Introduction to Aluminum Passivation

Posted on : February 16, 2022 By GREFEE
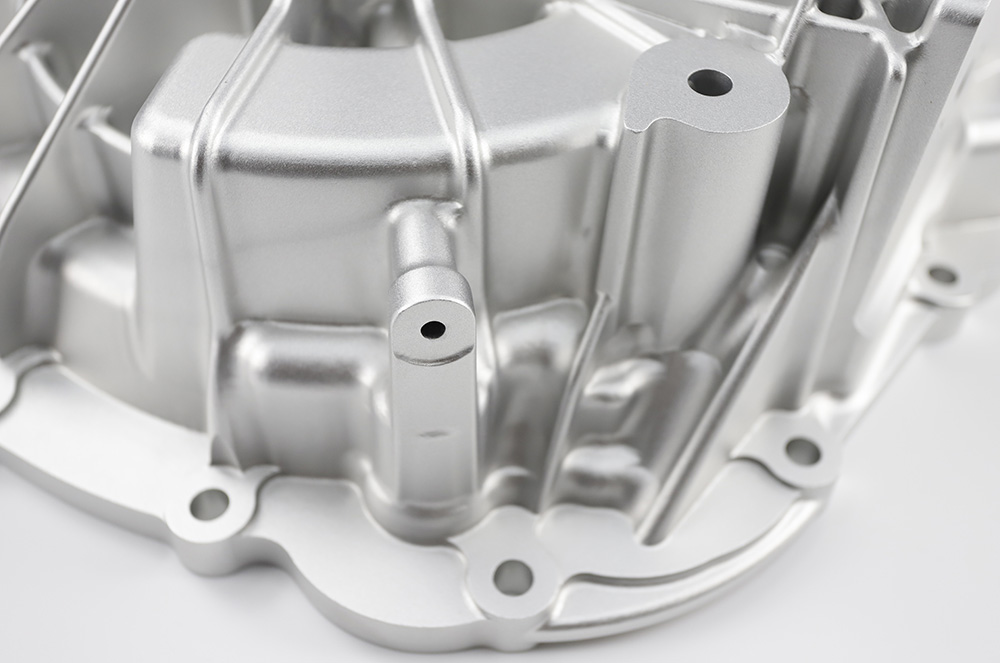
Aluminum Passivation refers to aluminum materials experiencing a type of oxidation treatment by the strong oxidation and electrical chemical methods to make the surface inactive. It is a method that can reduce the oxidation level of the aluminum surface and slow down the speed of surface corrosion. Besides, an active metal or alloy, the chemical activeness is significantly reduced and then turns into noble metal condition is called passivation.
It is difficult for many people to distinguish the aluminum passivation and aluminum anodization and regard them as the same post-treatment technology. Let’s take a look at the difference between aluminum passivation and aluminum anodization
Aluminum passivation refers to a chemical reaction of aluminum and aluminum products passivation solution that turns the active surface of the aluminum metal into an inactive surface to stop the reaction reacted by destructive substances from outside and the metal surface to prolong the time of aluminum rusting.
After the aluminum products have received passivation treatments, an aluminum passivation film will be formed on the surface, which is compact, has fine coverage, and is stuck to the metal surface stably.
The aluminum passivation film can prolong the rusting time, protect the metal effectively and make the metal is more erosion resistant. The aluminum passivation technology is simple, which can use for all kinds of corrosion resistance and anti-oxidation treatment of aluminum products and aluminum alloy.
Generally, the passivation only needs to be socked into the passivation solution for 1.5 minutes to reach its purpose. It is more cost-effective and time-saving. The process of aluminum passivation is a chemical reaction process, the color, size, and appearance of the aluminum surface will not be changed.
Meanwhile, a protective and anti-corrosion film will form on the surface of the aluminum products. It can maintain no discoloration and anti-oxidation in at least a minimum of 200 hours Salt Spray Test. (pics of the passivation solution)
- In line with RoHS environmental standards
- No heavy smoke, odorless
- Tintless or light color surface, fine metal toughness feelings
- Suits for dusting and gluing and other manufacturing prosses, high adhesion.
- Anti-corrosion increased by 5~20 times, ADC12 die cast aluminum can reach up to 72 ~ 168 hours of neutral salt spray test.
- Suits for Non-Hexavalent Chromium Passivation of aluminum die casting, aluminum profile and other products.
Aluminum anodizing is an electrolytic oxidation process in which the aluminum and aluminum alloy surface is changed into an oxidation film. This oxidation film has good performance of protection, decoration, and some other functional characteristics, which aim to overcome the aluminum alloy surface hardness, wear, and other defects.
It also expands its application range and prolonged service life. The surface treatment technology is an essential part of the aluminum alloy as well as aluminum anodizing technology is the most widely used and successful technology so far.
The aluminum passivation solution can form a protective and even passivation film on the surface of aluminum products timely. It can be applied to the anti-corrosion treatment of the aluminum alloyed aluminum die casting products.
A tintless and light color coating formed on the surface and can also work before the spraying, powder spraying, and gluing treatment.
Functions and features of aluminum passivation: the aluminum products have excellent anti-corrosion function and appearance after being processed by the aluminum passivation solution.
The white passivation film is both thick and impacts as well as maintains the aluminum products surface’s gloss. It is environmentally friendly and has no destructive substances, such as chromium ions and any heavy metal.
Physiochemical parameters:
- Appearance: transparent solution
- Proportion: 1.1±0.02
- PH value: acidcity
- Temperature: room temperature
- Intensity: stoste
- Time: 3~5 mins
Sock the clean aluminum products into the passivation solution for 3~5 minutes and dry them after rinsing with running water. Don’t overlap the products together before they are completely dry.
Passivation processing procedures of aluminum and aluminum alloy
Procedure notes
Operation contexts, equipments, tools
- Operation contexts and environments: passivation must be processed under the condition of good ventilation. closed workshops, or contexts with a possibility of fire and air pollution and risk areas.
- Material inside the cavity: plastic with acid-resisting, alkali-resisting, anti-corrosion properties.
- Clamp or rack materials: plastic with acid-resisting, alkali-resisting, anti-corrosion properties, titanium or stainless steel 316.
- Filtering; necessary (prolong the service life of passivation solution)
- Heating: the passivation solution temperature should be according to the requirements of products technology, water temperature.
- Maintenance: draw related program instruction and operation projects according to different requirements and products
- Ventilation: suggested
- Labour protection appliances: generally protection appliances used in the operation process, such as rubber gloves, masks when using chemical substances.
Test
Before putting the products into the salt and frog test box to test the ability of anti-corrosion, the products are placed under a condition of room temperature at a minimum of 24 hours.
Notes in the process of passivation:
Generally, many factors affect the quality of parts surface treatment. Except for the limits of the surface treatment technology, the basic quality of the parts is also another one. Thus, the first inspection of the process is essential — inspection of pretreatment of surface treatment.
Before the surface treatment, the surface quality of the parts determines the guarantee and supply of surface quality good or not. Thus, defects that affect the parts property, anti-corrosion quality and surface treatment procedures are not allowed to exist. Main parts defects include:
- Cracks, lamination, air holes, corrosion, scars, etc.
- Distortion, burrs, dry up residual cutting fluid, drilling cutting in the holes or runners, and hard edges that affect the assemble, etc.
- Cold-punched, cold extrusion, die casting manufacturing include oxide skin, lamination, cracks, mold release residue, coating, etc.
- Slags, welding residue, lines not being welded in the welding process.
- In the manufacturing process of rolling, polishing, brushing, there are scratches, burrs and parts that are not polished, polished, brushed and rolled which are beyond the standard, etc.
- The areas which are not painted, oxide skin, handprints, oil contamination, scratches or sand residue in the process of sandblasting.
- The heating treatment has oxide skin, salt residue, sinters, cracks and distortion, etc.
Therefore, before the aluminum passivation, the parts should be inspected carefully according to the process state of the parts. Control the defective parts before the surface treatment process.
Aluminum passivation methods
Passivation of metals in the environment can be achieved in two ways:
This passivation is due to the natural reaction of metal and passivator. Aluminum is easy to passivate in the air or oxidation solution, called spontaneous passivation. Except for oxidizing acid (concentrated sulfuric acid, concentrated nitric acid), when the medium contains strong oxidizing compounds such as silver nitrate, potassium chlorate, potassium dichromate, potassium permanganate, and other chemical substances, aluminum passivation will occur, and we call this type of chemical substance passivator.
The occurrence of passivation is not only determined by the oxidized ability but also related to the property of the anion in the oxidizer. For instance, the redox potential of potassium permanganate contains more anodic potentials than that of potassium dichromate. It is a stronger oxidizer; however, its function on iron passivation is lower than chromate. Peroxydisulfate has more anodic potentials than that of potassium dichromate. It is not able to make iron passivated.
Besides, although the occurrence of passivation is often related to oxidants. Some metals can passivate in non-oxidizing agents. For instance, magnesium can passivate in the hydrofluoric acid; molybdenum and niobium can passivate in hydrochloric acid; mercury and silver can passivate in the function of chloride ions.
Anode passivation
As the experiments show that aluminum passivation can also occur by the anodic polarization in the electrolyte fluid not containing active chloride ions. For instance, the aluminum will dissolve dramatically in the 20% sulfuric acid.
However, if applied impressed current to make it anodic polarization, when the polarization reaches 一0.1V(SCE), its dissolve speed will decrease to 1/10000 of the original speed and maintain high stability with the potential range of -0.1~+1.2V.
This passivation process is called anodic passivation or electrochemical passivation.in dilute sulfuric acid, iron, chromium, nickel, molybdenum, and other metals all can have anodic passivation results from the electrochemical passivation.
There are many definitions of passivation, conditions for the metal turn from active into passivated must contain:
The electrical potential of the metal move to the Positive direction to a large extent.
The electrical potential of the metA mutation occurs on the metal surface and forms the absorbed and phase-forming film.
The corrosion speed of passivated metals will largely decrease, which shows that the passivated metal featured with high corrosion resistance. Anode passivation and chemical passivation are the same as the occurrence of these phenomenons all arise from the mutation of the originally activated and dissolved metal surface.
This mutation makes the anodic dissolution process no longer follow the Tafel equation. It largely slows down the dissolving speed so the passivation refers to the mutation on the metal surface.
The state of metal passivation is called the state of being passive。 The properties of the passivated metal are called passivity。
Performance requirements after passivation of different manufacturing aluminum products:
Passivation solution property:
- A low toxic concentrated liquid based of Non-hexavalent chromium, trivalent chromium.
- Form transparent or light-colored conversion coating; corrosion resistance is higher than the hexavalent chromium passivation process.
- A passivation solution is easy to operate in dipping, spraying, and manual wiping.
- Apply the QPL qualified passivation solution, and the products even exceed the corrosion resistance standard of MIL-DTL-81706 and MILDTL5541. According to the neutral salt spray test standard of the ASTMB-117 and DINENIS9227, the bare film salt spray is over 150-360 hours after the passivation. Except for the fundamental processes, adding secondary treatment agent again, the bare film salt spray of aluminum die casting products is higher than 720 hours. The bare film salt spray of aluminum profile is higher than 1000 hours.
- The film formation is low contact resistance with high heat resistance and inorganic passivation film accorded with MIL-DTL-81706B whose resistivity is lower than 5000µOhm/square inch.
Property of film color:
Natural salt spray resistance index of passivation of the aluminum die casting products
- The color is the natural color of the aluminum, the natural salt spray can reach 48-72 hours, after secondary passivation, the salt spray can reach 72-96 hours.
- The color is wathet, the natural salt spray can reach 72-120 hours, after secondary passivation, the salt spray can reach 96-240 hours.
- The color is light blue, the natural salt spray can reach 120-168 hours, after secondary passivation, the salt spray can reach 240-360 hours.
- The color is based on blue, multi-color integrated, the natural salt spray can reach 168-240 hours, after secondary passivation, the salt spray can reach 360-480 hours.
- The color is steel grey, the natural salt spray can reach 240-360 hours, after secondary passivation, the salt spray is higher than 720.
- The color of the aluminum passivation products can be adjusted by the requirements of customers. Theoretically, it can produce any colors.
In conclusion, in processing aluminum material, aluminum profile, aluminum die casting parts, we will often need aluminum surface passivation treatment and varied types of passivation solutions. Each of them has different results.
GREFEE will provide the most professional aluminum passivation options according to your requirements about the aluminum products and test effect to ensure you have more qualified and high-quality products.
MORE BOLG
Categories
Try GREFEE now,for free
We keep your uploaded files confidential and secure.