The Quality of the Die Casting Material Determines the Quality of Die Casting Products.

Posted on : June 1, 2022 By GREFEE
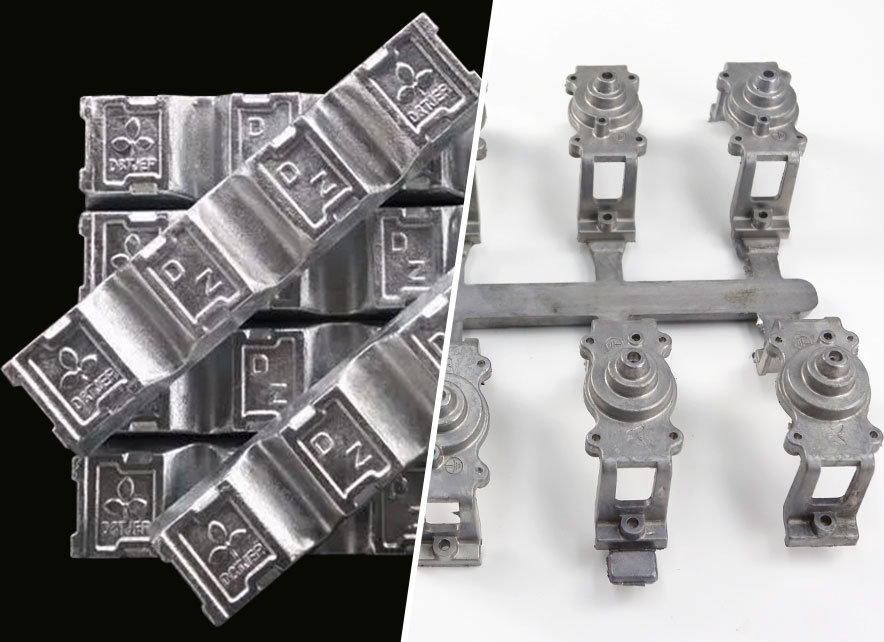
Material management is essential to quality control and qualified product manufacturing. Die casting materials include the main material (aluminum alloy ingot) and some auxiliary materials. The quality of the aluminum alloy die casting raw material determines the quality of aluminum alloy castings.
Management of main material
1. receipt of aluminum alloy ingot
Based on the requirements of the air content and hard point in aluminum alloy, the aluminum ingot makers must ensure the refining, degassing, and slag removal process to prevent the air content and impurities in aluminum ingot from entering into the liquid die casting aluminum. After the incoming of the aluminum alloy ingot, the first is appearance inspection, requiring a smooth aluminum ingot surface without roughness, grease, mildew, oxide skin, fine and dense fracture structure of aluminum alloy ingot, etc. Server segregation, shrinkage cavity, slag, and inclusions are not allowed. Examine the content randomly from each batch and furnace number to ensure the content.
Produce products with specific requirements also need to examine others, such as when making products with mechanical property requirements and when the aluminum alloy ingot is delivered for production. It requires that tensile test bars should be submitted for each furnace. When producing products with air tightness requirements, it requires an increase in the detection of the pinhole of aluminum alloy ingot.
The types of the used aluminum alloy are not limited to one brand. There is a big chemical composition difference in the aluminum alloy of each brand. The main elements in the alloy of a brand might be seen as impurities in another one. For the coexistence of multiple brands, it is necessary to distinguish each brand of alloy visibly to prevent material mixing errors from happening. The typical measurement is to specify a clear and unified regulation on the color of aluminum alloy appearance coating of different brands and manufacturers. Different materials should be stored in the specified places.
2. Control of aluminum alloy melting process
Based on practice, enhancing the quality of the liquid aluminum alloy is the key to improving the quality of aluminum alloy castings. Thus, strict material management is essential, which should promise no unqualified raw materials in the workshop and production. All the processes must follow the standard guides of alloy melting. Strengthen the management of each raw material (new material, return material, and auxiliary material)
The aluminum alloy melting process has clear regulations about the melting temperature, smelting time, and feeding proportion of return material, especially the return material, which should be managed strictly according to the classification. Return material should be clean without grease, corrosion, sediment, moisture, inserts, etc. Aluminum ingot factories can carry out the remelting treatment if there is grease in the return material. Scattered aluminum blocks need to be screened. Cleans out the dust, sand, and impurities inside before using. Once the aluminum liquid uses return material, the ratio using refining agent and slag remover should be higher than only using aluminum alloy ingot to melt. In humid weather, the return material ratio should not be less than 30%. Increase the amount of return material in dry weather but should be less than 40%.
Slag removal and ventilation jobs should be done regularly to liquid aluminum after melting. After this, record the related coefficient. Check the chemical content in each pot of aluminum liquid when concentrated melting to make sure the chemical composition of products in the melting process is qualified. Besides, long-time fusion is not suggested because it will lead to high hydrogen content in aluminum alloy liquid, affecting the strength and airtightness of die casting products. Generally, the length of the whole process, from melting to die casting, is no more than 4 hours.
Are you looking for a zinc alloy die casting parts manufacturers?You can contact GREFEE.
Management of auxiliary material
1. Control of mold release agent
Mold release agent will make a smooth filling for liquid metal to be prepared for molding and a smooth, brightening, and plane surface quality. Apart from this, it also prevents mold sticking and has a big influence on the production speed, surface, and internal quality. Indeed, it protects mold by avoiding the impact of high-temperature liquid metal on the mold surface. Decreased thermal conductivity and mold temperature will extend the service life. When the mold opens, it is easy to release the molds and reduce the abrasion between punch heads, ejector rods, and moving areas. The control of the release agent includes not only the selection and proportion of the release agent itself but also the management of the use mode of spraying and drying of the release agent by operators. Generally, the selection of a release agent has the following requirements.
(1) good lubricity under high temperature and low volatilization point. Water in mold release agent volatilized soon under 100-150 degrees.
(2) it has no corrosion action to castings and aluminum alloy castings. Besides, due to stable properties, the mold release agent will not volatilize quickly.
(3) toxic gas free under high temperature and no scale on the die casting cavity surface.
Currently, a mold release agent is processed manually. Appropriate spraying guarantees quality, service life, and production efficiency. The spraying of the mold release agent also varies according to different properties of the mold release agent, dilute ratio, casting shapes, mold temperatures, etc. The mold release agent will form a protective layer on the mold surface from the shotgun. It takes long for this step before the next step, pouring, is the cause of loose castings. According to the die casting standards, a different type of mold release agent, or a different dilute ratio, the spraying time should be within a reasonable range. Operators are required to understand the upper limit and down limit of the coefficients and the affecting tendency to optimize the surface of castings.
Strictly controlling the mold release agent proportion is a must in using the water-based mold release agent. If the proportion of mold release agent and water is high, a thick layer is formed on the surface, which leads to an accumulation of agents. This further results in the ventilation rate and airtightness inside the castings decreasing. However, if the proportion of mold release agent and water is too thin, the effect is hard to achieve and will cause strain and mold sticking phenomenon.
Thus, in the quality control of the die casting workshop, mold release agent management impacts the quality significantly. The related regulations are essential, such as designating a person in charge of the proportion of release agent, clear regulations of the proportions of release agent and water in the production of castings, and allocating a specific person and specifying the certain quantity according to the preparation process of release agent. The operator must be trained strictly and follow the practice guidelines to avoid issues, such as over-spraying, less spraying, and missing spraying.
2.management of punch oil
Currently, most punch oil used are oil-based punch lubricants or particle lubrication. After the liquid aluminum enters the material barrel, it takes a short term to burn. The residual substance is distributed on the upper level of the liquid alloy, reducing the influence on products, or the gas and residuals generated from burning will enter the interior of products and product quality.
A simple method to test the punch oil is to inspect the color of the material handle. The thickness of the material handle is 1/3-1/4 of the diameter of the punch.
The length of blackening of punch oil should not exceed 3/5 thickness of the material handle. Meanwhile, the tip of the material handle should not be black ( black means an excessive residue of graphite powder), or products might have defects after processing, like air holes.
In the production process, the operator should also monitor the working conditions of the punch lubrication device. Too much or too less lubricate shortens the service life of the chamber and punch and affects the quality. The use amount of lubricating should give the first place to the lubricity and release of molds, especially when adopting the particle lubrication. No matter how to use the wax pill in a die casting mold, volatilization of organic matter exists. A large amount of the volatilized organic substance will cause the generation of air holes if they cannot be voided.
3. Management of punch
The punch and chamber are interdependent systems. Typically, the service life of the chamber is from 2 to 3 years. However, the service life might be as short as a shift or as long as ten thousand times. This difference results from quality inconsistency and production cost change. Therefore, the management of punch not only can ensure the quality of castings but also lowers the production cost.
(1) Punch size design under normal conditions. There is a specific coordination gap between the punch and chamber. Based on practice, the ideal distance is about 0.1mm. During injection, liquid aluminum will enter the gaps if the gaps are large, and the aluminum liquid leakage and smoke will appear, which will aggravate the wear of the punch and reduce its service life.
On the other hand, the punch will be stuck during the movement if the gap is too small. The punch speed will not reach the predetermined speed, the mold filling time will be prolonged, and the quality issues will increase. Thus, the manufacturing of punch should strictly follow the drawing so that the gap can be controlled within a reasonable range. At the same time, it extends its service life and improves its quality.
Gree has advantages in aluminium die casting and has more than 15 years of casting experience.
(2)The cooling of punch changes according to the temperature control of punch in die casting. With the temperature changing, the gap between the punch and chamber changes, too. These changes affect its service life and the stability of the injection process in die casting. So, it is necessary to ensure sufficient cooling for an ideal gap.
In designing, to fully cool the punch through the water core of the injection rod to take away the heat of the punch to the greatest extent to maintain the stability of the ideal gap between the punch and the pressure chamber. These measures are beneficial to ensure the stability of the injection process per mold and product quality. The injection system has sufficient punch cooling for a stable injection process and extends the service life. However, the sealing of the cooling water path of the punch must be firm to prevent the leakage of cooling water between the punch and ejector rod. Neglecting this issue will significantly affect the airtightness of products.
4. management of crucible
Using crucible is vital for aluminum alloy die casting, especially the cast-iron pot. Failing to operate according to the guidelines might lead to the content of Fe in aluminum alloy exceeding. According to our experience, brush the cast iron crucible with the crucible coating per the use requirements of the new pot, and once every three days during the use, the increase of Fe content will be less than 0.2% in the whole die-casting production process.
Provided the control of the incoming aluminum alloy ingots, it can fully ensure the alloy composition of die castings meets the standards. Although there is no concern about increasing the iron in graphite crucible use, it should be paid attention to, too. The drying process for the first use of the graphite crucible must be rigorously implemented because these operations will affect the service life of the graphite crucible. The service life of the graphite crucible without good preheating will be affected. Each graphite crucible is expensive and is directly related to the production cost.
Conclusion:In the quality management process, besides the management of raw material and auxiliary material, staff training, management of work, and technological improvement help solve quality issues in production. Applies the idea of comprehensive quality management into practice and guides the production with the systematic die casting production theories are a must for levitating the quality control in the workshop to a new level.
MORE BOLG
Categories
Try GREFEE now,for free
We keep your uploaded files confidential and secure.