How to improve the accuracy of precision injection molding parts

Posted on : Sep 16 , 2022 By GREFEE
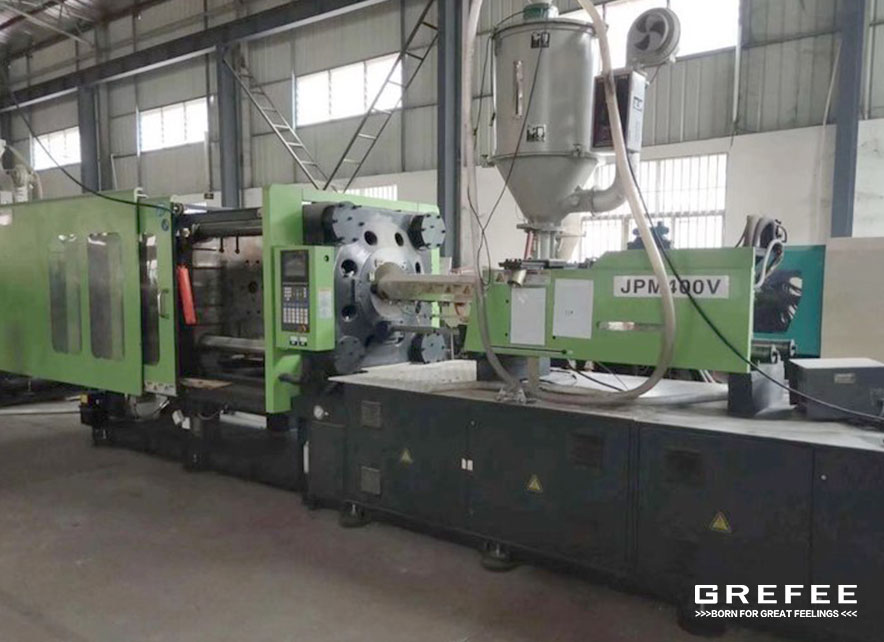
Most of the plastic electronic parts adopt injection molding because these materials have high designing accuracy and are processed with specific engineering materials. For those that cannot be processed with ordinary injection molding, but precision plastic injection molding. To ensure the properties, quality, reliability and long term stability, the material, equipment of injection molding parts, mold design, injection molding process and injection molding site management must be improved to produce high quality plastic products that meet the design requirement of products.
The so called precision injection molding refers to the appearance accuracy of injection molding products meet the strict dimension tolerances, geometric tolerance and surface roughness requirements. There must be many related conditions for precision injection molding, and the most essential factors are plastic materials, injection molding molds, injection molding processes and injection molding equipment. When designing a plastic product, it is better to start with engineering plastic materials. While, the selections of materials must be those with high mechanical property, stable dimension, good creep resistance, Materials resistant to environmental stress cracking. Besides, selecting the injection molding machines according to the materials, dimension accuracy, weight, quality requirements and expected mold structures.
During the process, factors that affect the products include temperature of molds, process control of injection molding parts, and the environment temperature and humid variations of the sites, as well as the later annealing treatments, etc. In terms of precision injection molding parts, mold is the key to obtain high quality precision injection molding parts. The molds that precision injection molding parts used should comply with the dimension, accuracy, shape, and material selection requirements of products. Eve though the accuracy and dimension are consistent, the actual dimension of products cannot be the same due to the difference of shrinkage. Thus, effectively control the shrinkage rate of products is essential to the precision injection molding technique.
Whether the design of injection molding parts is reasonable or not will directly affect the shrinkage rate of the plastic products. Since the dimension of mold cavity is obtained by plastic product size plus estimated shrinkage, while the shrinkage is a number recommended by the plastic manufacturers or handbook of engineering plastics, which is not only related to the gate types, gate positions, and distribution, but also the crystal orientation (anisotropy) of engineering plastics, shape and size of plastic products, distance and position to gate.
Meanwhile, it is also closely associated with the cooling distribution of cooling system in molds. The thermal shrinkage, phase transition shrinkage, orientation shrinkage, compression shrinkage and elastic recovery and other factors mainly affecting the shrinkage rate of plastics. While, these factors are also linked with the molding conditions or operating conditions of precision injection molded parts.
Thus, when designing the mold, the relationship between these influencing factors and the conditions of the injection parts and their apparent factors must be taken into account, such as the pressure of the injection parts and the cavity pressure and the filling speed, the temperature of the injection melt and the mold temperature, the mold structure and the gate form and distribution, as well as the influence of the gate cross-sectional area, the product wall thickness, the content of reinforcing filler in the plastic materials, the crystallinity and orientation of the plastic materials, etc. The above factors vary according to the materials. Other molding conditions, such as temperature, humid, continuous crystallization, internal stress after molding and changes of injection molding machine.
During the injection molding process, the plastic is turned from solid status(powder or pellet) into liquid status(melt), and then return to solid status(products). From pellet to melt, and then from melt to product, the temperature field, stress field, flow field and density field are required. Under the combined action of these fields, different plastics (thermosetting or thermoplastic, crystalline or non crystalline, reinforced or non reinforced) have different polymer structure morphology and rheological properties. Factors that affect the above fields will also affect the physical performance, dimension, shape, accuracy and appearance quality.
So, the internal relationship between process factors and polymer properties, structural morphology and plastic products will be demonstrated by plastic products. After figuring out the interlinks, it would be highly helpful for reasonably formulating the processing technology of injection molding parts, reasonably designing and manufacturing molds according to drawings, and even reasonably select the processing equipment of injection molding parts.
The injection rate of precision injection molding parts and ordinary injection molding parts are different. The former ones usually adopt high pressure or ultra-high pressure to inject, and high speed injection to obtain small molding shrinkage. Based on above, in addition to the normal designing factor of mold, the following should also be taken into account when designing precision injection molding parts.
- Adopt proper mold dimension tolerance.
- Avoid generating the molding shrinkage rate tolerance.
- Prevent deformation of injection molding parts .
- Prevent deformation of remolding .
- Minimize the manufacturing errors .
- Prevent the mold accuracy errors.
- Maintain the mold accuracy .
The shrinkage rate changes as the pressure of injection molding parts changes. Therefore, for single cavity mold, the mold cavity pressure should be consistent as much as possible. For multi-cavity mold, the pressure difference of each cavity should be quite small. Under the single cavity multi-gate or multi-cavity and multi-gate condition, same injection molding pressure must be the same to ensure the cavity pressure is the same. Regarding so, the position of gates must be balanced to ensure the mold cavity pressure is consistent. It is better to maintain the consistency of pressure of gates. The balance of the pressure around the gates is related to the flow resistance of runners.
Thus, before the pressure of gates reaching its balance, the first thing to do is to make it flow smoothly. Due to the influence of the temperature of melt and mold temperature to the actual shrinkage rate, the arrangement of mold cavities must be paid attention for the sake of deciding molding conditions when designing the precision injection molds cavities. As the molten plastic brings the heat into the molds, while the temperature range arrangement of molds usually is around the cavities, in concentric circle shape centered on the main flow channel. Thus, means like the balance of runners, arrangements of cavities and the concentric circular arrangement with main flow channel as the center are necessary for reducing the shrinkage errors between each cavity, expanding the allowable range of molding conditions, and lowering the costs.
The arrangement mode of precision injection molding parts should meet the requirements of balance of runners and arranged around the main channel. Moreover, it must adopt the cavity arrangement mode of taking the main channel as the symmetry line, otherwise it will cause the shrinkage difference between each cavity. Due to the big influence of mold temperature to shrinkage, it also affects the mechanical properties in the meantime, and other defects like blur on the surface of products. Thus, the mold should be used within the standardized temperature range, and it should make the mold temperature change as the time. The temperature difference between each cavity of mold should be the same, too. So, when design the mold, temperature control measures for mold heating or cooling, and in order to minimize the temperature difference between mold cavities, the design of temperature control cooling circuit is quite important.
Two connecting means in the cavity and core temperature control circuit: series cooling and parallel cooling. From the perspective of heat exchange efficiency, the flow of cooling water should be turbulent. However, in the parallel cooling circuit, the flow rate in one circuit that becomes a shunt is smaller than that in the series cooling circuit, so laminar flow may be formed, and the actual flow rate into each circuit may not be the same. Since the temperature of cooling water temperature entering into each circuit and the temperature of each cavity are the same, but the flow rate in each circuit is different, and the cooling capacity of each circuit varies, resulting in the temperature in each cavity is inconsistent.
The disadvantage of series cooling circuit is that the flow resistance of cooling water is large. There is a big difference between the temperature of cooling water at the front cavity inlet and the final cavity inlet. The temperature difference of the inlet and outlet of cooling water changes according to the flow rate. For processing precise small injection molds, the series cooling circuit is considered as a good choice due to low cost. If the properties of the used temperature control system can control the flow rate of cooling water within 2℃, the biggest temperature difference in each cavity can be maintained within 2℃.
The mold cavities and mold cores should have separate cooling system. In the designing of cooling circuit, as the heat extracted from cavities and cores are different, the thermal resistance of circuit is different, too. There will be a big temperature difference in water at the inlet of cavities and cores. If adopt same system, it would be difficult to design the cooling circuits. Generally, the mold cores of small-scale injection molds used by plastic parts are small, so water cooling system is hard to carry out. If possible, the core can be made of bronze material, and the solid beryllium bronze core can be cooled by plug-in cooling.
In addition, to prevent the warpage of injection molding products, a certain temperature difference between cavities and mold cores is helpful. Thus, it is recommended that to carry out temperature control and adjustment respectively when designing mold cavities and cooling circuits of cores. To ensure the mold accuracy of the pressure of injection molding parts under the clamping force, the process ability of grinding, milling, and polishing of cavity parts should be taken into account when deciding the structure of molds.
Moreover, the shrinkage rate is same as expected. However, the inner and outer dimensions of the molded products are difficult to meet the design requirements of plastic parts due to the center offset during molding. To ensure the dimension accuracy of fixed and moving mold cavity on the parting surface, the guide pins and guide sleeves used by ordinary molds should be set, it is also necessary to install conical positioning pins or wedge blocks to ensure accurate and reliable positioning accuracy.
The injection molding technique is essential for producing plastic parts, while the designing of precision injection molds is the key part of this technique. Properly designing the mold is the fundament and premise to obtain precision injection molding parts. Though appropriately setting the dimensions and tolerances of mold, carrying out measurements that stops the shrinkage rates of products, deformation of parts and de-molding, flashes, etc. on top of that, adopting the correct precision injection molding process, applicable engineering plastic materials and precision injection molding equipment to achieve the best result.
MORE BOLG
Insert mold in injection mold service
What are advantages and disadvantages of Zinc alloy and Aluminum alloy?
Inspection standards for injection molded partappearance
How to judge the quality of your plastic products?
Inspection standards for CNC machining
To ensure that your products are 100% qualified
Categories
Try GREFEE now,for free
We keep your uploaded files confidential and secure.