How to Manage Die Casting Dies

Posted on : June 21, 2022 By GREFEE
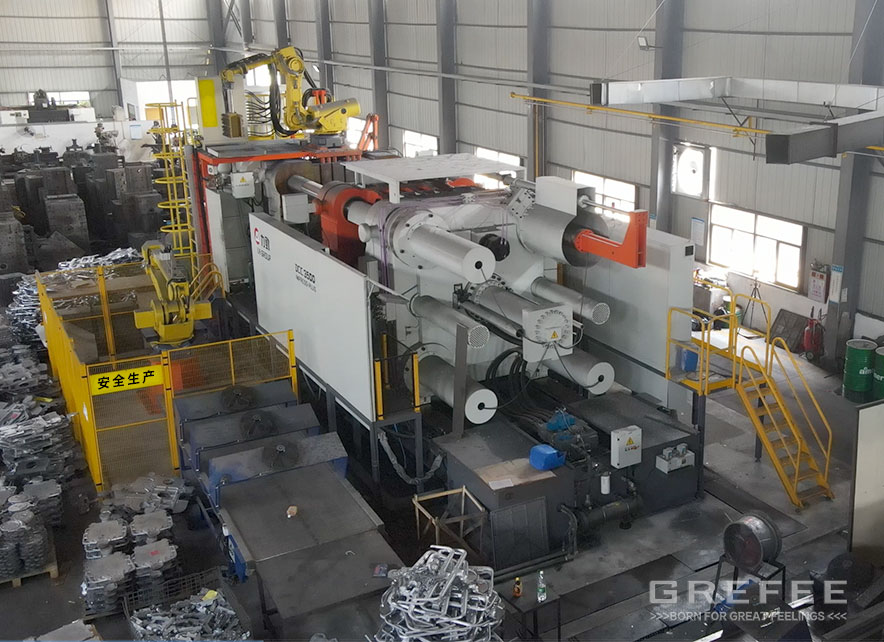
Die casting mold is one of the three indispensable factors in aluminum alloy die casting mold production. Its use of it determines the service life of die casting mold directly. The production rate and the quality of aluminum alloy castings determine the cost, especially the custom die casting molds. So, die casting mold manufacturers have come to realize that only by putting more effort into the management, the molds can be in good condition, and a smooth production cycle will be ensured.
Fine designing before mold fabrication for the sake of the mold and spare parts management
(1). In terms of the die casting mold, no matter whether it is an aluminum or zinc alloy die casting mold, many factors need to be considered in designing, like standardization, interchangeability, universality, and identifiability. These are essential for art mold die casting. For instance, select the die casting machine in one specification as far as possible for the whole chamber.
(2). Die casting machines with the same tonnage of oil cylinder joint, travel switch, water pipe, cooling oil pipe, and pre-reset rod should have unified specifications.
(3). If the mold with the oil cylinder core extractor is attached, the connector should be changed as soon as possible. We make sure that the core design should comply with the die casting mold design standards.
(4). Permanent marks should be marked on the mold, and the mold identification should at least include the part name, part drawing number, mold number, manufacturing time, manufacturer, etc. For instance, die casting mold made in China can be marked as “CHN”. Dimensional tolerance, finish, heat treatment, and numbering should be aligned with the specifications.
Establish (mold file) and storage area
(1). Each mold has a complete use record when incoming to the plant as it is a piece of important evidence for future maintenance and repair. Each item should be recorded carefully and clearly, including the acceptance status of new molds, off-site spot inspection records, maintenance records, production mold quality, etc.
(2). Aluminum alloy die-casting manufacturers have up to hundred sets of molds. How to find the mold that you need efficiently?
(3). One way is to position and carry out the partitioned storage. Produce the current situation board of mold storage position and specify the storage area. Typically, the mold that the die casting machine under 500T used is placed on the specific mold frame. The forklift can be used for homing. The mold that the die casing machine over 500T used is placed on the ground with the bottom padded with sleepers. It is forbidden to separate molds for storage to avoid damaging the working parts. Each set of mold should be marked with signs.
Regular mold maintenance
Responsibilities of mold repair team: the role of the repair team is in the maintenance and repairing of the molds. After one batch of a set of mold is completed, the quality department will carry out the inspection and report the issues to the superior supervisor.
Die casting mold maintenance principles:
(1). Inspect if there are any adhered metal chips, scratches, and ablation marks, on the mold cavity surface, and grind and polish the areas with these defects.
(2). Inspect carefully if there is any carking, crazing, scratches, and local depression on the mold cavity surface. If there are pits, undercuts on the wall towards the mold release direction. Slightly reticular crazing on the mold surface can be dealt with the electric spark tungsten electrode strengthening machine for strengthening and polishing. Large cracks, collapses, and pits must be welded, processed, polished and polished with die steel electrode after removing the bottom metal
(3). Pre-heat the mold cavity and slide to 180°C-250°C. Removing the stress and start annealing after welding.
(4). Check whether the ejector bar and core are bent. If there is any cracking and crazing. Replacing the bend and cracked core and ejector bar in time. The crazing on the cavity embosses area should be welded with the mold steel electrode and then progress, grind and polish before removing the bottom metal.
(5). Inspect whether the ejector bar can advance and retreat freely and whether it is stuck. Whether the ejector bar is higher than the profile. Whether the rod hole is drilled into the alloy. Any issue is found should be repaired and replaced in time;
(6). Inspect the coordination condition between the slides and slideways. If there is any alloy in the slideway, if the slide is intact, and if The gap between the slide and slideway is wide or not. If the gap is wide, weld the area or replace the slide. If the gap is small, narrow the gap to make it suitable for moving and remove the alloy inside the slideways at the same time.
(7). Carry out the painting inspection for the matching of the sliding block locking surface. Be aware of that whether there are mold barrens during production. Whether the inclined guide post hole is deformed; Whether the sliding block is stuck when coordinating with the inclined guide column; or Whether the sliding block is in place; Any issue is found should be repaired and replaced in time;
(8). Check the fit gap between the dynamic and static mold parting surface to keep the gap within the allowance range of 0.1mm. check whether the air duct on the parting surface is blocked and clean it when needed.
(9). Check whether the cooling system is blocked or leaked. Whether the water pipes connector is loose or damaged. Repairing in time if there is any blockage or leakage found.
(10). After the inspection, clean the residual and apply oil on the cavity, slideways, and guide pin surface of the die casting molds that are not used temporally before installation.
(11). The molds that have been inspected can only be produced after the first produced workpiece is qualified.
(12). During the repairing and maintenance process, the repair team should stick to one rule, which is to prohibit the change in the size of the mold without permission. Once the size changes, there will be quality issues in batches of molds. The loss is magnificent. For the polishing mold, polish where there is carbon deposit, and clean the wear on the mold caused by polishing as far as possible.
Mold spare parts management
To allow the mold repair staff to replace the parts in time, we can enhance the machine mobility, contract awarding, incoming, receiving, storage, and scrapping of the spare parts should be standardized. The first thing that needs to do is to make sure the quick-wear parts include a movable core, movable insert, ejector rod, gate sleeve, guide sleeve, and guidepost. The second is to establish the lowest storage amount of quick-wear parts. Principles: based on the monthly output, the strength of spare parts, the quantity of a single set of molds, and actual use. After that, formulate a list of quick-wear parts of the die-casting mold and the according list of quick-wear parts and mold core. The list of quick-wear parts must have the part name, drawing number, part number, quantity, minimum inventory, specification, etc. Each part number must be different to prevent mixing.
The table for the quick-wear parts and cores helps the mold repair personnel replace the spare parts. The warehouse management personnel should ensure the safety stock quantity of spare parts and check, numbering, register, incoming, and storage. The lowest storage quantity must be marked on the EXCEL. For spare parts lower than the lowest storage quantity, the warehouse management personnel should request and submit them to the supervisor for outsourcing. The commonly used spare parts and non-common used spare parts can be divided into zone A and B. Spare parts with common mold numbers in zone a; Spare parts with non-common mold numbers in zone B. Good management of mold is demonstrated by the comprehensive management level of die casting suppliers and companies. Professional management extends the service life of mold remarkably and saves cost.
MORE BOLG
Categories
Try GREFEE now,for free
We keep your uploaded files confidential and secure.