Unibody application in electronic product industry

Posted on : Nov 23 , 2022 By GREFEE
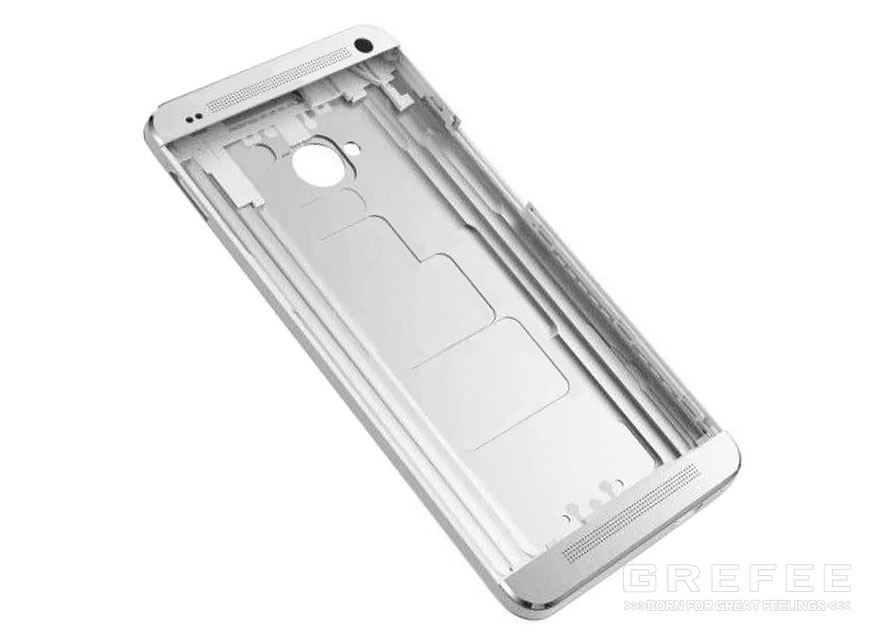
Unibody, also known as integrated molding or integrated body. Explanation for this principle is that one kind of mechanical operation technology that squeezes the aluminum alloy into board. Then, it is integrally formed by numerical control machine tool. This is mainly for the metal material (especially for aluminum alloys), which can produce parts with integrated structural features by CNC machining. This part is full of integrity characteristics, which not only can be most of the appearance of the product, but also serves as a fixed frame for internal parts.
This solution is not only for metal parts but also for other materials, such as plastic. Through the Uni Moulding, it can produce integrated housing parts, which is unable to be molded by traditional injection molding process, but requires to disassemble multiple parts to make a whole. However, if the integrated injection molding process is applied, a simple and clear appearance can be obtained. In the meantime, the number of the parts will be reduced and the seam between two parts can be reduced as well.
overall, Unibody can be divided into:
1. Metal Unibody 2, plastic Unibody 3, ceramic Unibody
The metal unibody which is the mostly used one. Apple introduced the Unibody to the world, and was also the first one that adopted this technology into the consumer electronic products with great comments. Since then, other companies also imitated. The metal unibody phone cases became a common feature of different phone companies.
Due to the great mechanical processing properties of aluminum alloys, phone cases with multiple beautiful colors can be obtained through anodic oxidation coloring. The aluminum alloy anodizing Unibody was the keynote of Apple’s product design at that time is still used today.
However, the first consumer electronics that adopted this technology was not iPhone, but MacBook Air, a laptop that is thin enough to fit in a file bag.
The display screen and the main body of the MacBook Air are all the Unibody integrated body, and most of the parts are fixed to the high-precision integrated aluminum alloy body by screws.
Since iPhone 5 in 2012, the body of smart phone is made of aluminum alloy anodized Unibody, which has been the integrated one.
Indeed, due to the consideration of the antenna signal, Apple has to inlay four sections of plastic strips through nano injection molding on the back of the aluminum alloy case. Even it is already sensational perfect and is almost integrated without seam between metals and plastics, but these “white belts” have a great impact on vision.
Why not make the color of the plastic antenna strip close to the fuselage?
Firstly, the plastics that can be applied into the Nano injection molding include PPS、PBT、PA6、PA66、PPA. It is hard to produce bring colors because the colourability and adhesive force of the engineering plastics are poor. In addition, based on the consideration of industrial design, it is hard to use two different materials, metal and plastic, to produce products with same colors and sensation. However, the iPhone will be improved under continual improvement.
All metal mobile phones need to solve the antenna signal problem. There are several ways in the industry:
Full CNC+NMT+anodizing (antenna white tape design)
One typical example is the iPhone 6 to iPhone 8, of which the process is to start with one aluminum alloy to produce the whole structural parts by CNC machining, and cut out the antenna slot, then inject the plastic into the corresponding antenna slot by Nano injection molding to connect the metal and plastic together. Lastly, completing the treatments, including sand blasting, anodizing, coloring, etc.
2. Forging+CNC+NMT+anodizing (three-stage design)
The antenna processing of the typical OPPO R7 is similar to that of iPhone 5, adopting three section structure on the back. The upper and lower antenna covers of OPPO R7 uses ordinary plastic. The color of the plastic can be made as similar as that of the body, then is fixed to the body with double-sided adhesive tape. Compared to iPhone 5, thicker structural members rough type through forging to reduce the time of CNC machining to lower the cost. In the meantime, the adopted metal material is the aluminum alloy that can be anodized. Later, it can be made into an integrated appearance with metal texture. However, even if the visual difference is reduced through upper and lower plastic parts by spraying and painting, there is still color difference. The final visual effect will affect the integrity to some extent.
3. Die casting+CNC+NMT+spraying and baking paint (overall painting design)
The typical Meilan Metal is more cost effective than forging. With the aluminum alloy die casting, most structures of the phone body has been completed at this stage, such as injection molding area of antenna slot. Later, only local CNC is required for some areas with high accuracy requirements.
Next, nano injection molding is carried out for the upper and lower antenna slots, as shown in the figure below.
The final step is to carry out spray baking paint. Since the phone body is made of die casting aluminum alloy with high content of silicone, which is not suitable for the anodizing. The Meilan Metal is overall spraying metallic painted (which is to add pearlescent powder or aluminum powder into the paint) to achieve the multi-color integrated body.
The phone body made of pure metal texture of painting is not as obvious as that of anodizing, but can quickly hide the antenna injection molding to avoid the visual obtrusiveness.
4.Since the final part is overall painting, what is the difference between directly making plastic fuselage?
The difference between vision and texture may be not evident. The reason why adopting an integrated metal body is that the thickness of the body is light and thin, and the strength of the phone body is sufficient.
Conclusion: the metal Unibody has some advantages of irreplaceability which makes it the main reason why that Apple has been stick to it with their products.
1. Improved overall appearance, simple and beautiful
The most significant advantage of Unibody is that it increases the integrity of appearance of products, and reduces the unnecessary details to improve the anesthetic values and style of products.
2. Reduces the parts, screws and assembly steps
The own structural rigidity and plasticity of metal parts largely reduces the design of stiffener and bone position, as well as the assembly processes such as inlaying, welding and pasting, which modifies a great number of stations and circulation links.
3. No seam, parting line, and draft angle
Defects are unavoidable in injection parts, like assembly clearance, clamping line of die and draft angle, Unibody can effectively reduces the possibility of this kind of problems, such as product aesthetics and design reduction.
5. Avoid common appearance defects of moulds
In addition to design, there are technical defects in injection molding, such as shrinkage, air lines, flow marks, weld lines, etc.
Higher degree of freedom in appearance design, which can break through the appearance limitation of injection molding process
Some more breakthroughs, changes and styles can be tried because of getting rid of some limitations of the mold, especially when multi-axis and multi head equipment is gradually popularized so that the modeling ability of CNC in most scenarios can be as good as that of 3D printing.
6. Recycling and environmentally friendly
Due to the reduction of the use of parts and joining process, therefore, the materials contained in the Unibody body shall be reduced as much as possible, which is beneficial to the classified recycling and reuse of wastes. In the meantime, it also reduces the use of toxic substances and emission with excellent environment protection.
Disadvantage of Unibody: high cost
- CNC has extreme high requirements in the accuracy of equipments, so its processing length is also longer than other processes, like injection molding and stamping. It requires high investment in equipment at the early stage. As long as the mass production is generated, the cost can be averagely distributed. Thus, small companied or manufacturing factories are unable to purchase mass equipments, but only large companies.
- Similar to other subtractive processes, full CNC consumes a lot of materials. Thus, the material cost of it is also higher than that of other molding processes (die-casting, stamping, etc.). Fortunately, the waste of CNC can be recyclable.
MORE BOLG
Insert mold in injection mold service
What are advantages and disadvantages of Zinc alloy and Aluminum alloy?
Inspection standards for injection molded partappearance
How to judge the quality of your plastic products?
Inspection standards for CNC machining
To ensure that your products are 100% qualified
Categories
Try GREFEE now,for free
We keep your uploaded files confidential and secure.