Causes analysis and improvement methods of shrinkage depression of die casting products

Posted on : March 24, 2022 By GREFEE
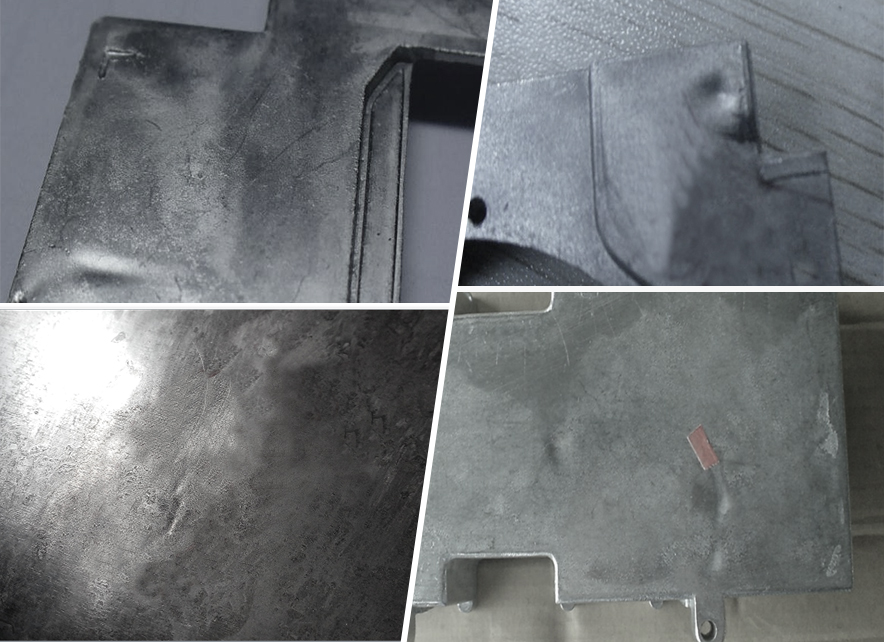
To learn more problems and preventions of die casting, click to check it out.
What is shrinkage depression in die casting?
When die casting products contract when they are cooled, during which the outer layer adheres to the core steel wall closely will be frozen first and generates the internal stress inside the parts. If the internal stress is too high, it leads to the metal material of the outer layer deforming. In other words, the outer layer will be depressed towards the inside. If the contraction and the outer layer deformation have been mature (as it is not cooled yet), no extra molten material need when holding the pressure, it will generate sedimentation between the wall of the mold and the outer layer of already solidified parts.
The sedimentation usually will be regarded as contraction. If the part has a thick section, contraction is likely to occur after mold release. As internal heat still exiting will penetrate the outer layer and heat it. The tensile stress created inside parts will make the heated outer layer settle inward, in which shrinkage depression occurs.
There are depressions on the smooth casting surface, which is in a natural cooling state.
Causes:
1.The improper structure design of casting part with big wall thickness difference and the thick sites, forming hot spot.
2.High contraction rate of alloy
3.The in-gate cross area is too small with inappropriate position.
4.Injection ratio is too low.
5.The local temperature of mold is too high.
6.Caused by the die casting mold damages and crazing
7.Caused by gas trapped. During the metal filling, the air discharges incompletely, so the air traps between the surface of the mold cavity and the metal level in contraction.
How to improve the shrinkage depression of casting surface?
Check the according to areas of products to see whether there is a big wall thickness difference and the thick wall areas or not. Discuss the detected issues with the product developer. Improves the structure of casting part to make a uniform wall thickness without affecting the functions of products. The connection which has a big wall thickness difference should be altered gradually to eliminate hot spots.
1. Takes the sample and uses the density detector to detect and observe the depression degree in sample solidification. Refines the liquid alloy.
2. The small in-gate section makes the far end of the casting part is not compacted sufficiently or appear the liquid metal streams to be docked. Observes if the in-gate position is at the place that facilitates the shrinkage and thick wall areas. Appropriately choose the alloy pouring position and enlarge the cross area of the in-gate properly.
3. The far end of casting part is not compact. – increases the injection pressure.
4. Uses the thermoprobe to check the temperature of the areas with defects. Appropriately adjusts the heat balance conditions of mold and uses temperature control device plus point cooling and other measures. Sprays painting this area for long and carry out forced cooling.
5. Observe whether there are any damaging protrusion and crazing according to areas of mold. Inspects and repairs the mold if it is server damaged.
6. Smooth depression surface with circular outline normally. It is different from other surfaces in terms of color. Improving the venting condition and the position of secondary injection should be farther with primary and secondary injection speed decreases appropriately,
Key inspection areas of casting parts
The shrinkage depression is usually at the thick wall area or areas with a value difference in wall thickness, of which the opposite side has long pillars or ribs.
How does shrinkage depression affect the products?
Shrinkage depression primarily affects the appearance of casting parts. Some products which need oil spraying, baking paint, or electroplating will suffer from worse depression issues.
How to know whether a die casting part with shrinkage depression is qualified or not?
The method detects if there is shrinkage depression on the part’s surface, which is mainly detected by visual or measurement tools for accurate results. Sometimes, the defects cannot be found by the eyes. If so, we can try to paint the product surface, after which the defects are easier to detect visually.
1. If the depression is on the outer layer of products or the surface of the die casting parts that need post-treatments is unqualified.
2. While in the internal of product, if the depth of depression ≤0.2mm and not affects the functions can be classified as qualified after customers confirmed.
3.when customers has requirements, follows the requirements.
Improves the problem of shrinkage depression
Generally speaking, the calculation of wall thickness percentage when designing is responsible for the shrinkage depression issue. Combining our years of experience, GREFEE found that 2-6MM wall thickness is the optimal range for die casting. To tick will lead to worse shrinkage depression. Besides, if there are pillars or RIB signs at the internal product, the ratio of product top surface and pillars and RIB should not exceed 0.7 times product top surface.
GREFEE has a professional die casting team. If you have inquiries about your die casting product design, contact us for a free assessment of our products. Choose GREFEE for perfect products.
MORE BOLG
Insert mold in injection mold service
What are advantages and disadvantages of Zinc alloy and Aluminum alloy?
Inspection standards for injection molded partappearance
How to judge the quality of your plastic products?
Inspection standards for CNC machining
To ensure that your products are 100% qualified
Categories
Try GREFEE now,for free
We keep your uploaded files confidential and secure.