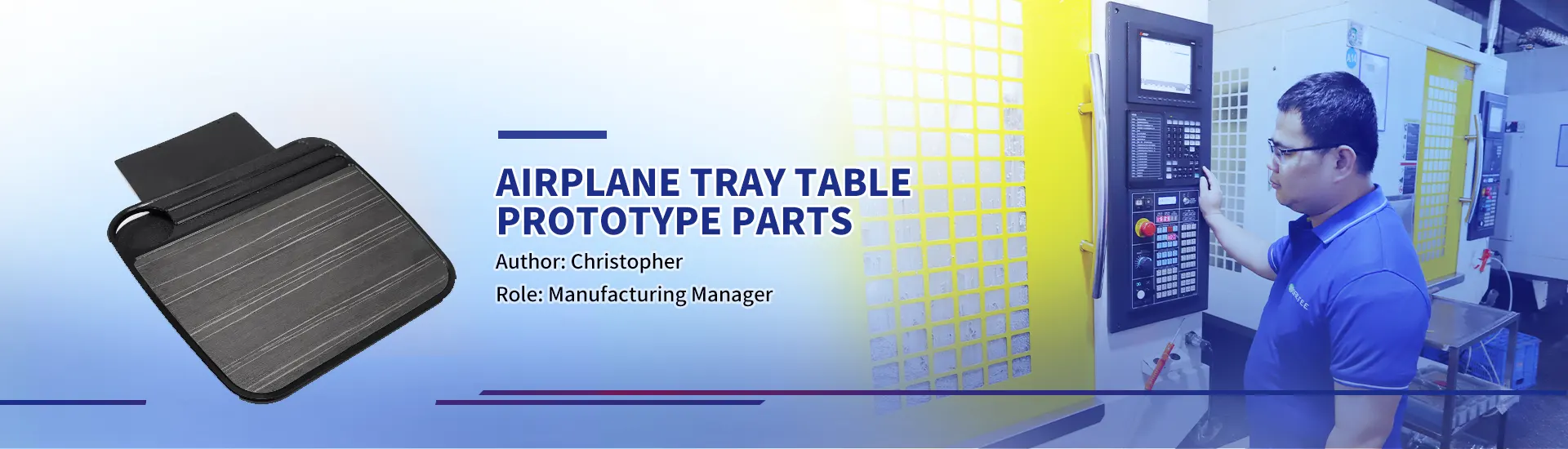
AIRPLANE TRAY TABLE-PROTOTYPE PARTS
Author:Christopher
Role: manufacturing manager
Since the airplane was invented in the last century, over hundreds of years of development, and flights to destinations around the globe has made aviation essential to most people. When it comes to airplanes, Boeing and Airbus will be the first to come to mind. Our small table panel is produced by our customer for the final Airbus model.
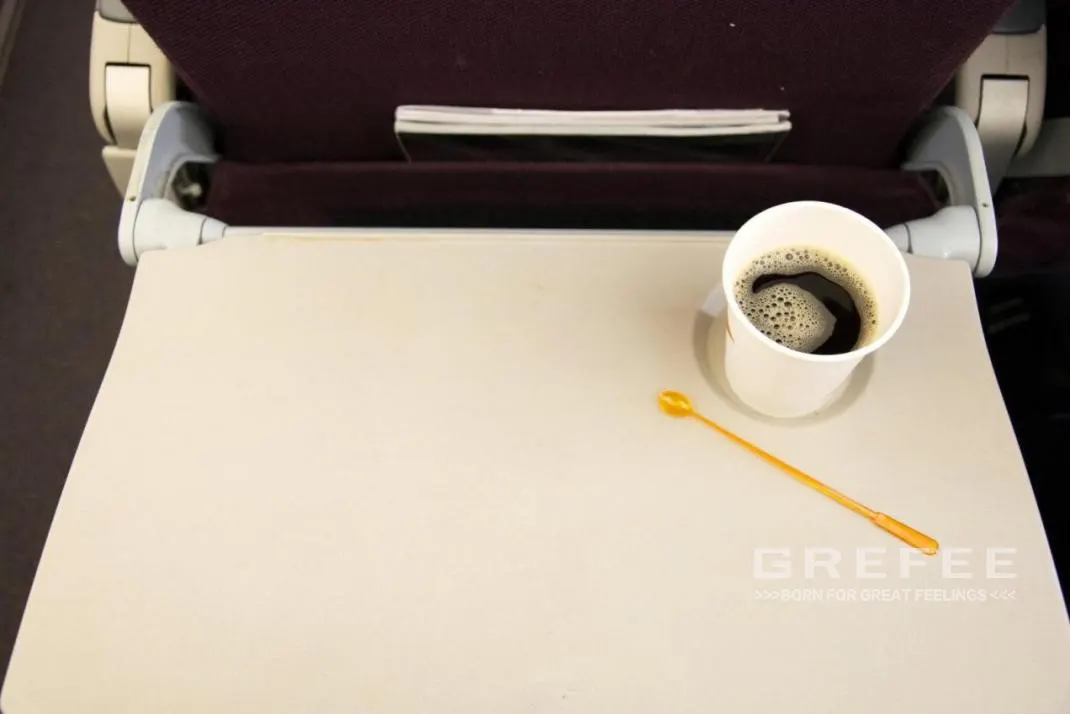
Regarding project:
A set of small tray tables is produced, which includes a set of prototype components consisting of 18 parts. They are assembled together using screws and 3M glue. It is divided into several parts, including the main body, upper and lower fireproof rubber plates, EVA plates, hinges, and cup holders.

Process applied: CNC
Post-processing applied: sandblasting, black anodizing
Materials used: 7075-T6, POM, EVA
Material selection:
7075-T6 is a high-strength and high hardness alloy aluminum, mainly composed of magnesium and silicon. Its hardness can reach up to HB150 or above. In addition, it has good processing and oxidation effects. According to statistics, more than 70% of all materials used in airplanes are aluminum or aluminum alloys.
Manufacturability evaluation:
Before project initiation, we evaluated the feasibility of mass production of the product in the future. The evaluation includes single piece production and batch production. A detailed analysis was conducted to check if there are any differences in the product or point out areas that need to be modified to improve its manufacturability. Here are a few suggestions we had for the product.
Manufacturability Assessment – Weight Reduction:
As an aerospace part, weight reduction is necessary. The whole table boards include 4 sets of cushion plates. Below you can see two diagrams. The first one is from the original design, and the second is after our modifications. By doing so, we have reduced the weight of the product on both sides resulting in a total weight reduction of about 23%.
Manufacturability Assessment – Product Optimization:
The cost of the product is related to the manufacturing time. The cushion block serves as a internal component, between the cup holder and the main body. Product optimization happens during design to ensure ease of processing. It can be seen that the original product had a small R-angle and could only be processed with a 2mm tool, and the tool needed to be replaced during the processing, which leads to an increase in programming cost and tool replacement time cost. The modified product can be directly processed with a 6mm tool without the need for tool replacement, thus, 15% of the time cost can be saved. This is also the purpose of our manufacturability evaluation, which allows us to provide customers with high-quality products at a lower price and faster speed.
Manufacturability Assessment – Assembly Optimization:
The original assembly was connected by 4 screws, and the right side of the rubber pad was bonded to the cup holder with 3M glue. There will be the assembly potential trouble as the cup holder and rubber are not fixed during assembly. Thus, a 0.5mm depth on the bottom of the cup holder based on the shape of the rubber pad has been designed to facilitate product assembly and also reduce the weight of the product.
Similarly, the same modifications on the back of the table was done, which allows the rubber and cup holder to be better placed on the main body after assembly.
Manufacturability Assessment – Assembly Optimization:
The rubber pad and cup holder are bonded together with 3M glue, which requires a very high level of adhesive placement. The glue must be in the appropriate position. If the glue is too close to the edge, it will overflow, and if it is too far from the edge, it will cause the rubber edge to curl up after bonding. Therefore, based on the bonding position of the product and the edge of the product, we have designed a glue groove with a bonding edge of 3mm and a middle spacing of 20mm. After testing, the addition of a glue groove can avoid both of the above problems at the same time.
Pre production:
A glue trough on the other side of the main body has been added where EVA needs to be placed, which allows for precise and fast dispensing without the need for fixtures during mass production. The automatic glue dispenser follows the position of the glue trough to ensure that the glue does not overflow and stop at the edges of the product, improving processing efficiency while ensuring product quality and aesthetic appearance on the outer surface.
incoming material inspection:
The material came with the material certificate and supplier certificate. We conducted the assessment according to the incoming material standards. Firstly, we will use X-ray equipment to analyze the composition of the product. As the material is AL7075-T6, we will use a hardness tester to perform hardness testing on the material to confirm that it has undergone tempering treatment. The hardness of AL7075-T6 is around H degrees.
Multi machine processing:
Two sides of the main body requires CNC machining. If it is for mass production, we can design different fixtures based on the two different sides of the product. When completing one side, flip the product and place it on another fixture to complete the processing of the other side.
Cleaning:
After finishing the process for each side, we have to clean the burrs to avoid product inaccuracy during the second treatment.
Post-treatment:
The surface of aluminum alloy product after CNC is very smooth and bright. However, as an active metal, aluminum can quickly react with oxygen in the air to form aluminum oxide on the surface, so we need to perform sandblasting and oxidation treatment on the product.
Preparation before oxidation:
Before oxidation treatment, we need to polish the product according to the product’s surface requirements and roughness requirements. Two methods, vibration polishing and chemical cleaning, are widely used for surface quality improvement. This can effectively improve the surface accuracy after oxidation.
Sand blasting:
Whether to start from sand blasting or oxidation depends on the oxidation thickness as sand blasting may cause the unevenness and defects to the oxide film on the surface and then affects the material quality. Normally, we start from sand blasting then oxidation. As sand blasting can remove the dust and burrs, which can provide a clear surface for oxidation and improves the uniformity and smoothness of oxide film.
Oxidation:
After sand blasting of the aluminum alloy, we need to do transparent oxidation treatment to the product to give the surface of aluminum alloy more texture, and create a protective layer on the surface to provide corrosion resistance protection.
EVA:
There are multiple EVA options on the Chinese market and we provide various patterns, thicknesses, and sizes for customers to choose from. The laser cutting equipment is controlled by a computer and can achieve an accuracy of 0.02mm.
Assembly Detail 1:
Through the customer’s original product, we can see that there will be glue overflow in the bonding area. After adding a glue sink, the position of the glue is fixed, and it can be seen that our product has no glue overflow, and the surface quality of the product has been improved.
Assembly Detail 2:
The main body, cup holder, rubber sheet, and cushion block are four independent parts that do not have fixed positions during assembly. By adding a rubber sheet groove on the bottom of the cup holder and a bracket on the main body to add a cushion block groove, the positions of the rubber sheet and cushion block are fixed, simplifying the assembly of the four products and significantly improving assembly efficiency.
Customer feedback:
Our customer sent us a letter of thanks after receiving the samples. Frederick mentioned in the email: “Thank you very much for providing us with qualified products in such a short time, which has saved us a lot of time in research and development. And we also appreciate your recommendation of a manufacturing solution suitable for mass production of the products. Your proactive work attitude and professional manufacturing knowledge have helped us better complete the design. This has been a very successful cooperation, and your product has met all the requirements. On top of that, we also appreciate your effort during the production process and the excellent design tips for mass production.