Design and manufacture for three-mold
Posted on :November 11 , 2023 , By GREFEE
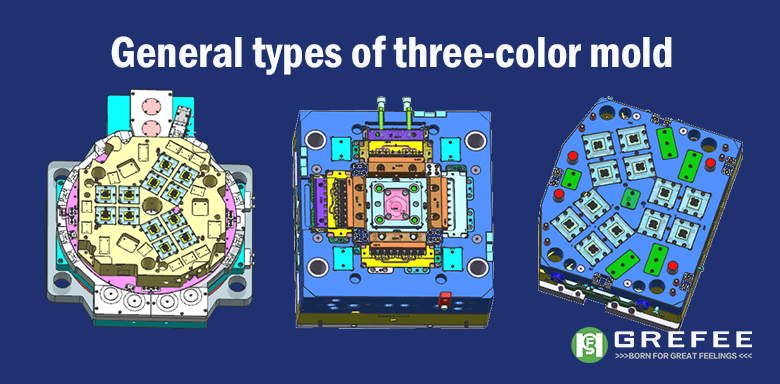
Sharing about three-color mold design and manufacturing technology in GREFEE
Product introduction
GREFEE provides injection molded plastic parts and subassembly to the world’s leading OEM, ODM, OBM, and massive customer companies who are dedicated to product R&D,involving automotive interior and exterior trim parts, communication parts, consumer electronics, personal wearable products, medical products,appliances, and personal consumer electronics, etc. .
GREFEE’s core businesses in injection molding are single-color, two-color, three-color and four-color injection molding production. With clean injection molding workshop, nearly 100 imported injection molding machines, and more than 200 CNC machines and fully equipped inspection equipments, GREFEE provides injection molding production services to customers from more than 50 countries around the world, and has won cooperation with many distinguished customers, like Tesla, Philips, Apple, Mindray, Johnson & Johnson, etc.
Advantage and application of three-color mold
01 Improve product quality
02 Reduce processing costs
03 Lift production efficiency
Application:
With the continuous development of industrialization, three-color mold technology is also developing and progressing sharply. Its products involve automotive, medical electronics, smart wearables, 3C products, and toy industries.t of technology, three-color molded products are increasingly applied to various industries, which also brings new vitality and market to the mold industry.
General types of three-color mold
Design tips for three-color mold
A. How to choose the 1st, 2nd, and 3rd shot:
1.With transparent parts: the first shot for transparent, and the second shot for non-transparent part(see picture A-2 on the right)
2. The first shot for plastic requires high temperature of molding material, and the second shot fore material temperature differs 20 ℃ at least.
3. If the 1st/2nd shot is a darker-color product, poor color mixing may occur after the third shot is molded.
4. Take the adhesiveness of the material into consideration, and confirm the physical properties with a material technician if necessary.
B. Optimize the structure in customer’s product drawing
1. Disassemble the product: a. simplify the mold structure as much as possible after disassembly with meeting the part requirements. b. ensure the strength of product connecting, such as adding some occlusal features
2. Optimize wall thickness: ensure the product wall thickness as average as possible to avoid the problems of thickness being too thick and too thin
3. Optimize sealing positions:
a. Generally adapt flat sealing in two-color/three-color molds(see picture A-2), contact sealing should be 3° at least.
b. Avoid any defects around the sealing positions, such as: lack of material or shrinkage problem
Design tips for three-color mold
C. Match the injection molding machines
1. The matching between the injection molding machine and the inject nozzle of the mold:The position of the machine nozzle should be designed based on the mold structure and the injection method.
2. The rotation direction and accuracy:Whether the processing movement of the machine fits the mold structure;
3. Ejection : consider the KO position and ejection method
4. For overall rotating structure, consider the water line and water returning roads:the fixed mold is usually on the outside, and make the movable mold side on the middle side in principle.
D. Mold structure design
1. According to the mold structure, arrange part position reasonably and consider the approach to take parts out.
2. Ensure the parting surface be as smooth as possible to avoid ridges, and adapt reasonable air avoidance solutions except for the sealing positions.
3. In designing of 2-color/3-color sealing, adapt touch sealing instead of contact sealing. If it cannot be avoided, ensure the angle as large as possible (at least 3 degrees or more)
4. For pin-point gate, should take the mold runner out every time to facilitate the next injection molding.
5. For mold side lock, better to adopt top locking, process the slot and frame together same time (to avoid deviations caused by multiple centerings) to ensure meeting accuracy requirements.
6. In designing, must pay attention to the rationality of processing to ensure the accuracy of mold processing. Fixture clamping (see A-1) can be adapted in processing if necessary. General principles of machining accuracy are as follows: priority grinder processing > slow wire processing > CNC processing > EDM processing;
7. Fully consider the exhausting of 2nd-color and 3rd-color mold. When 2-color are completely covered by the 1st color mold, air is easily trapped in mold (see B-1)
8. Mold material and its hardness are crucial factors to mold quality, because interworking can easily cause problems such as rubbing and burning.
9. Reduce mold weight: reduce the weight of the movable mold plates to reduce the burden on the machine
10. Problems in injection molding mainly because lack of consideration in designing, so usually requires mold flow analysis on products for early assessment and risk prevention.
Note: the 2nd color is surrounded by the 1st color both inner and outer sides, which makes air hard to vent
Solutions: 1. add inserts around sealing to facilitate air venting
2. add texture on the 1st color mold
Common problems with three-color molds
Product structure
1.Uneven wall thickness
2. Poor strength of product structure
3. Material reasons
Mold design
1.Lnsufficient and uneven water line design
2. Improper gate pointing or locating
3.Unbalanced ejecting design
4. product sticks to the mold
machine adjusting
1.Improper setting of cavity or core, or insufficient cooling.
2. Too high or low Injection molding maintaining pressure
Product structure
1.Uneven wall thickness, too thin or too thick
2. Material reason:very good mobility
Mold design
1.Radius or lack material around sealing locations,shrinkage.
2. Lacking pre-pressure around sealing areas;
3. Mproper gate pointing
machine adjusting
1.Insufficient or unbalanced machine clamping force.
2. Too high temperature of mold and material.
3. Improper setting of pressure maintaining.
Product structure
1.Uneven wall thickness.
2. Product feature: holes
Mold design
1.Improper gate pointing or locating.
2. Insufficient water running road.
3. Insufficient air-venting or air not out.
Machine adjusting
1. Too low mold temperature.
2. Lmproper injection molding parameters: speed/pressure
Product structure
1. Too thick material
Mold design
1.Improper gate pointing or locating.
2. Insufficient air-venting.
3. Insufficient water line
Machine adjusting
1.Improper setting of back pressure .
2. Missing baking the material.
3. Improper injection molding parameters: speed/pressure.
Product structure
1.The product has sharp edges and thin material
2. Single color mold not suits darker-color
Mold design
1. Improper gating location
2. Unreasonable part angle
Machine adjusting
1. Unclear of injection molding mahcine barrel
2. Poor colorant diffusion or poor colorant stability
Mold design
1. Unsmooth transition between sealing position and air avoidance
2.Too much pre-pressure around sealing position
3. Improper sealing structure
4. Part deformation
Machine adjusting
1. Too large size in injection
Basic factors for making good three-color molds
Mold design
Design is the most critical part. The rationality of the design directly determines the quality and life of the mold.
Processing equipment
Processing accuracy of the equipment is also an essential condition, which needs to be guaranteed in processing to meet the intercompatibility requirements of three-color mold.
Injection molding machine
Requires stable injection molding machines and skilled operator, man-machine to achieve best performance
processing and manufacturing
The accuracy of any component requires not only fine equipments, but also proper technology and processing to achieve high efficient man-machine operation.
Case study on three-color mold
Overall rotating structure
Structural principle: rotate core 120° to match different cavities for color changing injection molding
Notes:
1.Control the part size properly, too large size will cause crushing, while too small size will cause flashes.
2.Pay attention to all factors may affect the shrinkage and deformation of the product separating from the cavity after the mold open, must reserve safe position for steel on cavity for next color, specific value needs refer to the physical properties of the plastic material, product structure to make a comprehensive assessment.
3.Control the sequence of opening and closing the mold. Ensure closing cavity and core before slides, otherwise product may be damaged by slides.
Core rotating structure
Structural principle: this mold sets in four-color machine to do three-color injection molding, and this structure is designed to rotate 90° for color-changing injection molding
Notes:
1.Ensure the stability of the slide ejected product, no loose or deformation, otherwise, the product will be damaged during the second color injection.
2.Control the part size properly, too large size will cause crushing, while too small size will cause flashes.
Over mold structure
Structural principle: cavities are independent, products are ejected after the machine rotates 180°, and the intelligent manipulator fetches the part then rotates and put the part into core for color-changing injection(put the 1st-color part into core, the second-color part into the third-color part, and take the third-color part away). It’s same with over molding, just the intelligent manipulator repalces manual loading parts to achieve automatic production.
Notes:
1. Part size issue. Parts shrink not completely in the process of fetching and loading again, plus the dimension influenced by the time staying in the atmosphere, must pay attention to the assembly positioning size and the reserve steel room around sealing for the next color injection.
2. Ensure completely fitting when loading the part, when there’re slides, must ensure the cavity press the part firstly, then close the slides, otherwise, may cause cavity size changing or product damage.
Advantages of two-color, three-color in GREFEE manufacturing
Thanks to 20 years experience in designing and manufacturing two-color and three-color molds for our customers, we have accumulated abundant experience, solving various problems and continuously summarizing and improving, we believe that we have the ability to design and develop following two-color and three-color molds based on years of accumulated technical experience.
Types of over-molding
Classified by product:
-Hard material covers soft material (hard material only has soft material on one side)
-Hard material covers soft material (hard material has soft material on both sides)
-Hard material covers hard material
-Soft material covers soft material
Classified by mold structure:
-Two-color mold with core rotating right angle
-Parallel two-color mold
-Two-color mold with core ejecting and rotating right angle (60°, 120°, 180°, 360° etc.)
-Two-color mold with interchangeable cores inside mold
-Three-color mold and multi-color mold
Case studies on two-color, three-color and multi-color molds made in GREFEE
Hard material covers soft material two-color mold (hard material only has soft material on one side)
Hard material: PC-ABS
Soft material: TPE
Undercuts on both the inner and outer sides
Product feature: hard material covers soft material two-color product (only has soft material on one side of the hard material)
Product feature: five-color product
Hard material for the 1st/2nd/3rd/4th shots: COC
Soft material for the 5th shot: TPE
Product application: Medical care
Cavity: 2 cavities for hard material + 2 cavities for soft material
Mold material: 1.2343 ESR HRC 50~52
Mold life: 1,000,000 shots
Mold structure: two-color mold with core ejecting and rotating 60°right angle, 5 injection molding machines work at the same time, the rotating right angles can be designed in 60°, 120°, 180°and other angles.
Product portfolio for three-color product in GREFEE
A successful project relys on an experienced team and precise equipments. Our mold design engineers have an average industrial experience more than 15 years. Our CNC and injection molding machines are almost imported from Janpan and Switzerland. Combined with scientific management, we ensure your project be procced smoothly at GREFEE. If you need any project to discuss, just contact me right now! We will provide you DFM analysis report for free.
MORE BOLG
Insert mold in injection mold service
What are advantages and disadvantages of Zinc alloy and Aluminum alloy?
Inspection standards for injection molded partappearance
How to judge the quality of your plastic products?
Inspection standards for CNC machining
To ensure that your products are 100% qualified
Categories
Try GREFEE now,for free
We keep your uploaded files confidential and secure.