Four Main Factors of High Quality Zinc Alloy Die Casting

Posted on : July 12, 2022 By GREFEE
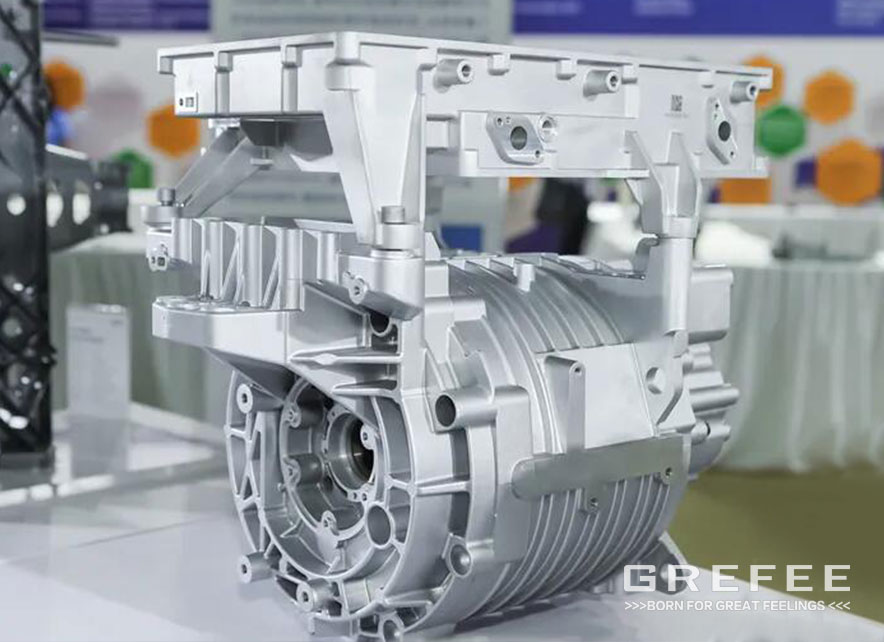
Die casting products is widely used in many industries. Most alloys are suitable for die casting. The physical and mechanical property of different alloys is heterogeneous, which provides convenience for the design of products.
The most common die casting includes zinc die casting and aluminum die casting. Other than that is magnesium, zinc-aluminum, copper, tin and lead alloys.
Zinc alloy die casting has a great significance in hot chamber die casting technique due to the excellent die casting and mechanical property. The advantages of zinc alloy include low melting point, easy to melt and temperature maintenance is easy. The cavity wall and the hot chamber extends the service life by receiving less heat. Besides, it demonstrates a great casting property, which does not absorb iron during melting and die casting, and it is not easy to stick. With its excellent normal temperature mechanical properties, wear resistance and excellent impact resistance, it is used in multiple die casting products, especially the thin shell products and products with smooth surface for electroplating and painting.
Non or less scraps high quality die casting is the ultimate mission in production. To reduce the defects and produce qualified zinc alloy die cast parts, the zinc alloy die casting parts manufacturers should start from the following four aspects.
1. Appropriate die casting machine
The die casting machine is the key in production, of which the property determines the quality of the castings. Appropriate machines ensure the quality of products, increase the production efficiency, lower the cost, and guarantee the safety. The property of the die casting machine is mainly based on the following two aspects:
(1)Sufficient clamping force: it is beneficial to avoid burrs when the metal flow pressure reaches its peak, and it also has resistance to bursting force to reduce the drop in production.
(2) Sufficient injection force: it ensures the die casting will not cause overheating or large overflow of the die. Moreover, it ensures the machine has sufficient capacity to transport enough molten metal, and fill the mold cavity with the required high inlet speed in a short time. On one hand, it can be selected according to the size, weight, and the complexity of the shapes (if the core pulling is required). On the other hand, the mold holding space of the die-casting machine is also a good reference.
The expansion force should be calculated strictly according to the injection area of the product (including the runner system)to select the die-casting machine with slightly larger clamping force. Some small die castings, such as electronic cigarette keys, intelligent equipment shells, and BWM pendants can be made into molds with multiple pieces in one mold. It is incorrect to think that a machine with large tonnage (large clamping force) means it has large pressure. On the contrary, concentrated pressure in the middle of the large template often occurs in the small area of the mold, leading to the damage to the die casting machine template and tooling, as well as a waste of resources, which does not meet the requirements of environmental protection.
2. Design of die casting die and runner system
The high pressure zinc die casting is often needed. Since the zinc alloy must fill out the cavity in 0.02-0.04s, the requirement for the design of the zinc die casting mold and runner system must be higher than the plastic mold. Multi-runner system can make the liquid metal fill the cavity in a certain way, which plays an important role in the controlling and adjustment of the aspects of flow direction, pressure transfer, filling time, exhaust conditions, and mold temperature distribution. Meanwhile, it is also the important factor which determines the surface quality and inner quality of the castings.
However, many manufacturers are used to making die-casting molds by making plastic molds. Consequently, the die-casting machine must be produced by high pressure, high speed, high temperature and increasing the clamping force, leading to defects like bubbles, cold shuts and shrinkage cavities. Other disadvantages include materials returned from the channel, low yield and high energy consumption. To obtain high-quality die castings and achieve the maximum die casting efficiency, an excellent runner system is indispensable. Since it can smooth the flow of molten metal in the mold cavity, minimize the pressure loss, and smoothly discharge the residual air to make high-quality castings in the most economical way.
(1) .The metal runner system consists of a series of pipes with different lengths and diameters. Under different high speeds, the molten zinc alloy is transmitted from the lower side of the injection plunger to the gate. Except for the changes in length and diameter, the direction changes occasionally, and each change consumes energy to overcome the resistance. Hence, the design of the runner system should converge from the gooseneck to the gate and avoid sharp corners. Besides, the surface of the flow path should be smooth to reduce resistance and maintain the flow speed of the liquid zinc alloy.
(2).Conical water inlet with main flow channel
(3)The main runner adopts ideal runner design. The cross section of different runner gradually shrinks at the direction of the flow, and being elliptic curve at the corner. A large bending radius should be at the bending area to reduce the resistance, lower the possibility of the gas trapping and cavitation at the downstream bend of the flow channel.
(4)Try to adopt long tapered tangent runner and thin gate, the ideal flow speed of the gate is 40-60m/s.
(5)Select appropriate venting pipes to reduce the overflow (stop position)
(6)Great thermal balance conditions between the cavity, wall thickness, and temperature.
3. Optimal zinc alloy material is the guarantee of the high quality products
Appropriately select zinc alloy material and correct scrap treatment to control the content of the impurities is beneficial to avoid the cracking due to the poor alloy composition and too high impurities, resulting in intergranular corrosion and affecting the mechanical property.
(1).Znal4-3 (No.2), znal4-3 (No.5) and znal4 are widely used due to the good comprehensive properties, excellent casting performance, good stability, little aging effect, good mechanical properties, reasonable price, and easy electroplating. Za-8 is a new type of zinc based alloy with high strength and high wear resistance, of which the tensile strength is 50%, higher than that of traditional zinc alloy. It also can replace aluminum alloy and copper alloy. Zinc die casting company GREFEE, based in China, uses stressed parts and wear-resistant parts with low cost with good economic benefits.
(2) Correctly smelt zinc alloy and strictly control the composition of zinc alloy. The melting of die-casting zinc alloy is essential to die-casting alloy. GREFEE uses the centralized melting furnace to melt the zinc alloy to make the ingot be evenly proportioned with the returned material. This also increases the use effectiveness of the the flux, so that the composition and temperature can be uniform and stable. If charging is directly performed in the hot chamber machine melting pot, the ground and reheating materials should be kept clean. It is best to preheat the alloy ingot on the furnace surface and discharge the slag in time. Zinc alloy products mixed with impurities will lead to serious intergranular corrosion.
The major composition and impurities in the zinc alloy have a big impact on the die casting product, which should be controlled and managed strictly. Aluminum is the major promotion. It can lower the melting point, improve the casting property, and enhance the alloy strength. Copper can enhance the stiffness and strength. Magnesium can compress the intergranular corrosion.
Due to the impurities in the zinc alloy. The iron composition has a low impact to alloy, whereas other impurities may be harmful and causes intergranular corrosion. Thus, GREFEE always strictly control the alloy content to avoid the impurity mixture because it is one of the keys in the zinc alloy die casting.
4.Correct operation and production & maintenance
Even with robust machines, die casting mold with proper runner design, and the best zinc alloy material, fail to manage, operating improperly or without maintenance cannot make the high quality products.
Machine is operated manually. Operators in GREFEE have all been professionally trained. Each of the operator must know and understand the property of each machine and product requirements, so that they can adjust the machine according to the corresponded data.
Before starting, check the computer screen to see whether all the data is normal, like oil lubrication, oil pressure gauge, nitrogen pressure, thermometer. If there is troubles, we need to remove them in time and adjust it before the non-load commissioning.
The die-casting mold should be in the center of the injection nozzle, and the mold adjustment and clamping should not be too tight. If there is no carry over in the die casting, lowering the clamping force properly to extend the service life of the elbow mechanism and die-casting die
Appropriately adjust the position of the slow shooting system to help the exhaust of the pressure shooting channel. Sufficient cooling time should be promised and do not blindly pursue speed to excessively shorten the full-automatic cycle time. The efficiency of the machine is highest when it can produce normally for a long time.
If allowed, the injection pressure, electric heating and melt temperature should be adjusted appropriately. After shutdown, do not close the cooling water. Disassemble the outward hammerhead and clean it. It is better to take one third of the molten liquid. Clean and inspect all parts of the machine.
The regular maintenance and repairing should be kept to avid any abnormal sound, loose screws, and deformation and dislocation of the parts.
A. Property difference: zinc alloy has low melting point, good flowability, which is easy to weld, braze and do plastic work. It has a good wear resistance under the air, making the exposed material easy to reuse and remelt. however, its brittleness is low and is more likely to cause dimensional changes due to natural aging. The hardness of the zinc alloy is 65 – 140. The tensile strength is 260-440. The aluminum alloy tensity is low and the strength is high. The property is similar or equal to some high quality steel with excellent plasticity, can be shaped into any profiles. Moreover, its great electric conductivity, thermal conductivity, and wear resistance make the zinc die casted parts such popular. The hardness of aluminum alloy is 45-90 and its tensile strength is 120-290.
B. Difference of the die casting: the melting temperature of the zinc alloy die castings is over 380 degrees, whereas the melting temperature of the aluminum alloy castings is over 600 degrees. The equipment of zinc and aluminum alloy is different.
C. Service life: the service life of the aluminum alloy castings is 10W, whereas that of the zinc alloy castings is 20W.
Generally, the process of both them is not big. We can know from the above that the zinc alloy is higher than aluminum alloy in aspects of hardness, tensile strength, material density and service life.
MORE BOLG
Categories
Try GREFEE now,for free
We keep your uploaded files confidential and secure.