What should be paid attention to in CNC machining of magnesium alloy parts?

Posted on : July 15 , 2022 By GREFEE
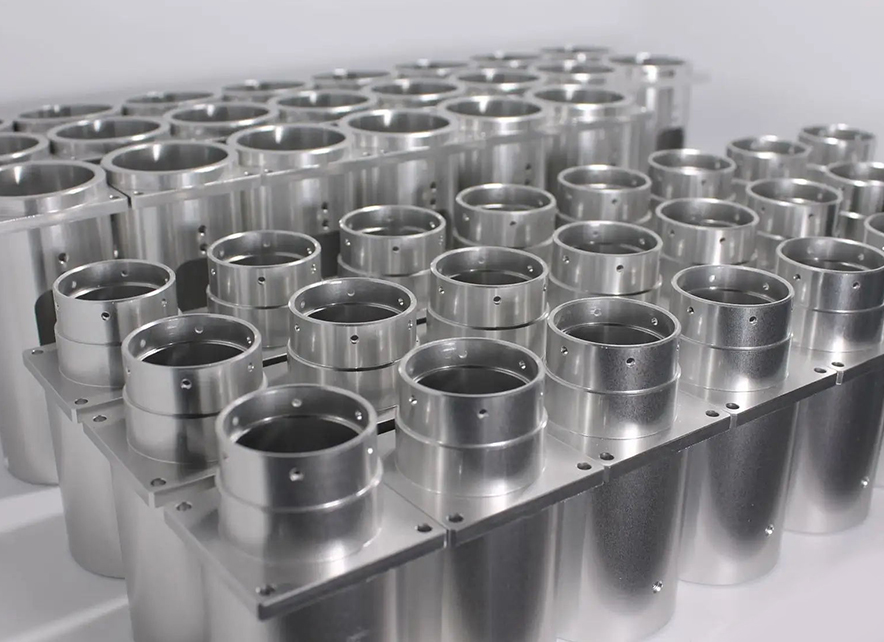
Definition of magnesium alloy
Magnesium alloy is an alloy based on magnesium and also includes other elements, which has high strength, large elastic modulus, good heat dissipation and shock absorption, greater impact load bearing capacity than aluminum alloy, and excellent resistance to organic and alkali corrosion.
CNC machining service of GREFEE metal cnc
Main application industry of magnesium alloy parts:
1.The magnesium is mainly used to produce automotive parts, such as seat bracket, instrument panel and bracket, electric window motor housing, sound housing, rear view mirror frame, etc
2. Automotive parts —— Shock absorber parts, frame, crank, flower shell, three / five way parts, wheel rim, brake handle, etc
3.telecommuting – notebook computer shell, MD shell, mobile phone shell, projector shell
4. Aerospace and national defense – Aerospace communicator and radar shell, aircraft landing gear wheel shell
5.Equipment and tools – control valve, camera housing, camera housing
Considerations of magnesium alloy processing
1. Risk factors during the mechanical processing
During the magnesium alloy mechanical processing, the chips and fine powders could lead to combustion or explosion. The size of chips are large during the preliminary processing stage. Since the heat conduction rate of magnesium is high, the friction heat can be exhausted rapidly, so it is hard to reach the burning point, resulting in less accidents possibilities. However, prior to the fine machining, the small chips and find powders generated have a large surface area, it is easily to cause them to burn and even lead to fire or explosion.
During the magnesium alloy processing, factors influencing chip temperature rise to flash point or combustion are as follows:
(1). The relationship between the processing speed and cutting speed. Under any given set of conditions, there is a possible feeding range and processing speed which could cause it to burn. The increase of feeding speed and cutting thickness will reduce the possibilities to burn. As long as the processing speed is low enough, the chips in any size will not to burn. The chips in any size will not to burn if the contact time between chips and tools are short and processing speed is high enough.
(2). The temperature of environment. The higher the temperature, the greater the possibility of fire.
(3). The composition and state of alloys. Compared to heterogeneous alloys, the homogeneous alloys are less likely to catch fire. The more uniform the alloy state is, the smaller the possibility of fire.
(4). Other factors, such as the feeding rate or the depth of cut are too small, the pause time is long during the processing, the rear corner and chip space of tools are small, the use of a high cutting speed without using cutting fluid, or sparks may be generated when the tool collides with the dissimilar metal core liner nested in the casting, the magnesium cutting chips around or under the lathe, etc.
2. Safety operation regulations for mechanical processing
(1). The cutting tool should be kept sharp and grind out a large relief angle and clearance angle. Blunt, chipped or broken tools are not allowed.
(2). Typically, try to use the large feeding amount and avoid micro feeding among to form chips with large thickness.
(3). Do not let the tool stop on the workpiece halfway.
(4). Use mineral oil coolant to reduce cooling when using micro cutting amount.
(5). If there is steel core lining in magnesium alloy parts, avoid sparks due to the collision with tools.
(6). A neat and clean environment is required.
(7). Smoking, fire making and electric welding is forbidden in the machining processing areas.
(8). Make sure that there is enough fire extinguisher stored in the working area.
3. Safety issues during the grinding processing
During the CNC machining of magnesium process, the magnesium powder is flammable and is easy to explode when it’s suspended in air, so any possible measures should be taken to ensure the collection and management of magnesium grinding powder are correct. When conduct dry grinding to magnesium alloy part, the magnesium slags should be removed from the working area by using correct designed wet dust collection system. The connector pipe between the vacuum and grinding machines should be short and straight, and the vacuum should be clean. besides, the exhaust gate should be outside of the room. The magnesium slags should be cleaned out in time to avoid too much residues. Before processing the slags, they should be stored in the water and a clean working environment is required, which is vital to ensure the safety of grinding magnesium alloy parts.
Check and clean the connecting pipes between the vacuum and emery cutter once daily at least and the whole vacuum system should be cleaned throughly once in a month at least. The magnesium powder should not be concentrated on the chairs, windows, pipes, and other surfaces. Too many vacuum equipments should not be connected with a concentrated exhaust system. The central dust collection system with long drying pipeline and the ordinary dust collection system with filter are not suitable for collecting magnesium powder. If the wet grinding of magnesium alloy parts is to be carried out on belt grinding device or disc grinder, sufficient cutting fluid should be used to collect all dust and transport it to the collection point. Thus, the following measurements need to be taken when carry out the grinding of magnesium alloy parts.
(1). There must be a specific grinding machine used for processing magnesium alloy parts, and labeled “magnesium special”on it. Before dressing the grinding wheel, clean the vacuum cleaner thoroughly.
(2). When reworking and grinding the surface of magnesium alloy parts washed with chromate, sparks may be caused, so there should not be any dust around.
(3). Grinding equipment operators should use smooth hats, smooth gloves and smooth flame-retardant clothes without pockets and cuffs. The aprons or protective clothes should be clean after using, dust-free and easy to take off.
(4). Warning signs should be placed in conspicuous place.
(5). There should be enough fire extinguishers in the working areas.
4. The treatment of magnesium chips and fine powder
The dry chips should be placed in a clean and sealed steel made containers, and without any contact with water. The wet chips and sludge should be stored in ventilation steel windows in remote places. Moreover, there should no enough exhaust space to allow the hydrogen gas being released. Place the wet chips and fine powder in the sealed containers is dangerous because high concentration of hydrogen gathering will cause explosion.
At present, the common treatment for the magnesium sludge, magnesium powder and sludges is to use the 5% ferric chloride solution to dissolve it (generally is 1kg dried magnesium needs 0.6kg ferric chloride). It can turn most of the magnesium into non-flammable magnesium hydroxide and magnesium chloride residues within few hours. Due to a generation of hydrogen in this reaction, so it should be conducted in an open container outdoors. It is strictly forbidden to make a fire, smoke or weld around the reactor. When preparing 5% ferric chloride solution, the water in the sludge should be taken into account.
5. Extinguishing of magnesium dust combustion
(1). Class D fire extinguishers.
The material is often the sodium chloride based powder or a passivated graphite based powder, of which the principle is to put out the fire by eliminating the oxygen.
(2). Covering agent or dry sand.
Small area fire can be covered by it, of which the principle is to put out the fire by eliminating oxygen.
(3). Cast iron chips.
Cast iron chips can be used when there is no other fire extinguisher materials. Its main function is to lower the temperature below the ignition point of magnesium, rather than put out the fire. In conclusion, no matter in which situation, water or other standard fire extinguishers cannot be used to put out fire caused by magnesium. Water and other fluid, such as carbon dioxide and foam will react with the burning magnesium, and it strengthens the fire.
MORE BOLG
Categories
Try GREFEE now,for free
We keep your uploaded files confidential and secure.