Find the appropriate Oxidation treatment for your aluminum alloy parts.

Posted on : May 9, 2022 By GREFEE
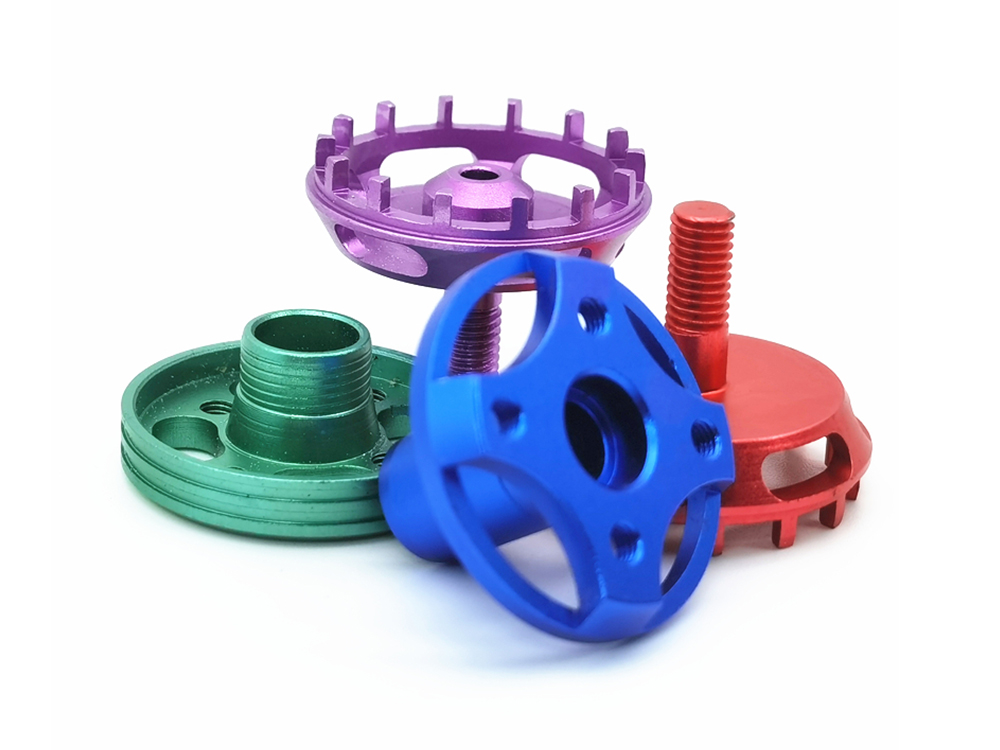
Anodic oxidation is one of the most common surface treatment methods for CNC aluminum parts, which accounts for a big share of the market. This processing suits aluminum parts manufactured by various techniques, such as CNC machining, die casting, and sheet metal forming.
Introduction of anodic oxidation
Anodic oxidation is processing that transfers the metal surface into the oxide film through an electrolytic process by which the thickness of the natural oxide film, the durability of parts, the adhesive force of paint, appearance, and corrosion resistance of the parts, and the service life are all increased.
In one type of thick layer anodic oxidation processing, the highest thickness of the oxide film can be 250 ~300 microns with great stiffness, whose micro-hardness of aluminum alloy can be 2452 ~ 4903 MPa, 11768~14710MPa on pure aluminum. What’s more, the hardness value of the internal layer is higher than that of the external layer. Due to the crevice between the layers, it can adhere to any kind of lubricates and increase the wear capacity. Its heat conductivity is poor, but corrosion resistance is high in the air, of which the melting point is as high as 2050℃
This process adopts the acid bath and current to form an anode layer on the base metal. Simply speaking, it is to adhere to an oxide film that is controllable and durable on the accessories rather than rely on the thin oxide film generated from the material. It is similar to bluing, phosphating, passivation, and other surface treatments of steels with great corrosion resistance and surface hardening.
Anodic oxidation classifications
Category I:
- Type I and IB –Chromic acid anodizing
- Type IC –Replace type I and IB non chromic acid anodizing
Category II:
- Type II – conventional coating for sulfuric acid bath
- Type IIB – non chromate alternatives to type I and IB coatings
Category III:
- Type III – hard anodizing
- Each type of anodic oxidation has specific reasons
(1). Type I, IB, II are all used for parts that have requirements on corrosion resistance and a certain degree of corrosion resistance, so for components that have specific needs for fatigue, select type I and IB as they are thin coating films, such as the connection and structural parts on airplanes.
(2). When I and IB require non-chromate alternatives, using type IC and IIB, which respond to the environmental protection.
(3). Type III is mainly for increasing the wear resistance, which is a thicker coating. So, it will be better than other types of wear. However, the coating may reduce the fatigue life. Type III anodic oxidation is usually used for gear, valves, and other sliding parts.
(4). Compared to nude aluminum, all types of cohesion are helpful with the bonding of paint and other adhesives. Besides the anodic oxidization processing, some parts might need to be colored, sealed, or processed by other materials such as dry film lubrication. If a component needs to be colored, it is categorized into type II, whereas an unstained part is a type I.
Design considerations
So far, you might be quite clear that when designing the anodic oxidization, one needs to consider the main factors, which are more likely to be ignored ( often being ignored to some extent).
1. Dimension
(1). The first factor we need to consider is the related dimension change to anodic oxidization parts. On the drawing, The engineer or designer may specify the application of dimensions after treatment to compensate for this change. However, for the rapid prototyping, we rarely rely on drawings, especially the rapid processing service, if we only rely on a solid model.
(2). In parts that have received anodic oxidization treatment, the surface will enlarge, which means the outer diameter will be bigger, and the holes will be smaller. This might be due to the surface expansion internally and externally when the anodic oxidation generates the oxide aluminum.
(3). The increase of the measured size might be 50% of the whole thickness of the anodic layer. The table below describes the range of different types of coating.
(4). According to specific alloy and processing control, the thickness varied. If the designer is aware of the increase in accuracy, the designer should pay much attention to it. Under some circumstances, thicker typer III coating could be grinder to the final size, but this increases the time and laboring cost. Another is the radius of edges and internal angle, for sharp corners are not the right place for the anodic coating generation, which is quite common for type III coating. The following is the corner radius for a given type III thickness according to Mil-A-8625
recommendations:
For thinner coating, 0.01-0.02 edge thickness is enough.Consult GREFEE’s process engineer for confirmation.
2. Wear resistance
(1). Anodic oxidation also leads to an oxide layer on the part’s surface.Hard anodizing increases the surface stiffness. If you have requirements on the surface wear resistance, hard-anodizing oxidation is a good choice. Hard anodizing of aluminum parts have high adhesive force. 50% of the oxide layer penetrates the internal of the aluminum alloy, and 50% adheres to the aluminum alloy surface, such as baseball bats, bicycle frames, and aluminum alloy flashlights. The initial solution of anode: after the hard-anodizing treatment, a 30-50μm thickness and 500HV stiffness layer forms on the aluminum alloy, which has excellent corrosion and wear resistance. The hard anodizing layer is toxin-free and harmless to the human body. Besides, it is durable and does not fade under high pressure and temperature, which provides an excellent decoration effect. It is widely applied to the inner tank of the rice cooker, packaging box of medical devices, air cylinder, oil cylinder, and printing roller. The whole technique will change its surface size to some extent. So, to gain a high-quality product, an accurate allowance calculation is necessary.
(2). In terms of this aspect, har anodizing oxidization factories must improve this technology. In many industries, for the convenience of mechanical machining, to comply with weight reduction trends and environmental protection requirements, some local parts of the current products use hard-oxidation of aluminum alloy to replace stainless steel. High quality and efficient hard-oxidation rigidity and the coating technology are a wide range: such as Thermochemical hard-oxidation technology; Physical vapor deposition; Chemical vapor deposition; Physicochemical vapor deposition technology; High energy in vitro hard-oxide coating technology; Diamond film coating; Multicomponent and multilayer composite coating technology; Hard oxidation modification, coating performance prediction and cutting technology. The layer is tough and has good wear resistance, whereas the layer generated by conductive oxidation is only 0.01-0.13 micron. Compared to hard anodizing, its wear resistance is not excellent.
3. Colored with dyes
Anodic oxide film can be colored. The advantages of this are: aesthetic satisfaction, reduction of stray light in optical system, and the contrast / recognition of the components in assembly.
When it involves the anodize oxidization, things you need to notice:
(1). Anodic oxide film can be colored. The advantages of this include aesthetic satisfaction, reduction of stray light in an optical system, and the contrast/recognition of the components in the assembly.
(2). Fade: the Anodic oxide film might be faded under the UV lines or high temperature. Organic dyes are more affected than inorganic dyes. However, many colors need organic dyes.
(3). Dye responsiveness: not all anodizing types and coating can be applied with dyes successfully. Type I anodizing cannot achieve the real black due to the thin coating. Typically, even with black dyes, the parts will still be grey, so the colored dyes might not be practical without specific treatments. When the coating is too thick, type III coating will be in dark grey or black on some alloys, so the color selection is limited. Multi-color might be acceptable for some thinner type III coatings. Type II coating is the optimal choice in terms of colors.
The details above are not comprehensive. If you have other equerries, can contact GREFEE for more information.
4. electric conductivity
(1). An anodic oxide layer is a good insulator even though the base metal has good electric conductivity. Thus, if ground the chassis, or the component, might need to coat a transparent chemical transmission layer to cover some areas.
(2). A method to confirm whether the aluminum parts have experienced anodic oxidation is with the digital multimeter to test the surface electrical conductivity. If the components haven’t received the anodizing treatment, they might have electric conductivity and low resistance.
5.composite coating
- The anodized parts could be secondarily machined to cover or process the anodized surface to enhance the properties. Some common additives of anodic coating are:
- Paint: the anodic coating can achieve specific colors that cannot be obtained through dyes. It might further increase the corrosion resistance.
- Teflon immersion: type III hard coating can be immersed by Teflon to lower the friction coefficient of bare anodizing, which can be finished in the mold cavities and sliding/contact parts.
- Other uncommon techniques can alter the properties of the anodic coating but might need professional suppliers.
Main considerations:
(1). Thick anodic coating might shorten the fatigue life of parts, especially when they adopt the type III process.
(2). We need to consider the geometrical alterations of anodically oxidized parts, which is essential for Type II and Type III but might not be necessary for type I.
(3). When dealing with multiple batches, it is hard to maintain color consistency, especially when working with different suppliers, which is more intricate.
(4). For complete corrosion protection, it might need to seal the holes of the anode layers separately.
(5). When the thickness is close to 0.003 inches, the wear resistance of Type II hard coating might decrease.
Different alloys adopt the same anodizing technique but with varied outcomes probably. For example, compared to other alloys, when the alloys whose copper content exceeds 2% or even higher receive the Mil specification test of type III coating, their wear resistance is poor. This also means the 2000 series aluminum material and type III hard coating of the partial 7000 series have poor wear resistance than 6061 hard coatings.
Try GREFEE now,for free
We keep your uploaded files confidential and secure.