Introduction of common medical plastics

Posted on : Nov 4 , 2022 By GREFEE
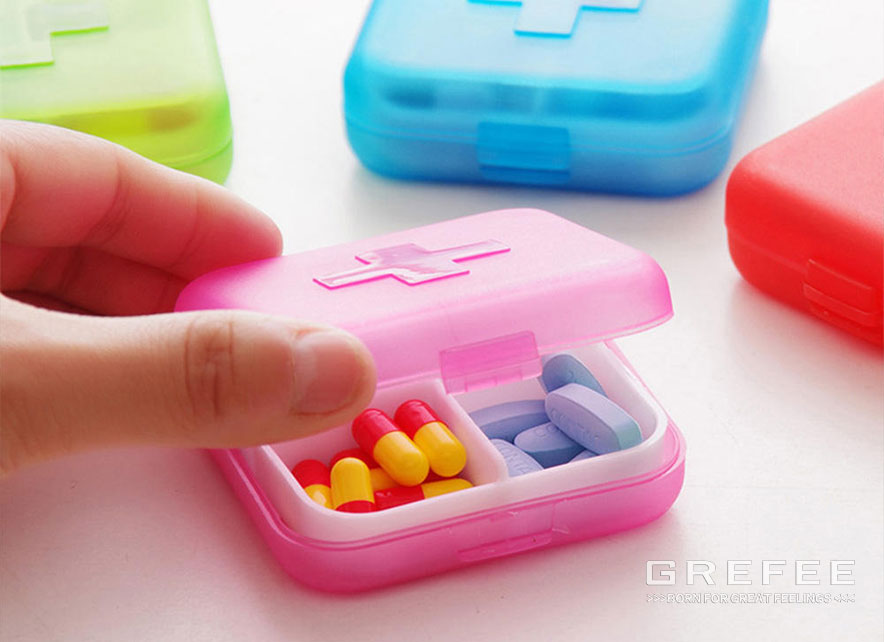
The common materials used in the medical industry include glass materials, metal materials. Compared with glass and metal materials, the main characteristics of plastics include:
(1). Low cost, can be reused without disinfection, suitable for the production of disposable medical devices.
(2). Simple to process, can be produced into various useful structures with its plasticity. Metal and glass are difficult to be made into products with complex structures.
(3). Rigid, high elastic, firm than glass.
(4). Good chemical inertness and biosafety.
These advantages give plastic a wide range of application in the medical appliances, including polyvinyl chloride (PVC), polyethylene (PE), polypropylene (PP), polystyrene (PS), polycarbonate (PC), ABS, polyurethane, polyamide, thermoplastic elastomer, polysulfone and polyether ether ketone, etc. Mixing can improve the properties of plastic to achieve the optimal performance of resin, such as polycarbonate / ABS, polypropylene / elastomer, etc.
Generally, the plastic is in the form of powder after composition, which cannot be used to produce directly. This is same as the extracting the grease from resin, is called resin, also named as powder material, which is a kind of pure plastic with poor flowability and thermal stability. It is easy to aging and decomposition as it is not resistant to environmental aging. To improve these disadvantages, adding the thermal stabilizers into the resin powder, anti-aging agent, UV resistant agent and plasticizer to improve its flowability after the granulation modification to produce various plastics with special performance, different brands, and are applicable to various processing technology
Hence, same kind of plastic has multiple numbers. According to the processing methods, there is injection grade, extrusion grade, blow film grade; According to the performance, there are high rigidity, toughening, etc. The plastic material commonly used by the medical device manufacturer are all the plastic particles after modification. For the products with special requirements cannot be found in the market, the factory can introduce granulation production line to process and produce plastic particles through different formula design.
Since the products will have liquid medicine contact or contact with human body, the basic requirements for the medical plastics are chemical stability and biosafety. Simply speaking, the composition of the plastic cannot be separated into the liquid medicine or human body, and will not cause toxicity and damage to tissues and organs. It is non-toxic and harmless to human body. To ensure the biosafety of it, the medial plastics in the market are usually authorized by the official department, and with obvious signs of medical grade to customers.
Selecting proper plastic types and numbers according to the requirement of structure and strength of mechanical products to decide the processing technique of material. The properties include processing performance, mechanical strength, use cost, assembly method and sterilization, etc. The following is the introduction of the processing properties and physical and chemical properties of commonly used medical plastics.
PVC, Polyvinyl chloride
As one of the largest plastic varieties in the world, PVC resin is white or light yellow powder. The pure PVC is random, hard and brittle, and rarely used. Different additives can be added according to different uses to obtain different physical and mechanical properties of PVC plastic parts. Through adding an appropriate amount of plasticizer to PVC resin, a variety of hard, soft and transparent products can be obtained.
None or a small amount of plasticizer contained in the hard PVC. PVC has good tensile, bending, compression and impact resistance, and can be used as a structural material alone. Soft PVC contains a large amount of plasticizers. Its softness, elongation at break and cold resistance increase, but its brittleness, hardness and tensile strength decrease. The density of pure PVC is 1.4g/cm3, and that for PVC plastic parts with plasticizers and fillers is generally 1.15 ~ 2.00g/cm3.
According to the report of market, 25% of medical plastics are PVC, which is due to the low cost of this kind of resin, wide application range, easy to process. Products of PVC medical products include: hemodialysis pipeline, respiratory mask, oxygen tube, etc.
Process conditions:
(1). Injection molding, extrusion, film blowing and rolling.
(2). No drying needed.
(3). Melting temperature: 170-200 oC, mold temperature :20-50 oC
(4). Injection pressure: can be up to 1500bar,holding pressure:up to 1000bar.
(5). Injection speed: to avoid the decomposition of material, low injection speed is recommended.
Main properties:
(1). Non-crystalline material, dissolvable in organic solvents, such as cyclohexanone and tetrahydrofuran. Cyclohexanone is usually used to bond PVC components.
(2). In the practical use, additives such as stabilizers, lubricants and colorants are often added.
(3). Lead barium additive is the most effective heat stabilizer for PVC, but it is prohibited in medical treatment. Calcium zinc additive is often used as a stabilizer for medical grade PVC.
(4). Phthalate (DEHP), as a plasticizer of medical PVC, the release of it is toxic to human body, which has attracted the attention of European and North American health organizations, either the drug regulatory authorities in China.
(5). Poor thermal stability, long-term heating will lead to decomposition, release hydrogen chloride gas, and make PVC discolor.
(6). Narrow application temperature range: normally within -15-5 oC.
(7). Low shrinkage rate: normally within 0.2-0.6%.
(8). Polar material, easy to adsorb with some polar drugs.
(9). Soft PVC film can be manufactured into bags by high-frequency welding, such as bag infusion sets and urine bags.
PE, Polyethylene
PE is milky white, tasteless, odorless and non-toxic glossy wax particles, which is the largest variety in the plastic industry. Due to its low price and good performance, PE has been widely used in industry, agriculture, packaging and daily industry, and plays a vital role in the plastic industry.
Several main categories of PE include low density polyethylene (LDPE), high density polyethylene (HDPE) and ultra high molecular weight polyethylene (uhdpe). HDPE has fewer branches on the polymer chain, higher relative molecular weight, crystallinity and density, higher hardness and strength, poor opacity and high melting point. It is commonly used for injection molding parts. Due to its multiple branches, so it has small relative molecular weight, low crystallinity and density, and good softness, impact resistance and transparency, which is commonly used for film blowing and is an alternative to PVC. HDPE and LDPE can also be mixed according to the performance requirements. UHDPE has been an ideal material for producing the artificial hip, knee and shoulder connectors due to its high impact strength, low friction, stress cracking resistance and good energy absorption characteristics.
Processing conditions:
(1). Dry: low water absorption rate, normal no need to dry. Melting temperature 170-260 oC,mold temperature 20-40 oC
(2). Injection pressure: maximum can be 1500bar, holding pressure: maximum can be 750bar, injection speed: high injection speed.
(3). Runner & gate: all types of runners and gates. Suits hot runner molds.
Main characteristics:
(1). Large molding shrinkage rate, easy to shrinkage and deform.
(2). The processing temperature of PE is wide, which is hard to decompose (decomposing temperature is about 300℃), processing temperature: 180~220℃. If the injection pressure is high, the density of products is high, and the shrinkage rate is low.
(3). Moderate flow performance, long term holding pressure, consistent mold temperature (40~70℃). The crystallinity of PE is associated the molding process conditions. It has high solidification temperature and low mold temperature, and low crystallinity.
(4). During the molding process, the temperature of material and mold should be higher. The injection pressure should be lower with the guarantee of the quality.
(5). Similar to PP, PE is non polar materials with low drug adsorption, which are easy to adhere. They cannot be processed into bags by high-frequency welding, but the heat sealing process.
PP,polypropylene
PP is colorless, tasteless and non-toxic. It looks like polyethylene, but it is more transparent and lighter than polyethylene. PP is a kind of thermoplastic with excellent performance, which has the advantages of small specific gravity (0.9g / cm3), non-toxic, easy processing, impact resistance and flexural resistance. It is widely used in daily life, including woven bags, films, turnover boxes, wire shielding materials, toys, car bumper, fibers, washing machines, etc.
Medical used PP has high transparency, good barrier and radiation resistance, making it being widely used in the medical equipment and packaging industry. Non-PVC is based on PP, which is the alternative of PVC.
Processing conditions:
(1). Injection molding, extrusion, blow forming, or made into film.
(2). Drying: low water absorption, no need to dry.
(3). Melting temperature:220-270 oC,not exceed 275oC, mold temperature:40-80 oC,50 oC is recommended.
(4). Injection pressure: up to 1800bar. Injection speed: high injection speed can minimum the internal pressure. If there are surface defects, low speed injection under high temperature is recommended.
(5). Runner and gate: for Cole runners, typical diameter range for runners is 4-7mm. Circular injection port and flow channel are recommended. All types of gates are applicable. The typical diameter range is 1~1.5mm or 0.7mm. for margin gates, the smallest depth of gates should be half that of wall thickness. The smallest width of gates should be two times that of wall thickness. PP is the material for hot runner system.
Major characteristics:
(1). PP is a semi crystalline material with high melting point, good heat resistance, and can be sterilized at temperatures above 100 ° C.
(2). Better than PE in yield strength, tensile strength, compressive strength, hardness and elasticity.
(3). Homopolymer PP has large brittleness, and the random copolymer PP synthesized with ethylene has better toughness and stronger impact strength. Generally, the copolymerizing PP or adding thermoplastic rubber to increase its flexibility and low-temperature impact resistance suits the products used under low temperature conditions. The non-PVC large infusion bag is made of copolymerized PP and elastomer blend modified materials.
(4). Prone to depolymerize and age under the action of oxygen, heat and light, so requiring the anti-aging agent.
(5). Not easy to adhere, treatments needed before bonding, and special adhesive should be used. The cyclohexanone used by the equipment factory cannot meet the requirements.
(6). Poor coloring, large shrinkage rate (normally 1.6-2.5%), poor burning resistance, easy to ignite.
(7). Non-polar material with low adsorption capacity for drugs.
(8). PP film is usually welded into bags by heat sealing method, which is more complicated than high-frequency welding PVC bags in the processing techniques. Non PVC large infusion bags are produced with full-automatic equipment to ensure stable process and reliable quality.
Polystyrene (PS) & K Resin
PS is the third largest plastic variety, ranked after the polyvinyl chloride and polyethylene. It is usually processed and applied as a single component plastic. PS is light, transparent, easy to dye, with good molding and processing performance. These properties make it a great material in daily plastics, electrical parts, optical instruments and cultural and educational supplies. It is hard and brittle, and has a high coefficient of thermal expansion, which limited its application in engineering. In recent decades, modified polystyrene and copolymer based on styrene have been developed, which overcome the disadvantages of polystyrene. K resin is one of them.
Kresin is an amorphous polymer, transparent, tasteless, non-toxic, with a density of about 1.01g/cm3 (lower than PS and as), formed by copolymerization of styrene and butadiene. Its impact resistance is higher than PS, better transparency (80-90%), and thermal deformation temperature of 77 ℃. The amount of butadiene contained in K material varies with its hardness. K has good processing performance due to its good fluidity and wide processing temperature range.
Products of PS & K resin include cups, covers, bottles, cosmetics packaging, clothes hangers, toys, PVC substitute products, food packaging and medical packaging supplies.
Processing characteristics:
(1). Injection molding, extrusion and film blowing are seldom.
(2). Water absorption of K. No need to dry before processing. If K is stored with being exposed under the environment with high humidity, it needs to dry (under 65 oC).
(3). Good flowability, easy to process. The processing temperature range is limited, normally within 170~250 oC.
(4). When the temperature is higher than 260 oC, or stay above 20 minutes in the barrel, the K material will be thermal decomposed. It may even change color and become brittle. “low pressure, medium speed and medium temperature” methods should be processed and the mold temperature should be between 20 and 60 OC
(5). Thick-walled products can be cooled in the water to obtain even cooling to avoid the hollows.
Main characteristics
(1). High transparency and surface finishes
(2). Low shrinkage (0.4~0.7%)
(3). Compared to common PS, K resin has good rigidity. For some thick-walled products, there is still cracking issues. Carefully select the brand before use.
(4). Low heat resistance, and the thermal deformation temperature is generally 70-98 ° C, which can only be used at a low temperature.
Poor chemical resistance, easy to be eroded by oil, acid, alkali and strong organic solvent.
ABS,Acrylonitrile Butadiene Styrene copolymers)
ABS has rigidity, hardness, impact resistance, chemical resistance, radiation resistance and ethylene oxide disinfection resistance to a certain extent. It is mainly used in medical treatment as surgical tools, roller clips, plastic needles, tool boxes, diagnostic devices and hearing aid housings, especially the housings of some large medical equipment.
Processing conditions:
(1). In the medical field, normally processed by injection molding, film blowing and tube extrusion are rare to use.
(2). Drying treatment: ABS material is hygroscopic and requires drying treatment before processing. The recommended drying condition is at least 2 hours at 80-90c. The material temperature is less than 0.1%.
(3). Melting temperature:210-280 oC, recommend temperature:245 oC。
(4). Mold temperature: 25-70 oC. (mold temperature affects the surface finishes of injection parts. Low temperature will lead to low surface finishes) injection pressure: 500-1000bar,injection speed:moderate and high speed.
Main characteristic:
(1). ABS is synthesized from acrylonitrile, butadiene and styrene, which enable ABS with good comprehensive mechanical properties. Acrylonitrile enables ABS with good chemical corrosion resistance and surface hardness, butadiene enables ABS with high hardness, and styrene makes ABS have good processability and dyeing performance.
(2). The properties of ABS mainly depend on the ratio of three monomers and the molecular structure in the two phases, which allows high flexibility in product design, and produces hundreds of ABS materials of different quality in the market.
(3). Excellent processability, good appearance characteristics, low creep and excellent dimensional stability.
(4). Accept secondary processing, such as machining, bonding, fastening, electroplating, painting and ultrasonic welding.
(5). Great impact strength resistance, and will not drop under low temperature. Good mechanical strength, hardness, and certain wear resistance
(6). Great cold resistance, oil resistance, water resistance, chemical stability. Tolerant to water, inorganic salt, alkali and acid. Dissolve into the detones, aldehydes, esters, chlorinated hydrocarbons and form emulsion. Insoluble in most alcohols and hydrocarbon solvents, but will soften and swell in long-term contact with hydrocarbons.
PC,Polycarbonate
The typical characteristics of PC are toughness, strength, rigidity and heat-resistant steam disinfection, which makes it the first choice for producing blood dialysis filter, surgical tool handle and oxygen tank (when in cardiac surgery, this instrument can remove carbon dioxide from blood and increase oxygen). The applications of PC products in medical industry also include needle free injection system, perfusion instrument, blood centrifuge bowl and piston. With high transparent performance, it is often used to make the myopia glasses.
Process conditions:
(1). PC is often injection molded in the medical field, and few are extruded and blown.
(2). Drying:water absorption,drying before processing is important。recommended drying conditions are 100 oC ~160 oC,3-4hrs。the humidity before processing must be lower than 0.02%。melting temperature:260-340 oC。mold temperature:70-120 oC。
(3). Injection pressure: try to use high injection pressure.
(4). Injection speed: low injection speed for small gates. High injection speed for other types of gates.
Main characteristics:
(1). PC is a kind of non crystalline engineering material with excellent impact strength, thermal stability, transparency, gloss, bacterial inhibition, flame retardancy and pollution resistance.
(2). High impact strength resistance. Low shrinkage rate, which is 0.4%~0.8%, good dimension stability.
(3). Great mechanical properties, high temperature resistance, creep resistance, wear resistance, heat resistance, cold resistance. Embrittlement temperature below 100 ℃, long-term working temperature up to 120 ℃.
(4). The molding parts can achieve great dimension accuracy, and can maintain the dimension stability within a wide temperature range.
(5). Poor flowability, processing temperature (above 300 oC). The injection molding process is difficult.
(6). High cost, which is 2-3 times that fo PE or PP.
(7). Great weather resistance: resistant to water, dilute acid, oxidant, reductant, salt, oil and aliphatic hydrocarbon at room temperature, but not to alkali, amine, ketone, fat and aromatic hydrocarbon.
(8). The biggest disadvantage is that easy to crack, poor fatigue strength.
PTFE (Polytetrafluoro ethylene)
PTFE is an important kind of plastic, which is in the form of white powder, looks like waxy, smooth and non sticky. The excellent properties of PTFE outweigh that of other thermoplastics, so it is the best plastic, of which the friction coefficient is the lowest among all kind of plastics. Due to is great biocompatibility, it can be used to make instruments directly implanted into human body such as adult blood vessels.
Molding performance:
(1). Hard to process. Generally, the powder is cold pressed into a blank, and then sintered or extruded. It is better to purchase it directly when the quantity is small rather than manufacturing.
(2). Poor flowability, easy to decompose. Corrosive gas generated during the decomposition. Strictly control the molding temperature, not exceed 350 oC,mold should be heated to 100-150 oC。
(3). Clear pellet, injection molding, extrusion molding. Molding temperature 300-330 oC. When the temperature is above 350 oC, it is easy to cause discoloration or bubble generation. It should be formed at high speed and low pressure, and it is difficult to de-mould.
(4). Weight ration1.7g/cm3,molding shrinkage :3.1-7.7%,molding temperature:300-330 oC。
Main characteristic:
(1). Best chemical resistance and stability so far among all plastics, and is stable to strong acid, strong alkali, various oxidants and other highly corrosive media, even boiling “aqua regia”
(2). Good creep resistance and compress strength. High tensile strength. Elongation rate up to 100-300%, excellent radiation resistance.
(3). Great heat and cold resistance, can be used in the range of – 195 – 250 OC for long term without denaturation.
(4). The disadvantage is high thermal inflation coefficient, but poor wear resistance and strong mechanical strength, insufficient rigidity, hard to form.
MORE BOLG
Insert mold in injection mold service
What are advantages and disadvantages of Zinc alloy and Aluminum alloy?
Inspection standards for injection molded partappearance
How to judge the quality of your plastic products?
Inspection standards for CNC machining
To ensure that your products are 100% qualified
Categories
Try GREFEE now,for free
We keep your uploaded files confidential and secure.