and cause the outer layer material cannot contact with the mold cavity sufficiently, resulting in wrinkling. These wrinkles will become irreparable defects after solidification and holding pressure. One way to address this is to increase the melt temperature and injection speed.
MORE BOLG
Insert mold in injection mold service
What are advantages and disadvantages of Zinc alloy and Aluminum alloy?
Inspection standards for injection molded partappearance
How to judge the quality of your plastic products?
Inspection standards for CNC machining
To ensure that your products are 100% qualified
Categories
Try GREFEE now,for free
We keep your uploaded files confidential and secure.