How does 3D printing raise the manufacturing capacity of high standards and high-added-values molds?

Posted on : April 9, 2022 By GREFEE
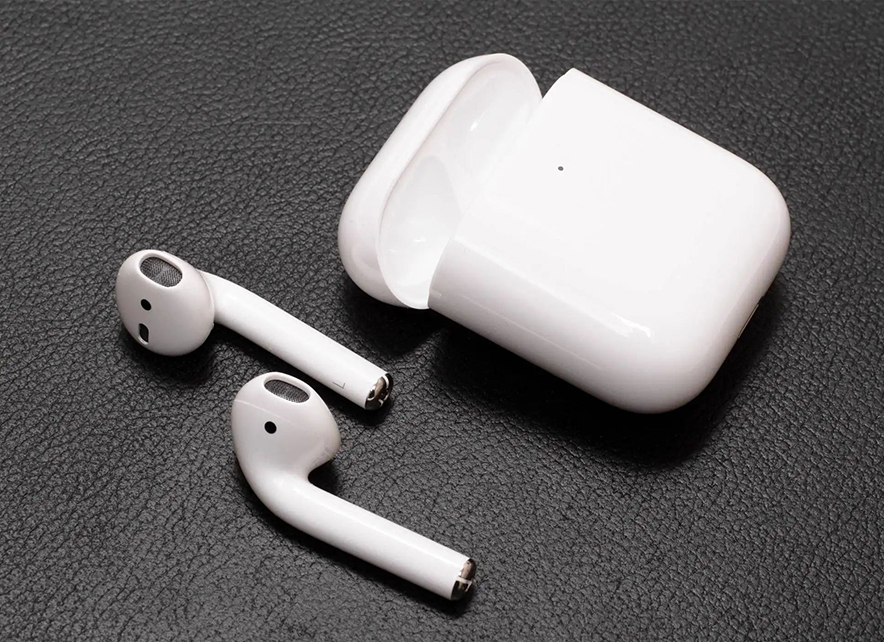
Through the 3d printing cases made by GREFEE in the last year, we know that the cases of the application of the 3C electronics field raised sharply. Among so many cases, we selected one, wireless earbuds charging box, which is not as simple as it looks
AirPods on the market
Earbuds look simple but are expensive. It increasingly owns a large part of the market due to its advantages of convenience, efficiency, and high added value. The famous product, AirPods, can be labeled with hundreds of dollars but still has its market. AirPods are the same thing as the Bluetooth earbuds of other brands.
They are composed of two parts: earbuds and a charging box. The height of a charging box is about 4-5cm and the width is only 2cm. Due to its needs in charging, the charging box must be of a highly accurate size to maintain good contact with the power supply.
Although it looks delicate, the manufacturing standards are rigorous. Thus, the forming process of this type of product is hard to control, especially the top cap area.
In the figure above:pic of the internal structure of the charging box’s top cap
Several difficult points
1. The core inserts has many reverse buckles, so it needs lifter to form.
2. The core inserts cannot be processed by the waterways of ordinary machines.
3. The temperature of core insert is high, forming cycle is long, the margin of the product is deformed and unstable.
Generally speaking, the manufacturing of this kind of product has two difficult points, which are 1. poor cooling effects due to the limitations of structure, so the product cannot make by ordinary machining. 2. The imbalanced mold temperature lead to margins deformation, and both of them can be solved by 3D printing technology.
3D printing conformal waterways design issue
In terms of the con-structure. There are many reverse buckles in the core inserts, and they need the lifters to help with the forming process, so the printing cannot be processed by waterways by ordinary machining methods.
Once the waterways cannot be designed inside, the mold without waterways will severely affect the time to eject. Long forming cycles and low production efficiency will directly affect the quality of the product.
As additive manufacturing works by layer upon layer, this allows the waterways distributed equally to follow the shape of products. (shown as the pic below) to shorten the production cycle and assists the product efficiency.
Pic 3: 3D printing conformal waterways of the top of earbuds charing boxTherefore, it is necessary to transform from traditional printing methods into 3D printing mold manufacturing. After setting the parameters of injection time, cooling liquid, mold temperature, and other machining parameters, we can carry out the mold flow analysis. Accounting to the displayed data (show as pic4):
Pic4: diagram of mold flow analysis comparison of the time for ejection temperature
The time when reaching the ejection temperature is about 95s after using conformal waterways technology, whereas the time for the ordinary waterways cooling is about 13s. It can be noticed that the cooling efficiency increases by 30%. From the comparison of data, the problems of 3D printing conformal waterways design will be solved and then the cooling time will be reduced, so does the production rates.
Mold temperature control of 3D printing
Mold temperate is mainly referred to as the cavity surface temperature in the forming cycle. Once the mold design and forming process has been confirmed, it is critical to maintain the proper temperature and make it distribute uniformly.
Uneven and different mold temperature distribution will lead to unequal contractility and internal stress. Hence, the forming area is easy to be deformed or has warpage, which affects the quality and forming a cycle to some extent.
One of the factors that affects the mold temperature is the distribution of waterways. In conventional molding, the internal structure of the top cap of the charging box and forming angle are serious issues which cause part of the components can’t be processed by waterways. Thus affecting the mold temperature. See pic5:
Pic 5: diagram of mold flow analysis of mold temperature
After adapting the conformal waterways, the mold temperature is about 54 degrees. While, the time for ordinary mold is as high as 84 degrees, which shows a decrease of around 35%. Hence, through the comparison of data, 3D printing can effectively control the mold temperature to achieve a balance mold temperature and avoid defects rates.
Polishing performance of 3D printing mold
In addition to the quality of products, whether the product can be used directly after printing is of great concern to many mold makers. The surface of parts that just have been 3D printed is rough. Some products have specific requirements, such as the AirPods we talk about today, which also have rigorous requirements about surface and accuracy due to their particularity and high price.
The mold products produced by ESU will leave a 0.8mm allowance on the base of the original dimension. The reason why is to facilitate the post-treatments and processing. The polishing performance could reach level A1.
Pic 6: diagram of polishing performance
The raw martial issue of 3D printing mold
Another factor that affects the 3D printing mold quality is the raw material. With many years of practical experience in the 3D printing field, GREFEE has independently developed multiple raw materials, like EM181、EM191、EM201, and other specific 3D printing used materials.
The material for making the mold part for the top cap of the charging box is EM191. Except for assuring the rigidity and strength of mold, it also has Rust and corrosion resistance plus good polishing performance.
Overall, according to the displayed data of the mold flow analysis by the modified 3D printing technology, the production rates increased by almost 30%, and mold temperature decreased by 35%.
No matter the production efficiency, coming quality, or the precise post-processing, even the aspect of raw material, GREFEE has fully prepared for any difficulties.
Although there are still many mold makers who are skeptical and insensitive about the 3D printing technology, we believe that we must stay ahead of others in terms of the high requirements and high added values to injection molding products. Utilizes the 3D printing technology according to the specific tasks.
Try GREFEE now,for free
We keep your uploaded files confidential and secure.